Friday, October 20, 2017
As demand for liquefied petroleum gas continues to increase, particularly in the agricultural and transportation industries in the U.S., Modern Welding Co. Inc. is expanding its capabilities to produce LPG systems. The company is building a new state-of-the-art manufacturing plant in Fresno, Calif. to replace its current plant and significantly increase its ability to produce large LPG storage vessels. It currently has three manufacturing locations — in Fresno; Owensboro, Ky.; and Augusta, Ga., and six other underground and aboveground steel tank manufacturing subsidiaries in the U.S.
“With the clean fuels — green energy — we see a future for more propane and the need for more small and large propane pressure systems,” said Steve Fort, vice president of sales at Modern Welding Co. “We will now be able to serve the LPG needs of our customers in all of North America with our new plant, and we have the capacity to increase production as needed from our other manufacturing locations.”
Diverse Product Line
The new plant, operated by subsidiary Modern Custom Fabrication, will open in March 2018. In addition to LPG vessels, the facility will continue to produce Modern’s line of other steel products for upstream producers and midstream refiners requiring ASME pressure vessels and atmospheric tanks as part of their refining processes.
The LPG storage vessels produced by Modern Welding can hold from 3900 to 120,000 gallons, are available in both horizontal and vertical aboveground and underground configurations, conform to ASME standards, and allow for standard 250-psi operating pressure. In addition, the company partners with clients to custom-design systems to best meet their needs.
Modern Welding comments that LPG is quickly becoming a popular alternative source of fuel. It’s cleaner, more portable, and can be more cost-effective than other types of energy sources. LPG also greatly reduces greenhouse gas emissions from vehicles and electricity generation.
“We don’t know what’s going to be affecting our domestic fuel source, but we do know the U.S. has become a huge source of natural gas” said John Austin, vice president and manager at Modern Welding Co. of Owensboro. “Modern is preparing for the future with items we know.”
“Technology is another factor driving the growing LPG market. New vessels are manufactured from high-strength steel, which makes them lighter and more economical for transportation compared to systems that use refurbished older vessels, which are much thicker and heavier. These older vessels are often stored for 40 to 50 years and problems may occur if they are not evaluated properly prior to being returned to service,” said Jim Gray, vice president and manager of Modern Custom Fabrication.
In addition, Modern Welding’s LPG skid systems facilitate portability, allowing more flexibility for clients. “Sometimes our customers require these LPG units in ‘out-of-the-way’ places. Our skid system allows for set-up in a timely manner,” Austin explained. “These LPG vessels can be set up and pumping product in four to six hours versus potentially four to six weeks.” — Karen Massman VanAsdale
For more information about Modern Welding’s LPG systems, contact Steve Fort at (270) 685-4400 or This email address is being protected from spambots. You need JavaScript enabled to view it., or visit modweldco.com.
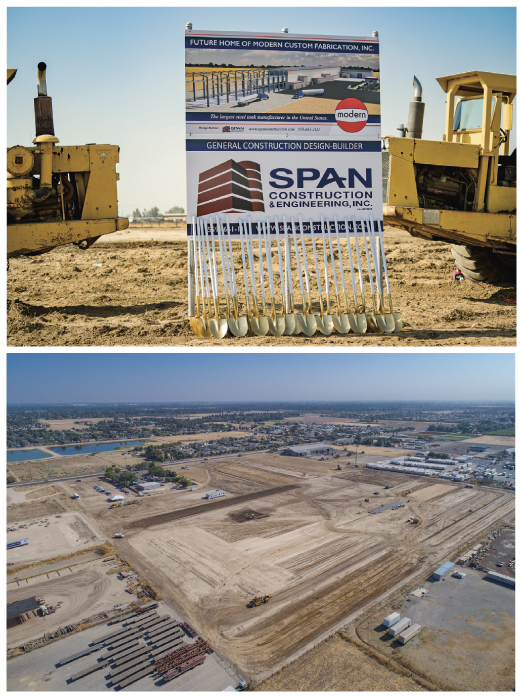
“With the clean fuels — green energy — we see a future for more propane and the need for more small and large propane pressure systems,” said Steve Fort, vice president of sales at Modern Welding Co. “We will now be able to serve the LPG needs of our customers in all of North America with our new plant, and we have the capacity to increase production as needed from our other manufacturing locations.”
Diverse Product Line
The new plant, operated by subsidiary Modern Custom Fabrication, will open in March 2018. In addition to LPG vessels, the facility will continue to produce Modern’s line of other steel products for upstream producers and midstream refiners requiring ASME pressure vessels and atmospheric tanks as part of their refining processes.
The LPG storage vessels produced by Modern Welding can hold from 3900 to 120,000 gallons, are available in both horizontal and vertical aboveground and underground configurations, conform to ASME standards, and allow for standard 250-psi operating pressure. In addition, the company partners with clients to custom-design systems to best meet their needs.
Modern Welding comments that LPG is quickly becoming a popular alternative source of fuel. It’s cleaner, more portable, and can be more cost-effective than other types of energy sources. LPG also greatly reduces greenhouse gas emissions from vehicles and electricity generation.
“We don’t know what’s going to be affecting our domestic fuel source, but we do know the U.S. has become a huge source of natural gas” said John Austin, vice president and manager at Modern Welding Co. of Owensboro. “Modern is preparing for the future with items we know.”
“Technology is another factor driving the growing LPG market. New vessels are manufactured from high-strength steel, which makes them lighter and more economical for transportation compared to systems that use refurbished older vessels, which are much thicker and heavier. These older vessels are often stored for 40 to 50 years and problems may occur if they are not evaluated properly prior to being returned to service,” said Jim Gray, vice president and manager of Modern Custom Fabrication.
In addition, Modern Welding’s LPG skid systems facilitate portability, allowing more flexibility for clients. “Sometimes our customers require these LPG units in ‘out-of-the-way’ places. Our skid system allows for set-up in a timely manner,” Austin explained. “These LPG vessels can be set up and pumping product in four to six hours versus potentially four to six weeks.” — Karen Massman VanAsdale
For more information about Modern Welding’s LPG systems, contact Steve Fort at (270) 685-4400 or This email address is being protected from spambots. You need JavaScript enabled to view it., or visit modweldco.com.