Wednesday, March 27, 2019
When it comes to both Department of Transportation (DOT) audits and road accidents, it’s never too early to work to prevent them and to prepare yourself to handle them if they do happen. That was the message delivered by three speakers at an education event held by J. J. Keller & Associates Inc., a provider of regulatory, safety, and compliance solutions to organizations of all sizes.
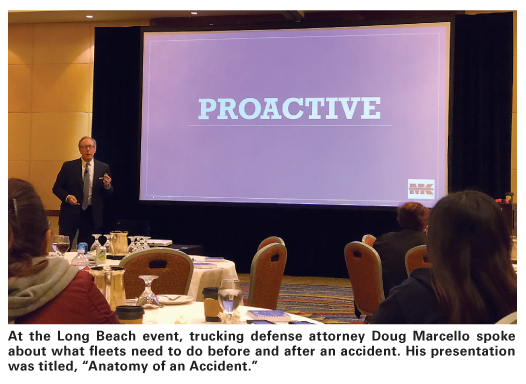
The 6-1/2-hour seminar, “DOT Audits — What You Need to Know,” was held Nov. 27, 2018, in Long Beach, Calif. It was one of many such events the company holds around the country, and it was complimentary to experienced fleet professionals. More than 70 executives, directors, and safety managers registered to attend the Long Beach event.
Preventing Audits
One segment of the gathering was presented by two J. J. Keller experts: Angela Rose-Lane, senior safety consultant, and Dennis Isherwood, account executive. They offered information on DOT audit-prevention strategies, guidance on implementing the Federal Motor Carrier Safety Administration’s (FMCSA) Safety Management Cycle within the Compliance, Safety, Accountability (CSA) Seven Basics, and how to take your safety programs to the next level.
When it comes to DOT audits, the message was, “The best way to survive an audit is to not have to go through one!” Rose-Lane explained that the audit selection process is not random; audits happen due to CSA Behavior Analysis and Safety Improvement Categories (BASICs) scores, complaints, follow-up, and crash investigations. The main reason for selection, she added, is CSA BASICs scores.
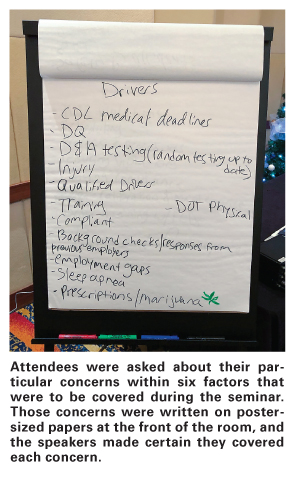
If you know why audits occur, you can work to prevent them and become a safer company in the process. For example, violations found in a roadside inspection are considered to offer a “snapshot” of the company’s compliance. They are part of a predictive pattern that can identify problems before an accident occurs, Rose-Lane said, “because they suggest the driver and the maintenance department are not doing their job.” Similarly, Isherwood explained that even a dirty truck, especially one that has a dirty windshield and headlights, signals that a company is not practicing “good housekeeping.” So, to help show your safety culture and provide less reason for an audit, make sure your vehicles are properly maintained.
To make sure drivers are thoroughly inspecting their vehicle before completing their driver vehicle inspection report (DVIR), Isherwood suggested sticking notes on the vehicle, on the areas that are supposed to be inspected, and requiring the driver to turn in those notes. Also, check the driver’s log; “If they got to the vehicle and then drove off two minutes later, they didn’t do a proper inspection,” Isherwood said.
If one of a company’s trucks has been found to have a violation, the company’s other trucks may be more likely to be pulled over as well. Rose-Lane said, inspectors figure that they are more likely to find violations on this company’s trucks, so they keep pulling them over until violations are no longer found. If a company’s trucks are being pulled over often, she added, “It’s not inappropriate to ask why, but how you do it makes all the difference.”
Hours-of-service (HOS) policies are a topic of special concern. Isherwood reported that the J. J. Keller editorial department receives about 3000 questions a month, and most have to do with HOS. The speakers suggested that companies make sure logs and supporting documents are submitted in a timely manner and filed in an organized manner, logs are audited, and drivers are counselled, corrected, and disciplined if necessary. E-logs have made this much easier, Isherwood said. “Because of e-logs, we’re getting a lot of data, and we’re getting it immediately,” he said. “If a driver misses a break, you know it, that day or the next.” An inspector will know it, too, when they see the logs. “You have the data, so act on it,” Isherwood suggested. “See if remedial training is required.”
Because CSA BASICs scores are based on a carrier’s performance compared to its peers, it’s also useful to have your PIN number for DOT and use it. The PIN number, Rose-Lane explained, lets you see information that is hidden to the public. That includes your rank in your peer group, so you can make sure your score isn’t making you stand out in the crowd; “You don’t want to be the zebra with red stripes!” she said.
Companies should also be familiar with DataQs and how to use it to report errors. “Sometimes inspectors make mistakes,” Rose-Lane said. As an example, she described an inspector being wrong about the correct way to secure propane cylinders in a vehicle. In a case like that, she said, the driver should correct the “violation” the way the inspector directs, but take pictures and report the inspector’s error later.
Preparing for Audits
When the speakers polled the audience at the Long Beach event, they found that more than half of those in the room had gone through a DOT investigation in the last three years. These included full investigations (29%), focused investigations (21%), and new-entrant investigations (6%). Of the remainder, 29% had not gone through an investigation and 15% were not sure (in most cases, because they hadn’t been with the company three years).
When a company is about to go through a DOT investigation, again, the key is preparation. For example, prepare your staff to locate, transfer, and prepare requested documents. To test how prepared they are, ask them how they would find such and such document. You, too, should be ready to get the documents. For example, if the inspector asks for the records of “a driver,” most companies want to give them the records of their best driver. To do that, you have to know beforehand who your best driver is, so it’s best to “keep your finger on the pulse of compliance,” Rose-Lane explained. This is also a good way to spot concerns on an ongoing basis, so you can correct them.
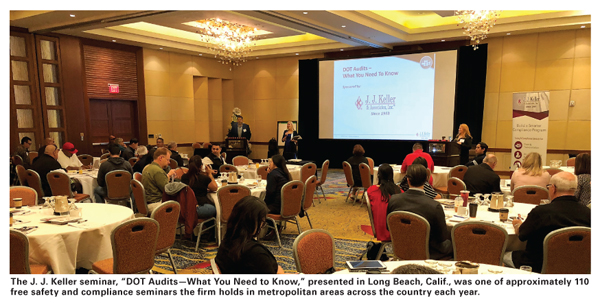
Preparation for an audit also includes preparing a work area, identifying a dedicated internal point of contact, and reviewing the process with your team. “An inspector who is convivial and mingles with staff can learn more [by] accident than in any other way,” Rose-Lane said, because staff members may share incorrect information or information that is not required during casual conversation. So, she suggested, treat the inspector as a guest, but also give them an office to use and train staff not to share information that is not requested.
An exit interview isn’t a required portion of an audit, but it’s often done and it can be useful to the company — especially if the audit has gone badly. Rose-Lane suggested that companies ask the inspector to discuss the findings at a high level and see if there are any shortfalls that the company can remedy before receiving the report.
Throughout the event, Rose-Lane and Isherwood made certain they were addressing all the issues the audience had come to hear about. Before their presentation began, members of the audience were given handouts listing six factors that were to be covered — general, drivers, operational, vehicle, hazardous materials, and accidents — and asked if they had any particular concerns within those areas. Those concerns were written in large print on poster-sized papers on an easel at the front of the room, and as the speakers finished their presentation on each of the six factors, they stopped to read from this paper and make certain they had covered each concern.
Preparing for Accidents
Another segment of the Long Beach event was presented by Doug Marcello, a trucking defense attorney who has a CDL. His firm, Marcello & Kivisto LLC (Carlisle, Pa.), provides trucking defense and transportation defense in cases in central Pennsylvania and throughout the country. His presentation, “Anatomy of an Accident,” focused on what fleets need to do before and after an accident.
“Prepare for an accident now; we as an industry know it’s going to happen,” Marcello said. “There are issues you can address ahead of time — before the trial, before the accident, before the truck leaves, and before the driver is hired. You can protect against threats we know are coming.”
When hiring, one thing to do is make sure all the information on a driver’s application is accurate. “The best evidence we have is a driver’s credibility,” Marcello said. Another thing is, require a road test, even though it is not required when the driver has a Commercial Driver’s License (CDL). Do the road test on a route that relates to routes the candidate will drive for your business, be it rural, urban, etc. “This is one more way to show that you have done everything you could have done,” Marcello said.
Another preparation is to use all the tools that are available to monitor drivers and vehicles, such as satellite positioning and in-cab cameras. Since drivers are employed to be on the road, Marcello said, “We are charged with supervising people we never see, who operate heavy equipment. But there are tools we can use. Know what data you have, monitor it, and use it.”
Immediately after an accident, the most important thing a driver can do is, not talk. “Drivers never talk their way out of trouble, but they often talk themselves into trouble,” Marcello said. “Too many drivers feel they need to explain what happened or make excuses.” Too often, he added, those excuses are something the other side’s attorney will say a professional driver should have known not to do.
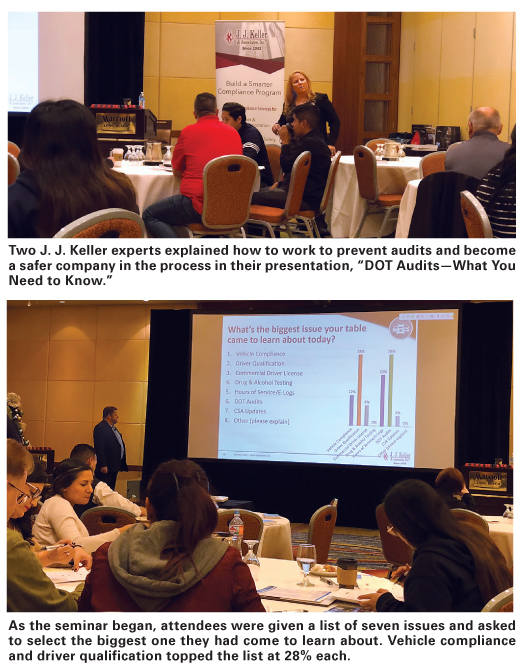
To attendees who gave him a business card at the Long Beach event, Marcello emailed five accident response forms: a non-reportable accident form; a list of post-accident dispatcher responsibilities; a list of post-accident document collection and retention; a photo checklist; and a rapid response program form that guides readers through putting together a list of emergency response providers, organizing an action plan, and preparing for post-accident action.
“Street Credibility”
After the Long Beach event, an attendee told BPN that the program covered a lot of material and that he will probably attend events like these again if given the opportunity.
“The cost of this training was incredible — free!” said Eric Stachowiak, gas distribution supervisor II at The City of Long Beach Energy Resources Department. “It was also conveniently located within two miles of my worksite.”
Stachowiak provides and oversees training for above-ground aspects of natural gas distribution, is a Veriforce Operator Qualification evaluator for the Gas Services Division, serves as Gas Services liaison to the safety department and safety officer, and is a certified Smith Syste driving instructor.
“Angela was very good,” he told BPN. “She has a lot of ‘street credibility,’ in my opinion. She was confident and knowledgeable. I felt like she was sharing the equivalent of ‘insider’ information regarding DOT inspections.”
“I liked that there was little or minimal salesmanship,” Stachowiak added. “I felt like the hardest sale (which was no sale) was from the lawyer, who was my favorite speaker. He has a scripted shtick, but was still able to passionately express his concerns about the topic. What I found most interesting was insurance does not cover ‘punitive damages’ and you need good records and are responsible for hiring competent people. I felt a little scared after his lecture.”
J. J. Keller holds approximately 110 events like this in metropolitan areas across the country each year. It has been offering free safety and compliance seminars covering DOT and other regulatory news for more than 10 years. Events are added monthly. For more information and to register for an event, visit jjkeller.com/events.
Doug Marcello offers a blog, a library of articles, and several other resources at the Marcello & Kivisto website, cdl-law.com. —Steve Relyea
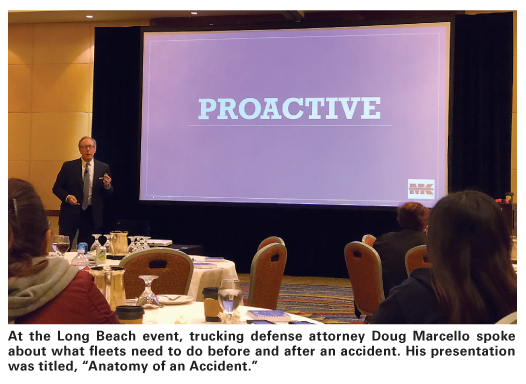
The 6-1/2-hour seminar, “DOT Audits — What You Need to Know,” was held Nov. 27, 2018, in Long Beach, Calif. It was one of many such events the company holds around the country, and it was complimentary to experienced fleet professionals. More than 70 executives, directors, and safety managers registered to attend the Long Beach event.
Preventing Audits
One segment of the gathering was presented by two J. J. Keller experts: Angela Rose-Lane, senior safety consultant, and Dennis Isherwood, account executive. They offered information on DOT audit-prevention strategies, guidance on implementing the Federal Motor Carrier Safety Administration’s (FMCSA) Safety Management Cycle within the Compliance, Safety, Accountability (CSA) Seven Basics, and how to take your safety programs to the next level.
When it comes to DOT audits, the message was, “The best way to survive an audit is to not have to go through one!” Rose-Lane explained that the audit selection process is not random; audits happen due to CSA Behavior Analysis and Safety Improvement Categories (BASICs) scores, complaints, follow-up, and crash investigations. The main reason for selection, she added, is CSA BASICs scores.
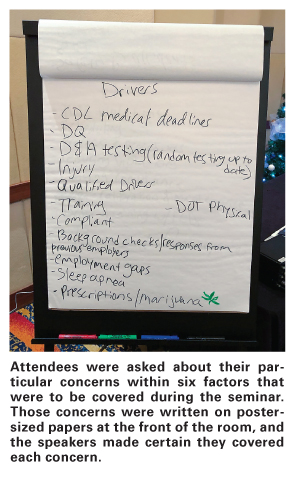
If you know why audits occur, you can work to prevent them and become a safer company in the process. For example, violations found in a roadside inspection are considered to offer a “snapshot” of the company’s compliance. They are part of a predictive pattern that can identify problems before an accident occurs, Rose-Lane said, “because they suggest the driver and the maintenance department are not doing their job.” Similarly, Isherwood explained that even a dirty truck, especially one that has a dirty windshield and headlights, signals that a company is not practicing “good housekeeping.” So, to help show your safety culture and provide less reason for an audit, make sure your vehicles are properly maintained.
To make sure drivers are thoroughly inspecting their vehicle before completing their driver vehicle inspection report (DVIR), Isherwood suggested sticking notes on the vehicle, on the areas that are supposed to be inspected, and requiring the driver to turn in those notes. Also, check the driver’s log; “If they got to the vehicle and then drove off two minutes later, they didn’t do a proper inspection,” Isherwood said.
If one of a company’s trucks has been found to have a violation, the company’s other trucks may be more likely to be pulled over as well. Rose-Lane said, inspectors figure that they are more likely to find violations on this company’s trucks, so they keep pulling them over until violations are no longer found. If a company’s trucks are being pulled over often, she added, “It’s not inappropriate to ask why, but how you do it makes all the difference.”
Hours-of-service (HOS) policies are a topic of special concern. Isherwood reported that the J. J. Keller editorial department receives about 3000 questions a month, and most have to do with HOS. The speakers suggested that companies make sure logs and supporting documents are submitted in a timely manner and filed in an organized manner, logs are audited, and drivers are counselled, corrected, and disciplined if necessary. E-logs have made this much easier, Isherwood said. “Because of e-logs, we’re getting a lot of data, and we’re getting it immediately,” he said. “If a driver misses a break, you know it, that day or the next.” An inspector will know it, too, when they see the logs. “You have the data, so act on it,” Isherwood suggested. “See if remedial training is required.”
Because CSA BASICs scores are based on a carrier’s performance compared to its peers, it’s also useful to have your PIN number for DOT and use it. The PIN number, Rose-Lane explained, lets you see information that is hidden to the public. That includes your rank in your peer group, so you can make sure your score isn’t making you stand out in the crowd; “You don’t want to be the zebra with red stripes!” she said.
Companies should also be familiar with DataQs and how to use it to report errors. “Sometimes inspectors make mistakes,” Rose-Lane said. As an example, she described an inspector being wrong about the correct way to secure propane cylinders in a vehicle. In a case like that, she said, the driver should correct the “violation” the way the inspector directs, but take pictures and report the inspector’s error later.
Preparing for Audits
When the speakers polled the audience at the Long Beach event, they found that more than half of those in the room had gone through a DOT investigation in the last three years. These included full investigations (29%), focused investigations (21%), and new-entrant investigations (6%). Of the remainder, 29% had not gone through an investigation and 15% were not sure (in most cases, because they hadn’t been with the company three years).
When a company is about to go through a DOT investigation, again, the key is preparation. For example, prepare your staff to locate, transfer, and prepare requested documents. To test how prepared they are, ask them how they would find such and such document. You, too, should be ready to get the documents. For example, if the inspector asks for the records of “a driver,” most companies want to give them the records of their best driver. To do that, you have to know beforehand who your best driver is, so it’s best to “keep your finger on the pulse of compliance,” Rose-Lane explained. This is also a good way to spot concerns on an ongoing basis, so you can correct them.
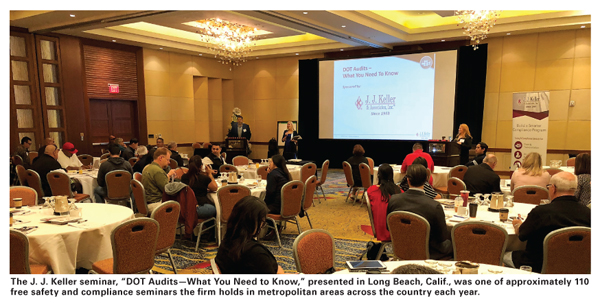
Preparation for an audit also includes preparing a work area, identifying a dedicated internal point of contact, and reviewing the process with your team. “An inspector who is convivial and mingles with staff can learn more [by] accident than in any other way,” Rose-Lane said, because staff members may share incorrect information or information that is not required during casual conversation. So, she suggested, treat the inspector as a guest, but also give them an office to use and train staff not to share information that is not requested.
An exit interview isn’t a required portion of an audit, but it’s often done and it can be useful to the company — especially if the audit has gone badly. Rose-Lane suggested that companies ask the inspector to discuss the findings at a high level and see if there are any shortfalls that the company can remedy before receiving the report.
Throughout the event, Rose-Lane and Isherwood made certain they were addressing all the issues the audience had come to hear about. Before their presentation began, members of the audience were given handouts listing six factors that were to be covered — general, drivers, operational, vehicle, hazardous materials, and accidents — and asked if they had any particular concerns within those areas. Those concerns were written in large print on poster-sized papers on an easel at the front of the room, and as the speakers finished their presentation on each of the six factors, they stopped to read from this paper and make certain they had covered each concern.
Preparing for Accidents
Another segment of the Long Beach event was presented by Doug Marcello, a trucking defense attorney who has a CDL. His firm, Marcello & Kivisto LLC (Carlisle, Pa.), provides trucking defense and transportation defense in cases in central Pennsylvania and throughout the country. His presentation, “Anatomy of an Accident,” focused on what fleets need to do before and after an accident.
“Prepare for an accident now; we as an industry know it’s going to happen,” Marcello said. “There are issues you can address ahead of time — before the trial, before the accident, before the truck leaves, and before the driver is hired. You can protect against threats we know are coming.”
When hiring, one thing to do is make sure all the information on a driver’s application is accurate. “The best evidence we have is a driver’s credibility,” Marcello said. Another thing is, require a road test, even though it is not required when the driver has a Commercial Driver’s License (CDL). Do the road test on a route that relates to routes the candidate will drive for your business, be it rural, urban, etc. “This is one more way to show that you have done everything you could have done,” Marcello said.
Another preparation is to use all the tools that are available to monitor drivers and vehicles, such as satellite positioning and in-cab cameras. Since drivers are employed to be on the road, Marcello said, “We are charged with supervising people we never see, who operate heavy equipment. But there are tools we can use. Know what data you have, monitor it, and use it.”
Immediately after an accident, the most important thing a driver can do is, not talk. “Drivers never talk their way out of trouble, but they often talk themselves into trouble,” Marcello said. “Too many drivers feel they need to explain what happened or make excuses.” Too often, he added, those excuses are something the other side’s attorney will say a professional driver should have known not to do.
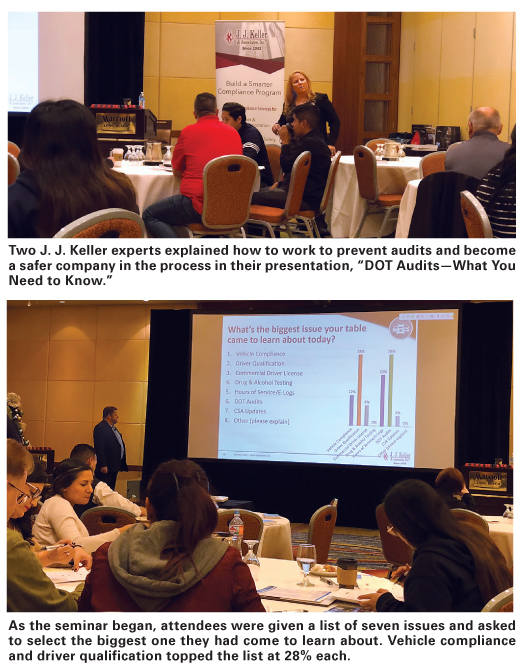
To attendees who gave him a business card at the Long Beach event, Marcello emailed five accident response forms: a non-reportable accident form; a list of post-accident dispatcher responsibilities; a list of post-accident document collection and retention; a photo checklist; and a rapid response program form that guides readers through putting together a list of emergency response providers, organizing an action plan, and preparing for post-accident action.
“Street Credibility”
After the Long Beach event, an attendee told BPN that the program covered a lot of material and that he will probably attend events like these again if given the opportunity.
“The cost of this training was incredible — free!” said Eric Stachowiak, gas distribution supervisor II at The City of Long Beach Energy Resources Department. “It was also conveniently located within two miles of my worksite.”
Stachowiak provides and oversees training for above-ground aspects of natural gas distribution, is a Veriforce Operator Qualification evaluator for the Gas Services Division, serves as Gas Services liaison to the safety department and safety officer, and is a certified Smith Syste driving instructor.
“Angela was very good,” he told BPN. “She has a lot of ‘street credibility,’ in my opinion. She was confident and knowledgeable. I felt like she was sharing the equivalent of ‘insider’ information regarding DOT inspections.”
“I liked that there was little or minimal salesmanship,” Stachowiak added. “I felt like the hardest sale (which was no sale) was from the lawyer, who was my favorite speaker. He has a scripted shtick, but was still able to passionately express his concerns about the topic. What I found most interesting was insurance does not cover ‘punitive damages’ and you need good records and are responsible for hiring competent people. I felt a little scared after his lecture.”
J. J. Keller holds approximately 110 events like this in metropolitan areas across the country each year. It has been offering free safety and compliance seminars covering DOT and other regulatory news for more than 10 years. Events are added monthly. For more information and to register for an event, visit jjkeller.com/events.
Doug Marcello offers a blog, a library of articles, and several other resources at the Marcello & Kivisto website, cdl-law.com. —Steve Relyea