Monday, March 25, 2019
When the hydrostatic pressure test requalification period for some bobtails was extended in 2016 from five years to 10 years, a burden was removed from propane marketers. At the same time, though, that extension may allow problems on improperly maintained bobtails to fester for an additional five years.
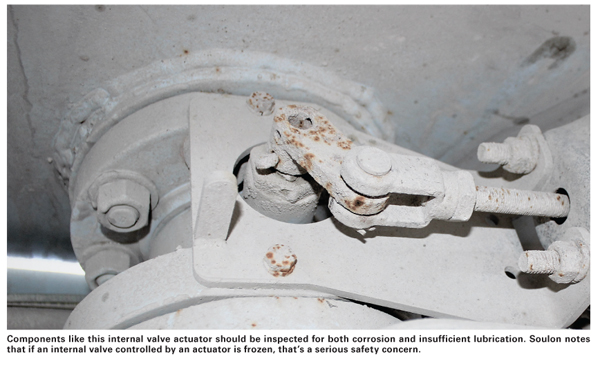
Jason Soulon, sales manager, southwest region at Westmor Industries (Morris, Minn.), has seen what can happen when people get lax with inspections and maintenance. He has 20 years of experience designing, selling, and servicing bobtails. Westmor Industries not only manufactures bobtails, transports, and other equipment, but also offers repairs, tests, and inspections at seven locations in the Midwest and the Eastern United States.
“When we have a bobtail in the shop to perform a hydrostatic pressure test, we crawl all over it as part of the requalification process,” Soulon explains. “If that bobtail has been maintained at a shop that is not so attentive, we find problems they have missed. If we find a problem at year five, it may cost several thousand dollars, but we can repair it. But if we are now finding that problem at year 10, it may cost $10,000 plus or the tank may be beyond repair — it may cost more to repair than the tank is worth.”
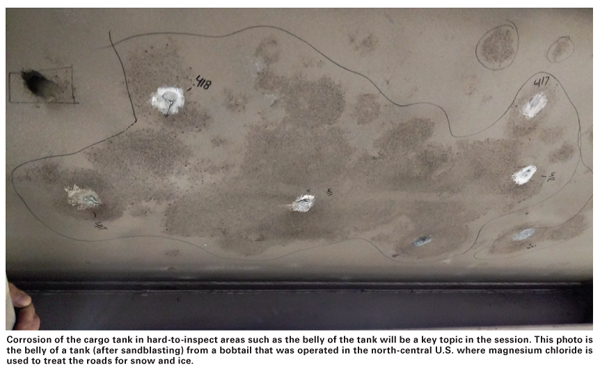
“The extension has made daily, weekly, quarterly, and yearly PMs [preventative maintenance services] and inspections more important than ever,” he adds. “You don’t want to become complacent; you want to be vigilant about these inspections.”
Soulon will explain the “why, how, and when” of cargo tank maintenance in a seminar at the National Propane Gas Association (NPGA) expo in April. Offering a preview of the seminar to BPN, he said the safety concerns resulting from poor preventative maintenance fall into six categories: tank corrosion; abrasions and physical damage; insufficient lubrication; inoperative controls; meter creep testing; and hose testing.
Tank corrosion is a problem commonly seen if inspection and maintenance has been neglected. The longer the corrosion goes undetected, the deeper it gets in the tank, and the more costly it will be to repair. Abrasions and physical damage may include, for example, a hose that has been dragged on the ground and is now damaged. Insufficient lubrication can cause the failure of a variety of components, including pumps, hose reels, power take-off (PTO) drive shafts, valves, and actuators. Inoperative controls can be a safety concern. “If an internal valve controlled by an actuator is frozen, that’s a serious safety concern,” Soulon notes.
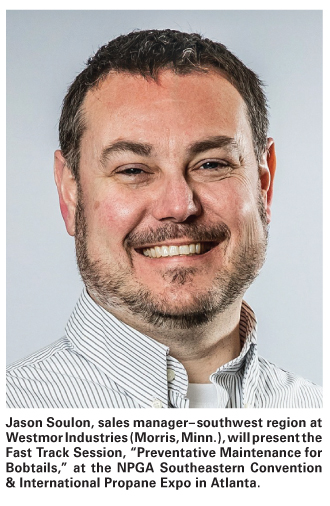
To prevent or spot these problems, he suggests performing thorough visual inspections and adhering to a comprehensive preventative maintenance plan covering those six categories. Many of the components found on a bobtail have a maintenance schedule provided by the manufacturer; it’s important that fleets adhere to those schedules. In the past many bobtails came with a stack of papers that often got lost, but today most of the information can be retrieved on demand with just a few clicks.
“Prior to the change in the law, every bobtail had to requalify every five years, and that is a very thorough process,” Soulon says. “Now, every bobtail still has an annual visual inspection and leakage test, but sometimes it is easy to overlook things during that inspection — especially if they are under the bobtail and it’s difficult and dirty to get at them. Rock salt, and other road treatment chemicals such as magnesium chloride, are very corrosive and when these spray up from the tires, it gets into every nook and cranny. If you don’t get under the bobtail with a flashlight and perform a thorough visual inspection, then corrosion could become an issue.”
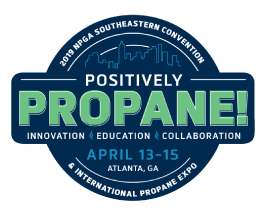
Cargo tank maintenance and other bobtail maintenance will only become more important in coming years. While the rule of thumb used to be that a marketer would keep a bobtail for seven years, Soulon says, that is now the bare minimum; today, some marketers keep a bobtail for as long as 15 years. “The price of bobtails has increased faster than the cost of most other things, due to the cost of steel and other components, so marketers are running them longer.”
During his seminar, in addition to explaining how to properly maintain today’s bobtails, Soulon will show actual components that Westmor technicians have removed from bobtails and will offer advice on attendees’ existing maintenance programs. This Fast Track Session, “Preventative Maintenance for Bobtails,” is scheduled for Sunday, April 14, from 3:15 to 4:00 p.m. at the NPGA Southeastern Convention & International Propane Expo in Atlanta. —Steve Relyea
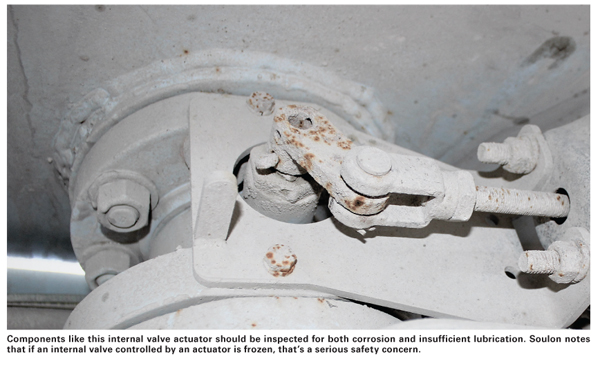
Jason Soulon, sales manager, southwest region at Westmor Industries (Morris, Minn.), has seen what can happen when people get lax with inspections and maintenance. He has 20 years of experience designing, selling, and servicing bobtails. Westmor Industries not only manufactures bobtails, transports, and other equipment, but also offers repairs, tests, and inspections at seven locations in the Midwest and the Eastern United States.
“When we have a bobtail in the shop to perform a hydrostatic pressure test, we crawl all over it as part of the requalification process,” Soulon explains. “If that bobtail has been maintained at a shop that is not so attentive, we find problems they have missed. If we find a problem at year five, it may cost several thousand dollars, but we can repair it. But if we are now finding that problem at year 10, it may cost $10,000 plus or the tank may be beyond repair — it may cost more to repair than the tank is worth.”
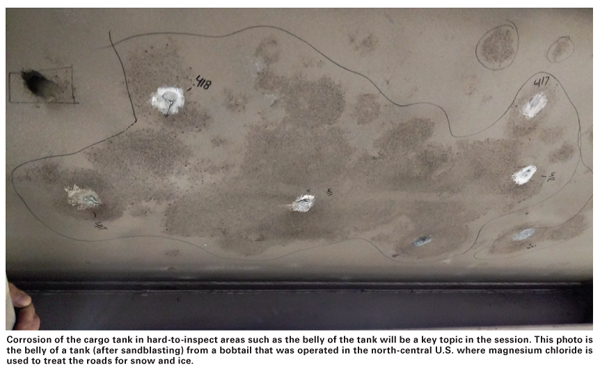
“The extension has made daily, weekly, quarterly, and yearly PMs [preventative maintenance services] and inspections more important than ever,” he adds. “You don’t want to become complacent; you want to be vigilant about these inspections.”
Soulon will explain the “why, how, and when” of cargo tank maintenance in a seminar at the National Propane Gas Association (NPGA) expo in April. Offering a preview of the seminar to BPN, he said the safety concerns resulting from poor preventative maintenance fall into six categories: tank corrosion; abrasions and physical damage; insufficient lubrication; inoperative controls; meter creep testing; and hose testing.
Tank corrosion is a problem commonly seen if inspection and maintenance has been neglected. The longer the corrosion goes undetected, the deeper it gets in the tank, and the more costly it will be to repair. Abrasions and physical damage may include, for example, a hose that has been dragged on the ground and is now damaged. Insufficient lubrication can cause the failure of a variety of components, including pumps, hose reels, power take-off (PTO) drive shafts, valves, and actuators. Inoperative controls can be a safety concern. “If an internal valve controlled by an actuator is frozen, that’s a serious safety concern,” Soulon notes.
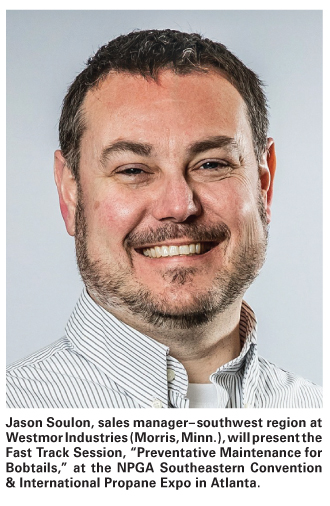
To prevent or spot these problems, he suggests performing thorough visual inspections and adhering to a comprehensive preventative maintenance plan covering those six categories. Many of the components found on a bobtail have a maintenance schedule provided by the manufacturer; it’s important that fleets adhere to those schedules. In the past many bobtails came with a stack of papers that often got lost, but today most of the information can be retrieved on demand with just a few clicks.
“Prior to the change in the law, every bobtail had to requalify every five years, and that is a very thorough process,” Soulon says. “Now, every bobtail still has an annual visual inspection and leakage test, but sometimes it is easy to overlook things during that inspection — especially if they are under the bobtail and it’s difficult and dirty to get at them. Rock salt, and other road treatment chemicals such as magnesium chloride, are very corrosive and when these spray up from the tires, it gets into every nook and cranny. If you don’t get under the bobtail with a flashlight and perform a thorough visual inspection, then corrosion could become an issue.”
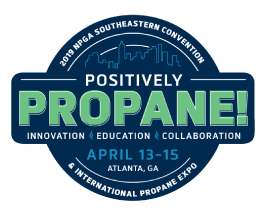
Cargo tank maintenance and other bobtail maintenance will only become more important in coming years. While the rule of thumb used to be that a marketer would keep a bobtail for seven years, Soulon says, that is now the bare minimum; today, some marketers keep a bobtail for as long as 15 years. “The price of bobtails has increased faster than the cost of most other things, due to the cost of steel and other components, so marketers are running them longer.”
During his seminar, in addition to explaining how to properly maintain today’s bobtails, Soulon will show actual components that Westmor technicians have removed from bobtails and will offer advice on attendees’ existing maintenance programs. This Fast Track Session, “Preventative Maintenance for Bobtails,” is scheduled for Sunday, April 14, from 3:15 to 4:00 p.m. at the NPGA Southeastern Convention & International Propane Expo in Atlanta. —Steve Relyea