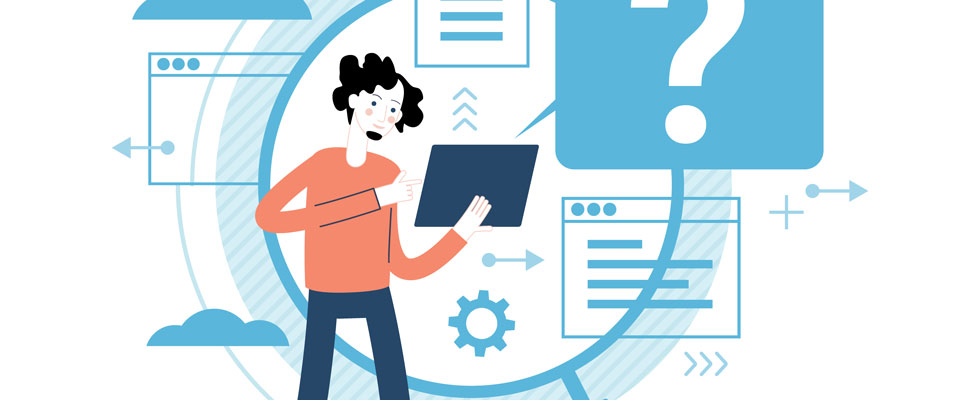
When it comes to establishing a solid safety training program, policies and procedures are the first place to start. Policies and procedures are critical because they help companies meet compliance requirements and reduce liability, but their value in training employees cannot be overlooked.
They are also essential in promoting a culture of safety in the workplace and offering a standard for all employees to follow.
As a blend of virtual and in-person training becomes more common in our industry, it is more important than ever to have a policies and procedures manual that serves as a guiding document for all employee training needs. The propane industry is guided by codes and regulations that can be federal, state or local.
Several industry stakeholders that recommend certain policies and procedures to help propane marketers maintain proper employee training and stay compliant with these codes and regulations include:
- Propane Education & Research Council (PERC) — PERC creates training materials used by propane marketers across the country and has just expanded its offerings to include “The Learning Center,” which provides online training opportunities. Since January, more than 5,000 propane professionals and partners have logged into the tool to complete any of the 400-plus available courses online.
- Certified Employee Training Program (CETP) — With more and more propane professionals taking online courses, it is critical that propane marketers have a clearly defined set of policies and procedures to support online and blended learning materials. As an example, CETP 1.0 states in Module 2: “Know your company policies and procedures for documenting safety-related contacts with the customer. Be sure to document the question or concern that has been raised along with your response.”
- Department of Transportation (DOT) and Occupational Safety and Health Administration (OSHA) regulations — Policies and procedures help companies maintain compliance and ensure employees are properly trained to meet DOT and OSHA roles and requirements.
- Insurance underwriters — Many insurance underwriters affirm that propane marketers should have a policies and procedures manual in place for many tasks, including handling gas-leak and interruption-of-service calls or notifications.
Keeping Policies and Procedures Up to Date
Think about it; you are not training new employees to follow outdated training guidelines. Make sure your policies and procedures manual is as up to date as possible so that it can do its job: keep daily operations running smoothly and reduce risk.
It is critical that a policies and procedures manual is a living document that is updated as your company and code requirements change. It should be reviewed on an annual basis to include these changes.
This will allow your team to discover and remediate shortcomings efficiently and before it is too late. If you have policies and procedures in place in your company, when was the last time you reviewed them? Do you provide training to all current employees regularly and to new employees as a part of the onboarding process? If you already have policies and procedures — or you have just completed one — it is important to recognize that this is not a “one-and-done” deal.
If your company does not yet have a policies and procedures manual, you should have one — plain and simple. It is crucial in order to train employees, uphold a successful safety program, meet regulatory codes and requirements and avoid dangerous scenarios or expensive fines. If you already have your policies and procedures in place, make sure to review your manual at least once a year and to make updates as code requirements change.
Working with a safety professional can make reviewing and updating your policies and procedures manual simpler and more convenient and will ensure that your manual is up to date with industry code changes.