Thursday, September 17, 2020
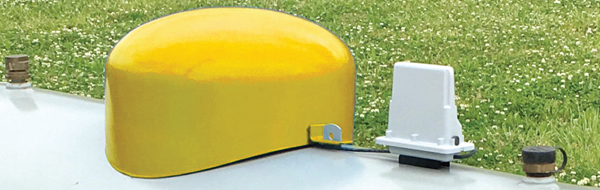
Remote tank monitoring (RTM) is being more widely deployed in many industries. Internet of Things (IoT) analyst firm Berg Insights reports that the global installed base of active RTM solutions is growing at a compound annual growth rate of 36.3%. (This includes not only propane tank monitors, but others as well.)
In the propane industry, tank monitoring is growing because propane marketers need to maximize the efficiency of their deliveries, and because customers expect to have information available to them on demand. Nine providers of tank monitoring solutions recently shared with BPN the ways their products and services help achieve those two objectives.
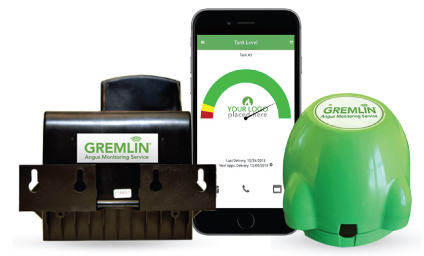
Angus Energy (Fort Lauderdale, Fla.) offers a suite of solutions designed to help companies improve their bottom line performance. For fuel delivery companies, the solutions include Gremlin tank monitors, an app, a portal, ADEPT (Angus Delivery Efficiency Planning Tools), and BRITE business solutions.
“All tank monitor providers have monitors, an app, and a portal, and connect to back-office systems; what makes you better is your training and how you help people properly deploy the monitors,” Philip Baratz, CEO, tells BPN. “Our biggest asset is our experience; we’ve been in this space for a long time. I’m not about monitors, I’m about solutions.”
Before deploying its tank monitoring solutions for a customer, Angus Energy offers a free delivery analysis based on the fuel delivery company’s last two years of delivery history. “We need to build a case that monitors are even needed,” Baratz says. “If they have the K-factors nailed, we’d say they don’t need monitors.”
If the fuel delivery company can benefit from tank monitoring, Angus Energy then prioritizes where the monitors should go and determines whether a cellular or a Wi-Fi monitor would be best for each location. The firm also trains the fuel company’s staff on how to install the monitors and use the portal. “We discuss if there is a need; where there is a need (which groups of customers); and then, and only then, the product.”
Angus Energy offers many other things, too, including business analysis and predictive analytics. With ADEPT, it takes information from a customer’s existing back-office system together with data from tank monitors and K-factors and then helps clients make the biggest drops they can, with no reasonable discomfort in regards to runouts and while spending as little money as possible on delivery. “ADEPT is like a magic box that looks at actual information on current customers and the next 10 days’ weather forecast and determines how to make the most efficient deliveries not only tomorrow, but over the next 52 weeks,” Baratz says.
“Monitors should be part of a comprehensive plan with buy-in,” he adds. “You have to involve your finance team, your delivery team, and your whole operation. You need to know your current delivery metrics and what you are trying to accomplish.”
“We’re partnering with fuel delivery companies,” Baratz concludes. “We look at them not as customers, but as stakeholders. We have a stake in their success and they have a stake in ours.”
For more information, visit www.angusenergy.com.
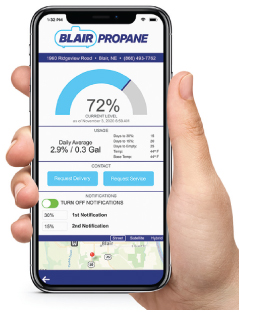
ANOVA (New Providence, N.J.) has launched a Hardware-as-a-Service (HaaS) option for its tank monitoring solutions. Now marketers can use the company’s hardware and software solutions with one affordable monthly subscription and no upfront capital investment.
The HaaS option provides subscribers with a bundle that includes use of Anova tank monitors and sensors; data transmission; and software that is accessible via web browser, mobile, or API. The equipment and batteries are warrantied for as long as the subscriber uses the service, and Anova will upgrade any units affected by network sunsets. The monthly monitoring service also includes deployment guidance and technical support.
“We’re trying to help customers predict and manage technology expenses, and at the same time scale their tank monitoring programs for faster ROI and greater profitability,” Chet Reshamwala, CEO, tells BPN. “Extending access to the latest innovations from Anova, including 4G LTE connectivity and a streamlined, iOS and Android user experience, it’s garnering fast interest due to its competitive and future-proofing benefits.”
“Digitalizing the business is still a key initiative we see progressives in the industry very focused on,” he adds. “Tank monitors are a critical component for business transformation, providing data and actionable insight is always in fashion, pandemic or otherwise. Visiting unmonitored tanks too often or not reaching a tank before running a customer out happens too often.”
Another key part of digitalizing the business is offering consumers a mobile app. Anova meets this need with MyTankApp, which enables marketers to send notifications and marketing offers directly to customers’ smartphones, provide real-time tank level information, and enable customers to request delivery and service. This supplies an opportunity to build customer loyalty, provide better service, and market more effectively and efficiently.
“Communication is key, and when you can send a message to your customers that is timely and relevant to them, such as storm warnings with preparation tips, you build on the relationship and become a true partner for them,” Reshamwala says. “Anova’s MyTankApp mobile app helps marketers provide a unique experience for customers of propane distributors.”
For more information, visit www.anova.com.
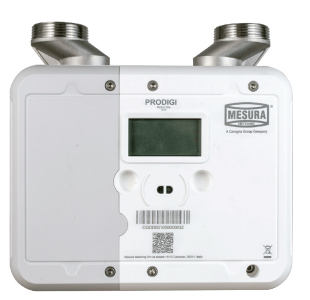
Cavagna Group offers a solution that provides the benefits of tank monitoring, but also gives the propane marketer a number of other abilities. The company’s Ultrasonic Smart Meter allows them to bill for propane as it is consumed, lets them shut off the meter remotely, and enables them to use the tanks they own at customer locations as additional storage.
“This is not a traditional meter; this is a tank monitor on steroids,” Peter Dwyer, vice president of sales and business development, LPG Division, Cavagna North America (Somerset, N.J.), tells BPN.
Metered service: The Ultrasonic Smart Meter is weights and measures approved, so marketers can bill through the meter. Rather than charging for a single, large delivery, they can bill the customer for the propane as it is used. “That’s how people are accustomed to paying for energy—they pay after they have physically consumed it,” Dwyer notes. “The expensive large delivery has been a stigma of propane. It makes customer retention difficult because when customers know they will soon be needing a large delivery, they shop around.”
Remote shutoff: The Ultrasonic Smart Meter has a solenoid valve that can be shut off remotely. “If there is an unsafe condition or a lack of payment at the location, a technician does not have to physically go to the property to shut it off,” Dwyer adds.
Additional storage: Because customers with metered service are not charged when the propane is delivered, marketers can deliver it at any time to the tanks they own. That means drivers can top off the tanks during the offseason, rather than waiting for customers to call when the weather turns cold. “If the marketer has 60 accounts with 500-gallon tanks, that’s 30,000 gallons of bulk storage, but it’s at the customer’s location, so they have it when heating season begins,” Dwyer explains.
Additional benefits of the Ultrasonic Smart Meter include accuracy and longevity, he adds. Rather than using a float gauge, the meter measures how much propane leaves the tank and goes into the house. And, rather than using a mechanical meter with moving parts that can break down, the meter uses an ultrasonic sensor that has no mechanical components. The meter has only one mechanical part: the solenoid valve that does the shutoff. The Ultrasonic Smart Meter can use celluar or LoRaWAN communication and it can report to Cavagna’s own platform or the customer’s back-office software.
For more information about Cavagna’s Ultrasonic Smart Meter, visit www.cavagnagroup.com.
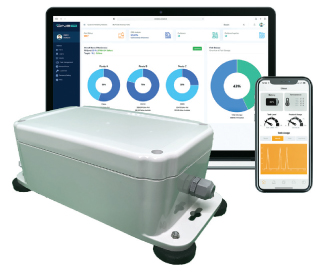
InSite Platform Partners (St. Charles, Mo.) has been offering SkyTracker tank monitors for years, providing a satellite-based solution for areas where it is difficult to get cellular coverage. Now, the company is rolling out three more solutions for the propane industry.
The first is a new dashboard that works with SkyTracker tank monitors and makes it easier for propane marketers to monitor all their tank data. Any tank can be connected to the One-Tank dashboard, and the dashboard is accessible on any device. Together, the data from the dashboard and the metered billing of the SkyTracker monitors enable marketers to use the tanks they own at customers’ locations as field storage. “Marketers can fill their tanks when it is convenient for them; they are not bound by the will-call customer,” Brian Humphrey, CEO, tells BPN. “This allows them to switch their business model from reactive to proactive. They can buy and deliver fuel in the off-season when the prices are low and the roads are in better condition.” One-Tank also alerts the marketer to abnormal usage, so they can investigate and see if that’s because of local degree days or if there is a leak. One-Tank is to be released later this year. InSite is now offering generous discounts and benefits for those who enroll in its Early Adopter Program.
The second new solution is a cellular-based variant of the SkyTracker tank monitor for use at locations that can get cellular coverage. “Our new cellular-based version of SkyTracker has a lower cost, so marketers don’t have to pay for satellite if they don’t need it,” Humphrey explains. These new monitors are equipped with batteries that last at least seven years and are field replaceable. Both variants of SkyTracker tank monitors read off the dial, but also feature temperature compensation. This makes them accurate enough to allow metered billing.
The third new offering from InSite is a mobile app for consumers. This allows end users to view their own tank and usage and to communicate easily with their provider. The app is now available for iOS and Android devices.
For more information about One-Tank, visit www.one-tank.com.
For more information about SkyTracker, visit www.nascorp-skytracker.com.
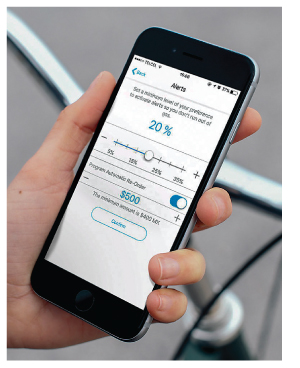
Nube (Boulder, Colo., and Mexico City) offers a tank monitoring solution that features a sensor that requires no wires. This saves the tank manufacturer and the propane marketer the cost of about $14 for the remote-ready gauge and a $40 remote-ready cable, and makes for an easy installation that takes only two minutes.
This is part of a solution that includes not only the sensor, but also an administrative portal and a mobile app. Together, these offerings from Nube provide complete visibility and transparency to both propane marketers and their consumers.
“This provides an end-to-end IoT solution,” Christopher Gnanakone, CEO of Nube, tells BPN. “It provides analytics and insights to the demand side (consumer) and the supply side (propane gas company) via two SaaS applications (gas company portal and white-labeled mobile app for the consumer) that enable parties to monitor, optimize operations, order processing, and logistics, and enable efficient supply chain management.”
The Hall effect sensor sends a reading of gas levels once a day via global wireless data transmission. Because it uses LPWA CAT M1 NB-IOT cellular connectivity, Gnanakone says, “the battery lasts for the life of the tank—12 to 14 years.” The device can be programmed before or after installation to report tank levels at intervals ranging from twice a day to once in five days and any time frame in between. It can be programmed over the air, just as the software on your iPhone gets software updates via the cellular network remotely.
The administrative portal provides the gas company with global monitoring of customers’ tanks; details of each customer/tank; history of consumption and order processing; online payments; and business intelligence tools. It includes alert level notifications as well as predictive analytics that tell the day the alert will strike. When an alert level is reached, messaging can be customized to email, text, or other messaging applications. In addition, Application Program Interfaces (APIs) are available to back-office ERP systems and third-party software applications.
The mobile app enables the consumer to monitor gas levels, set alerts, view consumption history, preset automated orders, and make payments. It is free to consumers and is available for Android and iPhone. The app also can be customized for bobtail truck drivers, allowing them to monitor the tanks they deliver propane to. “This enables advanced scheduling and delivery planning and enhances customer service, because the driver can call when the gas is going to be delivered,” Gnanakone concludes.
For more information, visit www.nube.gs.
Otodata Tank Monitors (Montreal) is launching four new products in 2020. Three result from collaborations with other leading manufacturers in the industry.
One is a digital lead for connecting into gauges. Developed in collaboration with Rochester Gauges, this provides very precise digital metering. “More and more marketers want to charge based on consumption,” André Boulay, president of Otodata, tells BPN. “Analog technology has a margin of error of 5%, 6%, or 7%, which is too much when you are trying to bill someone. This digital lead gives a much more accurate reading.” The new lead is universal, so it slips easily into any dial, and it doesn’t protrude from the gauge.
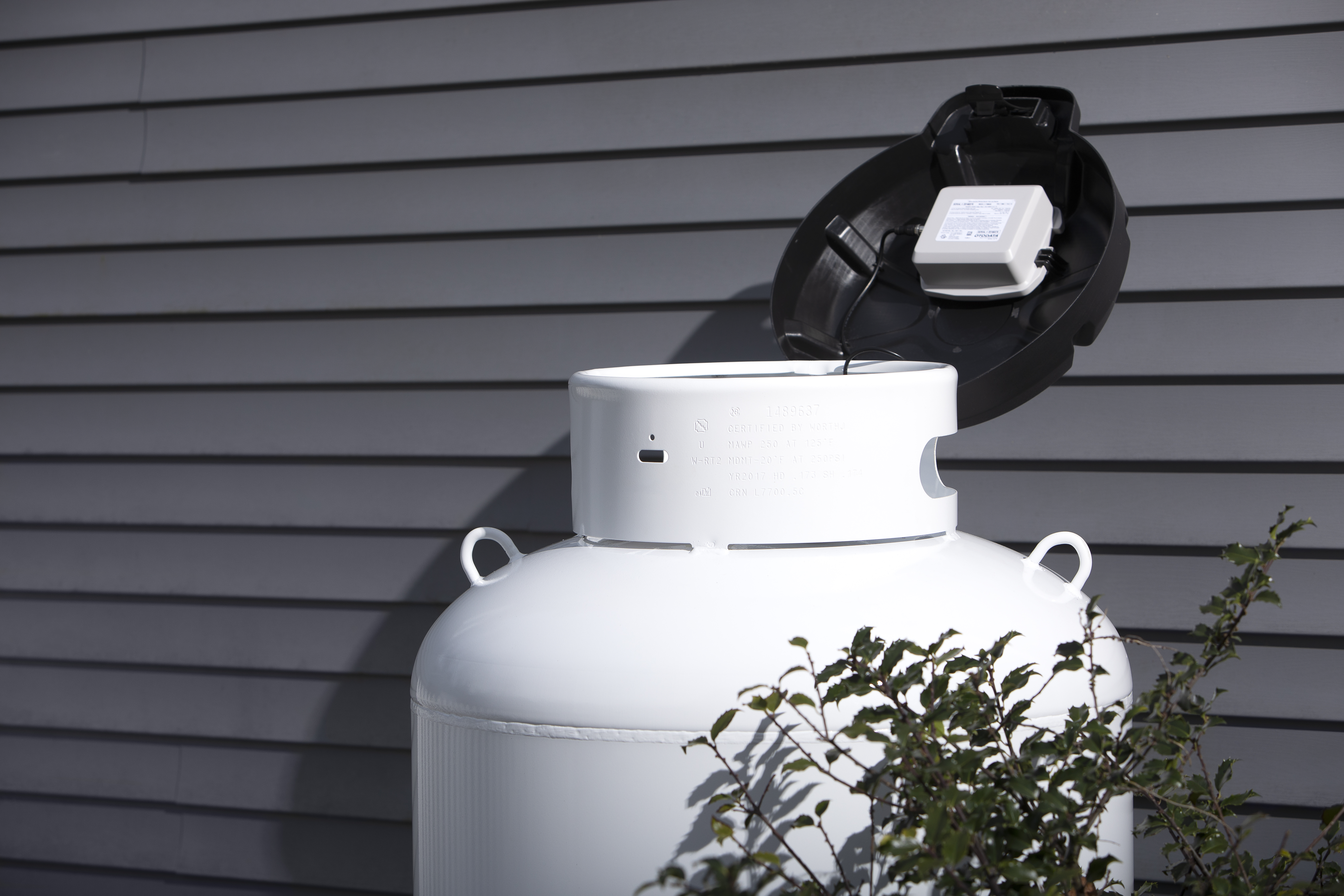
The second new product is the SmartLid. Created in partnership with Worthington Industries, and designed with the fuel technician in mind, this integrated lid features Otodata’s monitor technology combined with Worthington’s improved lid design. It allows for a quick and easy installation and protects components from damage. Each SmartLid also features an optimized signal. “With SmartLid, the antenna is always in the ideal place on top of the tank,” Boulay notes.
With the third new product developed in collaboration, Otodata tank monitors will interact with BASE Engineering ProControl3 truck control system. “The systems can talk to each other,” Boulay explains. “As the tank is filled, we monitor the gauge very closely and can automatically shut down and stop the truck pump. If the driver is not paying attention as he should, this would override his manual command and stop the fill at a certain percentage.”
The fourth new product to be launched in 2020 is an updated version of Otodata’s tank monitors. These will use the new cellular communication protocols Cat-M and NB-IoT. “We have also updated a few other things to optimize the technology. But it’s not more expensive–it’s more affordable.”
“Otodata’s vision has always been to provide affordable, effective tank monitors,” Boulay concludes. “We have made the ROI work on most tanks; now we want to make it work on any tank so marketers can bring digital service to their customers. We can’t let the utility companies be the only ones to have every home connected and have services around that. We need to make it so our clients have access to these services too—to know their levels, get alerts, and click to order fuel. So, we bring them affordable hardware, reasonable recurring charges, and these services.”
For more information, visit www.otodatatankmonitors.com.
Schneider Electric offers a complete set of tools to improve the productivity of any propane distribution business. These include 4G LTE/HSPA residential tank monitors, commercial propane monitors, and the WebView data portal.
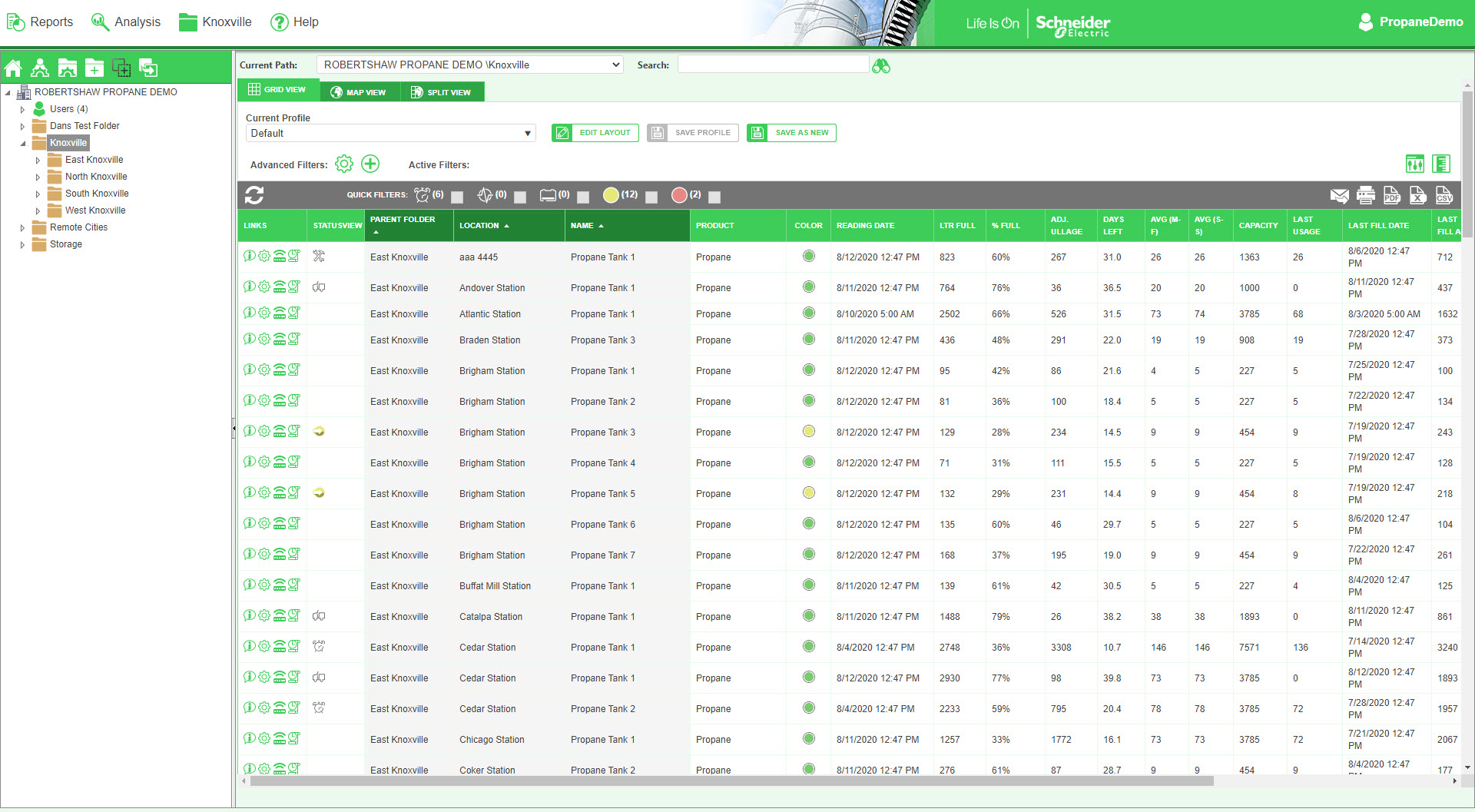
“Monitoring is more valuable than ever now,” Fred Morgenthaler, manager Centeron sales, tells BPN. “We reached out to customers and they told us the monitoring has saved their bacon during the pandemic by preventing runouts. Staff could access the information online, from home, and that saved them time and trouble. Having the information in a localized place, so they can have access to it from home, is perfect for the virtual world we live in now.”
Like other tank monitors, Schneider Electric’s hardware communicates over cellular band and sends information to a centralized database. Alerts can be set to notify the marketer of low tank levels and excessive usage.
“The data center is where we really shine,” Morgenthaler says. “It is very user-friendly.” The software allows complete customization, enabling users to control how the information is presented. Tanks can be organized in folders, so different users can see only what they need to see. This makes it easier for users to find the tanks they need to take action on. Management reporting tools are included, so CEOs and chief operating officers can look at the data efficiently. Screen layouts are customizable, too. So, for example, a screen can be set up to show only tanks that are 30% full or five days from empty. “The data is managed so that it is useful,” Morgenthaler notes. “This allows viewers to look through the tanks efficiently.”
The tools are compatible with many back-office software providers. “We go back 15 or 20 years in remote monitoring, so we understand what marketers need.”
“Some marketers spend too much time looking at hardware. That’s just a tool,” Morgenthaler concludes. “What you need is data. That’s what you pay for and make decisions on.”
For more information about the tools and data provided by Schneider Electric, visit www.wirelessmonitoring.centeron.net/index.aspx.
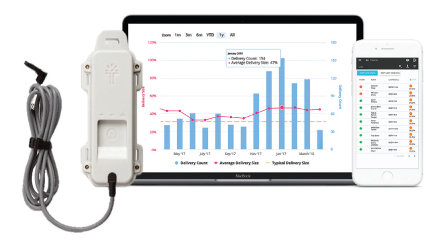
Tank Utility (Boston) offers a tank monitoring solution that includes internet-connected tank level monitors; cloud-based software and analytics, and a white-labeled mobile app. Beyond that, the company also provides services that help marketers make the most of this solution and improve their operations.
“Tank Utility is a full-service solution,” Christine Adams, content marketing manager, tells BPN. “It’s easy for marketers to get hung up on hardware, but it takes more than a tank monitor to transform a business. Marketers should be able to lean on their tech partners to implement their solution.”
She highlighted several ways Tank Utility’s software and services complement its hardware: The company not only delivers tank level data, but also detects how much a marketer is earning per monitor and how those savings trend over time. Before the purchase, Tank Utility offers to analyze the marketer’s delivery data to see where they can save and how they can grow profitably through monitoring. To help with deployment, the company offers to send out field techs to install monitors on tanks for the marketer. After the purchase, it assigns each marketer a customer success manager who helps them make the most of all that Tank Utility has to offer through training, best practices, and recommendations for operational changes.
Tank Utility integrates with back-office software, at no charge. “We pride ourselves on our flexibility in integrating with the back-office systems that our customers rely on for running their businesses,” says Dan O’Connell, senior director of product. “We go out of our way to meet the customer’s needs and meet them where their business processes run.”
“Our back-office integration is bidirectional,” Adams adds, “which means our customers can ensure the data from their back-office is pulled into Tank Utility accurately. We make sure the data is automatically updated in both systems to save marketers from having to perform manual data entry.”
When it comes to hardware, Tank Utility offers Dual-Carrier 4GLTE cellular, WiFi, and satellite monitors to connect to any tank. The monitors feature inexpensive, field-replaceable batteries and are backed by a lifetime warranty. “In addition to providing the best tools to ensure you are getting the most ROI out of monitors and integrating into your back-office if you have one, our software platform helps you stay on top of hardware maintenance as your fleet grows by alerting you whenever a monitor needs attention,” O’Connell explains.
Adams concludes, “We provide these features and services to help marketers improve their operations and profitability, specifically by making smarter drops and expanding their team’s capacity. Tank Utility gives its customers time back in their days; that is the main benefit of our solution.”
For more information, visit www.tankutility.com.
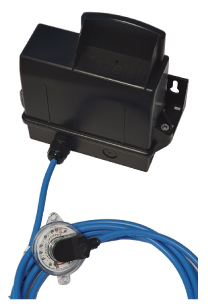
Tekelek (Shannon, Ireland, and The Woodlands, Texas) offers a tank monitoring solution that features a range of connectivity options and easy integration with the customer’s preferred backend or cloud solution.
The company is celebrating its 25th year in business. Tekelek started in 1995 as a one-person operation, founded by Peter McCarthy, and now employs 200 people across four Tekelek sites worldwide. It provides propane and liquid tank level measurement solutions, serving a diverse range of customers across the LPG, oil, chemicals, water and wastewater, waste management, and agri-food industries.
“With 3.5 million Tekelek tank monitors deployed worldwide, we offer propane marketers a cost-effective, proven, ultra-reliable, robust, intrinsically safe and accurate monitoring solution across a range of communications protocols and incorporating GPS tracking,” Sean Ganley, chief sales officer, tells BPN.
For propane customers, Tekelek offers a range of monitors in 4G LTE Cat M-1 and NB-IoT, 3G cellular, LoRaWAN, and Local Radio connectivity options. The sensors are easy to install and maintenance free. Non-contact dial gauge measurement is available via a Rochester gauge.
The data can be accessed anytime and anywhere. Tekelek is a platform-agnostic solution, so customers can use Tekelek’s backend and apps or they can choose to integrate Tekelek into their own preferred backend or cloud solution. “We’re not locking customers into costly ‘stovepipe’ backend solutions,” Ganley notes.
“Tekelek offers our customers scalable and flexible asset monitoring solutions to meet their business needs via Tekelek’s industry-leading two-way, remotely configurable sensors—used by everyone from small marketers to Fortune 500 businesses,” he adds.
“Now, more than ever, remote monitoring of your inventories and tracking of your assets is essential to the optimal running of your business during these challenging times,” Ganley concludes.
For more information, visit www.tekelek.com. — Steve Relyea
TOP PHOTO COURTESY: ANOVA