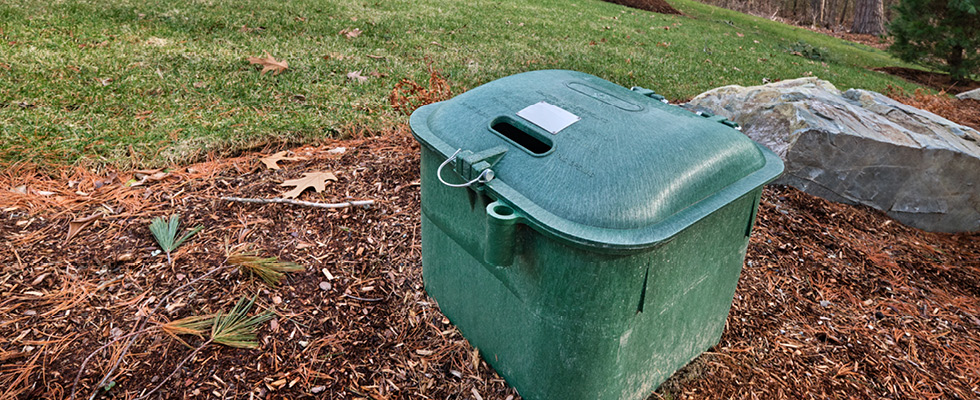
The National Fire Protection Agency’s (NFPA) Liquefied Petroleum Gas Code 58 requires routine cathodic testing requirements for underground propane tanks after July 2010. How is your company’s cathodic protection process? Are you aware of how to meet specific code requirements efficiently? Requirements vary depending on location, but what doesn’t change is the best way to document your testing data.
At this point, many underground tanks will be approaching their required follow-up testing period. Make sure you and your team are prepared with this self-assessment to analyze and improve your cathodic protection testing program.
Your Self-Assessment Guide to Cathodic Protection Testing
Q: Do you have an initial testing record and inspection form for that tank?
Initial inspection is required when you install a new underground tank or service an underground tank after July 2010.
Q: Do you have completed follow-up testing?
This is required by NFPA 58 on a timely basis after the initial inspection.
Q: Do you use technology or any system to track these follow-ups?
Implementing a system that tracks inspections and provides compliance alerts when follow-ups are due is critical to maintain compliance.
Q: Are your cathodic tests documented and accessible?
If you needed to reference a tank’s cathodic test history, could you do so easily? Using technology to store, track and retrieve these tests can maximize internal efficiencies.
Q: Are your employees trained in proper cathodic testing methods?
Make sure your employees have received hands-on training to conduct cathodic tests appropriately. Testing requirements, per NFPA 58, include:
- Cathodic protection must be at least -.85 D.C. or more (meaning negative) using a copper-copper sulfate half cell.
- Test must be completed upon installation unless prohibited by climatic conditions, in which case, testing shall be done within 180 days after installation of the system.
- For continued verification of the effectiveness of the system, retest 12 to 18 months after the initial test.
- Systems failing a test shall be repaired as soon as practical unless climatic conditions prohibit this action, in which case the repair shall be made no more than 180 days thereafter. Testing schedule shall be restarted as required initially.
- Periodic follow-up testing shall be performed at intervals not to exceed 36 months.
- Documentation of the results of the two most recent tests shall be retained.
Developing a streamlined process for your company’s cathodic testing documentation is critical to meet your NFPA 58 requirements while protecting your customers and your company. So what’s the best way to go about this? Here are some suggestions on complying with NFPA 58 cathodic protection inspection requirements.
Improve Documentation Accuracy & Organization
Do you have initial testing and inspection forms for any employees who need them? Does your company have a process in place to ensure that periodic intervals are being taken care of? There are a variety of different platforms out there; some people use paper forms, while others use a digital platform to store their documents safely and get reminders of periodic inspections.
Regardless of how you plan to document periodic inspections, choose a method that works well for your company, your employees and your customers, along with meeting industry standards for documentation. Your plan should also clearly define how your company performs such inspections.
Know What’s Required by NFPA 58
Make sure your team is comfortable with the NFPA 58 cathodic protection inspection requirements listed earlier in this article. As inspections come in, use a digital compliance program to give your management teams an easy-to-evaluate technician performance. You’ll be able to view technician-specific data, identify any areas for improvement and provide customized coaching in real-time to educate your team while reducing risk.
Find a Bulletproof Way to Track Follow-Up Tests
Develop a plan to conduct required follow-up testing. And keep in mind — paper inspection forms stuffed in a filing cabinet have no way of letting you know when they’ve expired. Instead, digital documentation automatically flags inspections needing follow-up on your dashboard for management staff to see.
Using software to store, retrieve and track cathodic protection documentation makes this process extremely efficient for your safety management team. Plus, software can notify you immediately when corrective action is necessary, unlike paper forms which often sit unattended for months.
How to Get Started on Your Compliance Assessment
If you’re overwhelmed by all the information or know there are improvements to be made at your company, reach out to a third-party safety consultant and recruit their help getting a custom analysis and a digital compliance program. The help of external professionals and technology can simplify this process, optimizing efficiency to keep your customers, employees and company safe.