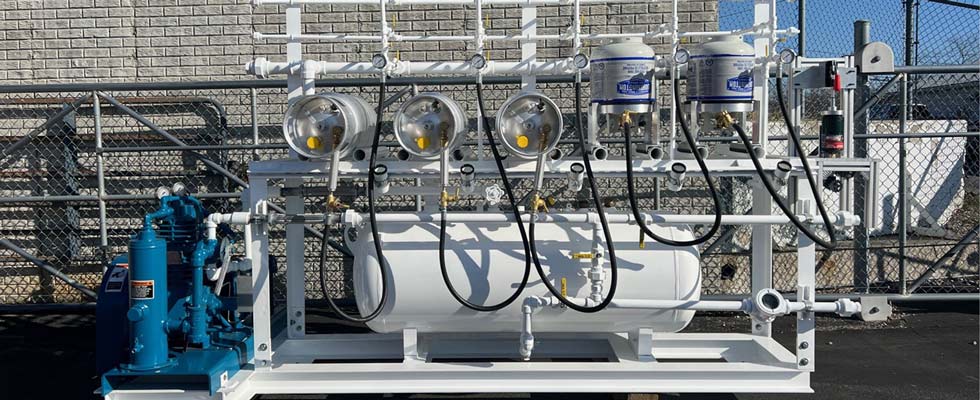
Propane cylinder evacuating is nothing new to the propane industry. Many large cylinder exchange companies have some sort of evacuation system to remove the liquid and vapor propane from cylinders to make repairs. The most commonly evacuated cylinders are 20-pound and 33-pound forklift tanks. However, there is equipment available to evacuate any sized propane vessel, from small cylinders to large storage tanks.
An Inside Look at a TurnKey Cylinder
About 10 years ago, Industrial Propane Service Inc. (IPS) developed a turnkey cylinder evacuation system that is fully assembled and painted for evacuating typically four to 12 cylinders at a time.
How does it work? It uses a steel rack for mounting all components for a compact, user-friendly experience. The main components are a propane vapor compressor, a scavenger tank and the cylinder evacuation stations. The size of the scavenger tank as well as the number of stations depends on the number of cylinders the customer needs to be able to evacuate at the same time.
The scavenger tank is typically kept at around 5 psi by using the compressor to transfer vapor from the scavenger tank into a bulk storage tank. Cylinders are placed at the stations in a position accessible to the liquid opening of the cylinder. The cylinder valves are opened and the liquid and vapor are emptied into the scavenger tank. Most of the liquid boils to vapor as it reaches the scavenger tank, which is transferred to the storage tank. The system can be reversed to transfer excess liquid from the scavenger tank to the storage tank. The system has a nitrogen purge line to clear the cylinder to a nonexplosive state and a vent line to be sure the cylinder is empty. The average time to fully evacuate propane from multiple cylinders at a time is about seven minutes. (Testing was done using new, full 20-pound and 33-pound cylinders.)
While testing used cylinders, some cylinders took longer due to the condition of the valve in the tank. When venting or flaring propane in cylinders that are due to be repaired, the process can be very slow and there are many safety concerns to be addressed when doing it that way. Not to mention there is more waste of reusable propane.
Steel scrap yards and recyclers are often in need of solutions to evacuate propane cylinders that still have propane in them. When the tanks are crushed, there can be an explosion, which is extremely dangerous and can damage the crusher. Most of these kinds of companies have many cylinders that have propane in them just sitting in a pile, while many have stopped accepting the cylinders unless they are punctured or cut in half. The propane industry has been dealing with the same issues. As regulations dealing with venting or flaring are becoming more stringent, a solution is needed.
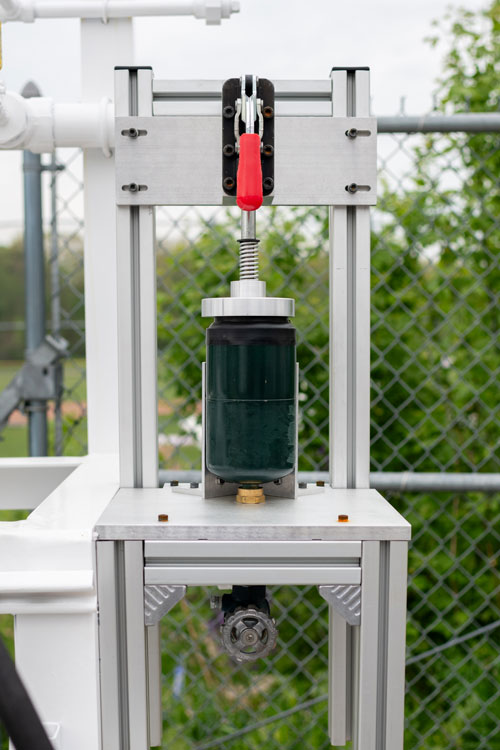
Recently, there has been an influx of questions regarding evacuating 1-pound cylinders that are used for grilling, camping and small engine fuel. The quantity of 1-pound cylinders left behind in campgrounds, national parks, campuses and other tailgating events nationwide is massive. One-pound cylinders are considered household waste and the cylinder should be properly disposed of. The big question is, how do you properly dispose of them?
One way that we have responded to this need is by developing a 1-pound cylinder inverter to connect to our cylinder evacuation systems. The idea is to evacuate multiple 1-pound cylinders at a time. Typically, the systems at this point range from five to 10 cylinders at a time. In testing new, full 1-pound cylinders, it took about 30 seconds to completely remove propane. The process is simple: Invert the 1-pound cylinder, set it in place and lock the lever down.
Many places that are left with 1-pound cylinders may not have an existing propane storage tank or propane dispensing system. For such places, it is helpful to provide options for a skid-mounted propane tank and dispensing system that can connect to evacuation systems. At IPS, these systems typically include a 1,000-gallon to 3,900-gallon tank for storing the recovered propane. If the customer does not have a use for the propane they recover, we can often provide them contacts of local propane retailers to sell the propane to, which helps with the return on investment.
When you take into consideration outdoor events, scrap yards and the propane industry collectively, there is an incredible amount of propane being stored that could be recovered and used or resold. It’s beneficial to offer evacuation systems that can, for example, be conveniently installed on a trailer. This opens the possibility to travel to a site to evacuate not only propane cylinders, but also domestic tanks sitting in our industry’s bulk storage plants. There are thousands of these tanks sitting at bulk storage yards around the country and most of them are likely to have at least 5% of liquid propane in them. Once empty, the tanks can be refurbished or scrapped.
These evacuation systems are expensive. However, the safety factors, efficiency, air quality and opportunity to recover and use what would typically get flared or vented make for an attractive return on investment. These systems are designed for future growth. After the initial investment, adding more cylinder evacuation stations is reasonably inexpensive. The propane vapor compressors are the most expensive part of the equipment included with the evacuation system. The compressor is sized for the potential growth that the customer may need in the future.
The propane industry has the opportunity to play a crucial role in today’s needs for alternative energy sources. Propane is a safe, renewable, clean-burning and affordable option for a cleaner environment. Propane autogas, portable electric charging systems and propane evacuation systems are just a few of the many ways propane can help the environment, including cleaning up waste in public outdoor spaces.