Saturday, December 28, 2013
Michael Avery, CEO of California Clean Air Technologies (CCAT; Menifee, Calif.), noted some important reasons why the company chose stationary farm equipment as the first products to use its Dual Fuel Retrofit System (DFRS), which works with existing diesel engines in combination with propane.
“Stationary equipment is less vulnerable because it doesn’t move around and doesn’t bounce,” said Avery. “The No. 1 reason we chose this equipment is due to the fact that it burns a tremendous amount of diesel.”
With funding help from the Propane Education & Research Council (PERC), the company built a retrofit system that is believed to be the only off-road dual-fuel engine with California Air Resources Board (CARB) certification.
CCAT has started installing the DFRS on stationary equipment such as irrigation pump engines and generator sets. The dual-fuel system, with two separate fuel tanks, can run in diesel-only mode or in propane-diesel mode. CCAT, which lists its core business as “developing and marketing new technology to increase the efficiency of heavy-duty diesel engines,” also plans to eventually install the dual-fuel system on mobile equipment such as tractors. The company in July displayed the dual-fuel retrofit system in use by one of its first launch customers, Maddox Dairy of Riverdale, Calif. in the San Joaquin Valley. Bolthouse Farms, also in San Joaquin Valley, is another company using the stationary equipment with DFRS.
Maddox Dairy installed two propane-diesel retrofit systems on its groundwater irrigation pump engines a year ago, and it reports seeing a 25% savings in fuel costs, a 50% reduction in diesel consumption, and reduced exhaust emissions. The technology could be a welcome relief for farmers, who are motivated to bring down their fuel costs because of the current high price of diesel. During May and June, which are high-use months for the equipment, Maddox Dairy saved $3400 to $4000 per month on fuel.
The product development process started around 2010, when PERC began working with CCAT to research the technology. PERC provided the initial funding, then CCAT tested and monitored the engines for real-world applications.
Avery and CCAT vice president George Malouf spent about a year testing dual-fuel propane systems from around the world, with a goal to produce a product that would displace 50% of the diesel with propane. Early propane fumigation systems displaced about 12% and advanced to displace about 25%. CCAT’s displacement results have been coupled with pollution reduction, particularly NOx emissions, Avery noted.
DFRS can be used on various engine sizes and can run on propane/diesel or natural gas/diesel. But CCAT has begun with a focus on stationary engines of 10 to 15 liters, which are large engines that Avery says “work hard, long hours in the agriculture sector.” That sector uses many water pumps with engines of that size. The systems are hooked up to pumps that pump water out of deep wells into irrigation systems.
After completing the testing, CCAT found several agricultural launch customers who were willing to test the technology, and Maddox Dairy was one of the first. Avery noted that CCAT chose an operation for testing in the San Joaquin Air Pollution Control District in California because of the heavy use of stationary equipment that exists in the county, which has some of the strictest air regulations in the United States.
Getting CARB certification was a big hurdle. Avery noted the total cost was $811,000 for lab work over about three years. For that lab work, the company used Caterpillar 3406 and Cummins QSM 11 engines, which are popular in on- and off-road and industrial applications.
In addition to cost savings, emission reduction is a big factor for farms using stationary irrigation equipment, especially in California and particularly in the San Joaquin Valley, an area that Avery says has a high level of air pollution. Maddox Dairy reduced its NOx emissions by 50% by using the product, and that allowed the farm to address another big issue: hours of equipment operation. Companies are allocated a certain number of hours to use the equipment, and because of the NOx reduction, CARB allowed an increase in hours of operation for the dairy.
PERC has worked with CCAT to demonstrate and validate the technology and to get the word out to likely users.
The council has deemed farms as the first area of focus for the product since the system could work on any large-displacement diesel engine, mobile or stationary. Future targets could include mobile and stationary equipment such as heavy-duty tractors and heavy-duty trucks.
The system’s status as possibly the first-ever CARB-certified dual-fuel engine is an important opportunity to quickly add gallons for the propane industry, because retrofitting an existing piece of technology is far less cumbersome than designing and engineering systems for various-sized engines. —Daryl Lubinsky
“Stationary equipment is less vulnerable because it doesn’t move around and doesn’t bounce,” said Avery. “The No. 1 reason we chose this equipment is due to the fact that it burns a tremendous amount of diesel.”
With funding help from the Propane Education & Research Council (PERC), the company built a retrofit system that is believed to be the only off-road dual-fuel engine with California Air Resources Board (CARB) certification.
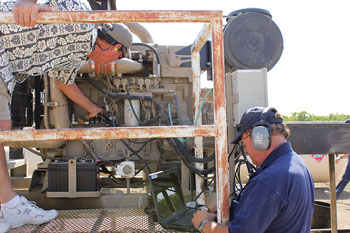
Maddox Dairy installed two propane-diesel retrofit systems on its groundwater irrigation pump engines a year ago, and it reports seeing a 25% savings in fuel costs, a 50% reduction in diesel consumption, and reduced exhaust emissions. The technology could be a welcome relief for farmers, who are motivated to bring down their fuel costs because of the current high price of diesel. During May and June, which are high-use months for the equipment, Maddox Dairy saved $3400 to $4000 per month on fuel.
The product development process started around 2010, when PERC began working with CCAT to research the technology. PERC provided the initial funding, then CCAT tested and monitored the engines for real-world applications.
Avery and CCAT vice president George Malouf spent about a year testing dual-fuel propane systems from around the world, with a goal to produce a product that would displace 50% of the diesel with propane. Early propane fumigation systems displaced about 12% and advanced to displace about 25%. CCAT’s displacement results have been coupled with pollution reduction, particularly NOx emissions, Avery noted.
DFRS can be used on various engine sizes and can run on propane/diesel or natural gas/diesel. But CCAT has begun with a focus on stationary engines of 10 to 15 liters, which are large engines that Avery says “work hard, long hours in the agriculture sector.” That sector uses many water pumps with engines of that size. The systems are hooked up to pumps that pump water out of deep wells into irrigation systems.
After completing the testing, CCAT found several agricultural launch customers who were willing to test the technology, and Maddox Dairy was one of the first. Avery noted that CCAT chose an operation for testing in the San Joaquin Air Pollution Control District in California because of the heavy use of stationary equipment that exists in the county, which has some of the strictest air regulations in the United States.
Getting CARB certification was a big hurdle. Avery noted the total cost was $811,000 for lab work over about three years. For that lab work, the company used Caterpillar 3406 and Cummins QSM 11 engines, which are popular in on- and off-road and industrial applications.
In addition to cost savings, emission reduction is a big factor for farms using stationary irrigation equipment, especially in California and particularly in the San Joaquin Valley, an area that Avery says has a high level of air pollution. Maddox Dairy reduced its NOx emissions by 50% by using the product, and that allowed the farm to address another big issue: hours of equipment operation. Companies are allocated a certain number of hours to use the equipment, and because of the NOx reduction, CARB allowed an increase in hours of operation for the dairy.
PERC has worked with CCAT to demonstrate and validate the technology and to get the word out to likely users.
The council has deemed farms as the first area of focus for the product since the system could work on any large-displacement diesel engine, mobile or stationary. Future targets could include mobile and stationary equipment such as heavy-duty tractors and heavy-duty trucks.
The system’s status as possibly the first-ever CARB-certified dual-fuel engine is an important opportunity to quickly add gallons for the propane industry, because retrofitting an existing piece of technology is far less cumbersome than designing and engineering systems for various-sized engines. —Daryl Lubinsky