Tuesday, February 11, 2020
(February 11, 2020) — There’s an emergency and your facility has been evacuated. Employees have gathered outside, but someone is missing. Is that person still in the building, or was the person absent today?
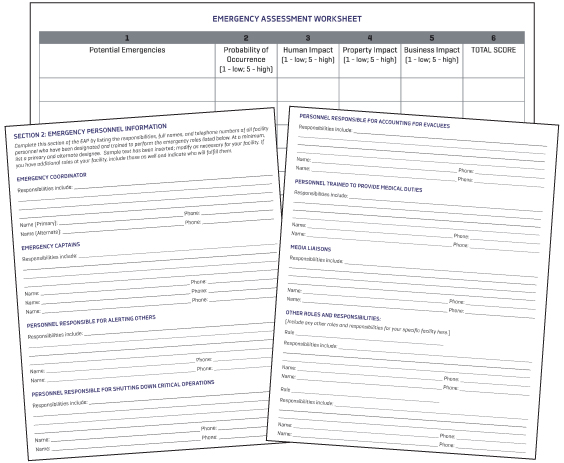
That scenario is an example of why “accounting of employees” is one of the many required elements of an emergency action plan. At a recent meeting of the Western Propane Gas Association (WPGA), the association’s safety consultant, Rob Scott, explained that propane marketers should know each day who has shown up to work and who hasn’t.
An emergency action plan isn’t something that’s created once; it’s something that must be reviewed on a regular basis. “There’s always an accident waiting to happen,” Scott said. “The question is: Are we ready for it?”
That, he noted, is what an emergency action plan is for. In his presentation, he focused on two questions: What’s in your plan? Has it been reviewed?
An emergency action plan is a written document that facilitates and organizes employer and employee actions during workplace emergencies. Its benefits are fewer and less severe injuries; less structural damage; and reduced confusion.
The required elements of an emergency action plan include a means of reporting; evacuation procedures and emergency escape routes; procedures for critical operations; accounting of employees; rescue and medical duties; and contact persons.
Scott listed different sorts of emergencies. They include natural incidents, such as floods or tornadoes; technological incidents, such as chemical release and vehicle accidents; and man-made incidents, such as civil disturbances or workplace violence.
He told of a recent incident in which customers were unhappy that they would not be paid for the propane left in a cylinder. One of them brought out a knife. Scott asked, “Would your driver know what to do?”
OTHER PROCEDURES
In addition to an emergency action plan, other emergency planning procedures include exit routes; fire prevention plans; hazardous waste operations and emergency response; permit-required confined spaces; fire brigades; portable fire extinguishers; fixed extinguishing systems; fire detection systems; and employee alarm systems.
Scott suggested developing habits to adhere to these requirements. For example, if your fire extinguishers are inspected annually, do fire extinguisher training at the same time. You can test employees while the inspector is onsite.
He then walked the audience through an emergency assessment process, using a worksheet that is available from the Propane Education & Research Council (PERC).
On the worksheet, you write down potential emergencies that could affect your plant. For each, you then estimate the probability of each emergency’s occurrence and assess the potential human impact, property impact, and business impact. Each is assigned a number, representing high or low probability or impact.
“We want to see near zero if we can,” Scott said. Those that do have higher totals, though, are those that should be given the highest priority and resources. But, he added, all emergencies should be planned for, and none should be ignored.
He then outlined a resource assessment. This includes assessing the personnel; the facility; and equipment and supplies. Among the questions to ask here are: Do we have first aid kits in trucks? Have we hired someone new? If so, have personnel records been updated? Is all necessary personal protective equipment available at the facility? Scott told of a driver who recently showed him his new leather gloves. The gloves were not the required gas gloves.
COMMUNICATION
Communication is another element of an emergency action plan. Requirements here include a designee for alerting and assisting employees and others during an emergency; alarms that are distinctive and recognized by all employees; and post-emergency phone numbers. The plan should also include the details needed for notifying emergency responders, utility companies, the National Response Center (NRC), the Department of Transportation (DOT), and the Occupational Safety and Health Administration (OSHA).
Scott suggesting taking into account the response time of not only the fire station closest to your plant, but also the second closest. He explained that the one that’s closest might be out on a call when you need them.
Evacuation is another element of the emergency action plan. The plan should identify an emergency coordinator; evacuation captains; individuals responsible for shutting down critical operations; individuals responsible for accounting for evacuees; evacuation routes and exits; and evacuation maps and drawings.
“In an emergency, everyone’s natural reaction is to run,” Scott noted. “But someone needs to push the shutoff button.”
Propane marketers also should collaborate with others before an emergency. Others who can help include employees; company officials and management; local emergency responders; local and state government; local emergency planning committees; and community and civic groups.
“It’s all about building networks and alliances,” Scott said. He suggested attending meetings of the local fire chiefs’ association. “They will appreciate your participation.”
Keeping employees current on the emergency action plan requires distributing the plan, maintaining the plan, and training on the plan. Training should include both classroom activities and practice drills. “We can never do enough training,” Scott noted.
When all these elements of an emergency action plan are known and reviewed, everyone will be as ready as they can be when something unexpected happens—for instance, something that might lead to employees evacuating and gathering outside. — Steve Relyea
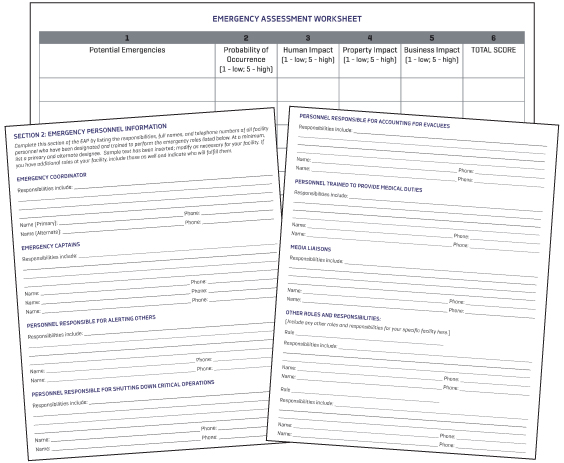
That scenario is an example of why “accounting of employees” is one of the many required elements of an emergency action plan. At a recent meeting of the Western Propane Gas Association (WPGA), the association’s safety consultant, Rob Scott, explained that propane marketers should know each day who has shown up to work and who hasn’t.
An emergency action plan isn’t something that’s created once; it’s something that must be reviewed on a regular basis. “There’s always an accident waiting to happen,” Scott said. “The question is: Are we ready for it?”
That, he noted, is what an emergency action plan is for. In his presentation, he focused on two questions: What’s in your plan? Has it been reviewed?
An emergency action plan is a written document that facilitates and organizes employer and employee actions during workplace emergencies. Its benefits are fewer and less severe injuries; less structural damage; and reduced confusion.
The required elements of an emergency action plan include a means of reporting; evacuation procedures and emergency escape routes; procedures for critical operations; accounting of employees; rescue and medical duties; and contact persons.
Scott listed different sorts of emergencies. They include natural incidents, such as floods or tornadoes; technological incidents, such as chemical release and vehicle accidents; and man-made incidents, such as civil disturbances or workplace violence.
He told of a recent incident in which customers were unhappy that they would not be paid for the propane left in a cylinder. One of them brought out a knife. Scott asked, “Would your driver know what to do?”
OTHER PROCEDURES
In addition to an emergency action plan, other emergency planning procedures include exit routes; fire prevention plans; hazardous waste operations and emergency response; permit-required confined spaces; fire brigades; portable fire extinguishers; fixed extinguishing systems; fire detection systems; and employee alarm systems.
Scott suggested developing habits to adhere to these requirements. For example, if your fire extinguishers are inspected annually, do fire extinguisher training at the same time. You can test employees while the inspector is onsite.
He then walked the audience through an emergency assessment process, using a worksheet that is available from the Propane Education & Research Council (PERC).
On the worksheet, you write down potential emergencies that could affect your plant. For each, you then estimate the probability of each emergency’s occurrence and assess the potential human impact, property impact, and business impact. Each is assigned a number, representing high or low probability or impact.
“We want to see near zero if we can,” Scott said. Those that do have higher totals, though, are those that should be given the highest priority and resources. But, he added, all emergencies should be planned for, and none should be ignored.
He then outlined a resource assessment. This includes assessing the personnel; the facility; and equipment and supplies. Among the questions to ask here are: Do we have first aid kits in trucks? Have we hired someone new? If so, have personnel records been updated? Is all necessary personal protective equipment available at the facility? Scott told of a driver who recently showed him his new leather gloves. The gloves were not the required gas gloves.
COMMUNICATION
Communication is another element of an emergency action plan. Requirements here include a designee for alerting and assisting employees and others during an emergency; alarms that are distinctive and recognized by all employees; and post-emergency phone numbers. The plan should also include the details needed for notifying emergency responders, utility companies, the National Response Center (NRC), the Department of Transportation (DOT), and the Occupational Safety and Health Administration (OSHA).
Scott suggesting taking into account the response time of not only the fire station closest to your plant, but also the second closest. He explained that the one that’s closest might be out on a call when you need them.
Evacuation is another element of the emergency action plan. The plan should identify an emergency coordinator; evacuation captains; individuals responsible for shutting down critical operations; individuals responsible for accounting for evacuees; evacuation routes and exits; and evacuation maps and drawings.
“In an emergency, everyone’s natural reaction is to run,” Scott noted. “But someone needs to push the shutoff button.”
Propane marketers also should collaborate with others before an emergency. Others who can help include employees; company officials and management; local emergency responders; local and state government; local emergency planning committees; and community and civic groups.
“It’s all about building networks and alliances,” Scott said. He suggested attending meetings of the local fire chiefs’ association. “They will appreciate your participation.”
Keeping employees current on the emergency action plan requires distributing the plan, maintaining the plan, and training on the plan. Training should include both classroom activities and practice drills. “We can never do enough training,” Scott noted.
When all these elements of an emergency action plan are known and reviewed, everyone will be as ready as they can be when something unexpected happens—for instance, something that might lead to employees evacuating and gathering outside. — Steve Relyea