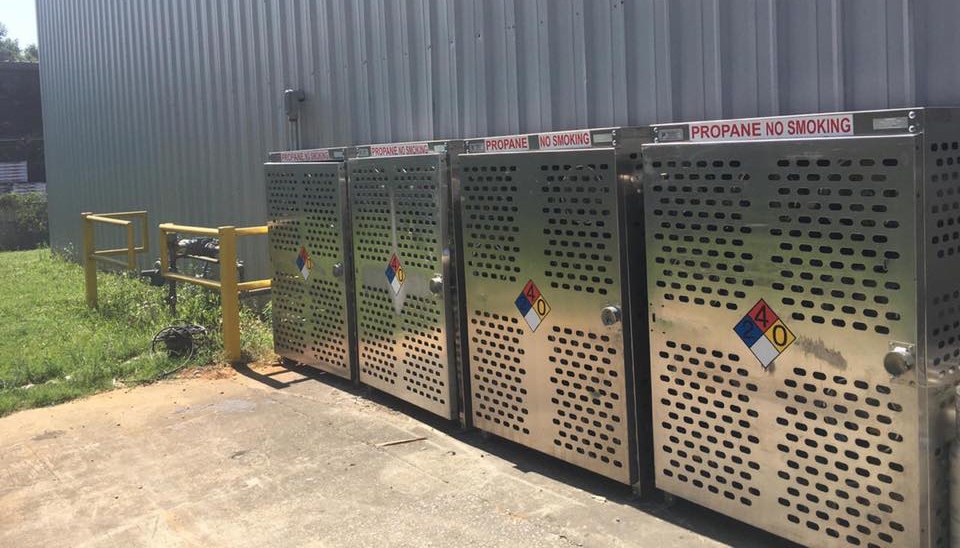
In the world of cylinder cages, it’s all about reliability, safety and durability. After all, cylinder cages protect a commodity from tampering and ensure safety compliance for the good of the customers — as well as the company providing propane to the masses. In that regard, it’s important for propane companies to conduct their cylinder exchange business with an attention to security issues. To highlight the latest updates in cylinder cages that could strengthen your cylinder exchange business, the American Standard Manufacturing team gave some feedback to BPN on what you may need to know.
What’s been trending in terms of updates to cylinder cage design in recent years?
It appears that in all the challenges we are facing as a nation, the propane storage industry is not excluded. Theft of cylinders has always been an issue but seems to be on the rise, and quite often security issues come up as a topic from our customers. Our first response to the issue back in the early 2000s was to introduce aluminum cabinets. These are more dense and harder to cut into. We also had them seismically tested in California, and they fared much better than their steel unit counterparts.
Are there any design changes coming down the pipeline at ASM that will lead to improvements in functionality and safety?
ASM customers have been coming to us for a few years asking for improved security options. After many meetings and design changes, we have shared a few concepts with a few high-volume customers and have come up with a cabinet that will have much denser panels (fewer punched holes), but will still provide the ventilation that is needed. The new punch pattern for all aluminum units will have holes that are in line with the shelves and racks, thus making much more work for the thieves. No other changes have been made to the cabinets. We can’t make them 100% thief-proof, but we can make their job much more challenging.
What particular care is taken for customer safety in cage design?
Our cabinets and equipment are designed with the utmost concern for the safety of customers and the end users. We make no guarantees because it truly depends on the placement and setup of the products.
Are there any design updates that the industry at large should consider in the coming years?
We will continue to listen to our customers and make every effort we can to meet challenges as they arise.
What type of anti-theft improvements could be made to enhance product safety across the cylinder exchange sector?
As [Coleman Vickary] (founder of ASM and the cylinder exchange concept) always says, locks and security devices only keep the honest folks out!
What are the advantages/disadvantages between aluminum and steel when choosing cage material?
The aluminum cabinets are more dense and harder to cut into. And, as mentioned previously, we also had them seismically tested in California, and they fared much better than steel units. The steel units are welded mesh into angle iron — this could be easily cut into or even just kicked out.