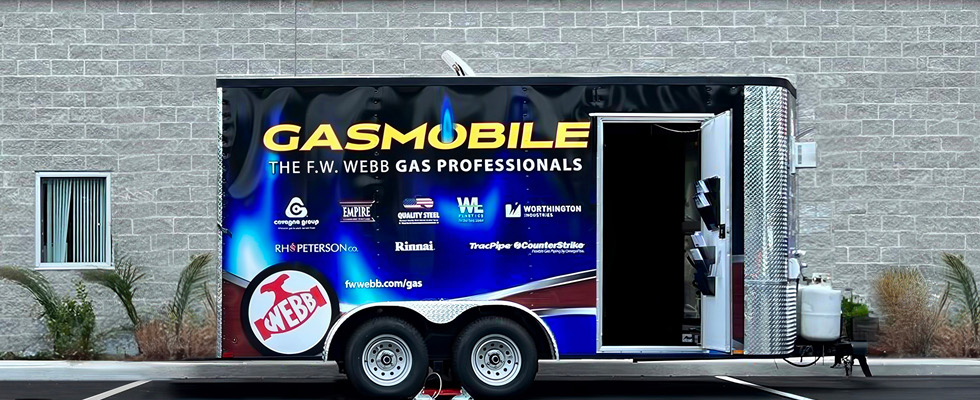
Technology, regulations, market conditions and macro trends are in constant flux across the propane industry. The ongoing transformation makes continuing industry education essential.
“Safety is paramount in our industry,” says Michael DelConte, vice president of heating and LP gas sales at F.W. Webb Company. “Therefore, proper training is foundational; we all must strive to keep technicians and end users safe, not only during installations or system startups, but also during routine maintenance that occurs throughout the service life of the components, systems and equipment we supply. In many cases, understanding and utilizing cutting-edge technology can significantly reduce how long it takes to complete projects, freeing up valuable time for both the technician and the end user.”
Training opportunities can also allow distributors to improve customer service. Given the complexity of many propane industry applications and the precision required to address issues that arise, distributors can foster better customer relationships when they educate professionals about the products they install. As a result, these educational opportunities can help serve as the basis for productive, long-term customer relationships.
The Importance of Mobile & Hands-On Training
Because of time constraints and the hands-on nature of their work, propane professionals can use mobile and experiential training classes as a valuable resource for acquiring industry knowledge.
For instance, DelConte’s company uses two live-fire training vehicles that essentially deliver safety training classes directly to propane company employees. With busy professionals who cannot rearrange their schedules to attend sessions several hours away, finding a training process that is convenient for employees is essential in an industry reliant on both safety and efficiency. Options such as F.W. Webb’s training vehicles also enable companies to coordinate and schedule multiple training sessions on location.
Each training vehicle offers over a dozen different classes, including underground liquid propane tank installation and cathodic protection, bulk plant maintenance and pump station design and maintenance. However, it’s important to also focus on training that is customizable to your employees’ training needs. For example, one of the F.W. Webb vehicles recently held a log set training, generator class, tank training session and LP fundamentals class all in one week.
During the classes, propane professionals worked directly on products or equipment. To simulate real-world, on-the-job experiences, trainers could bring products into a building and connect them to gas lines. In addition, technicians disassembled and reassembled products under the guidance of seasoned trainers. While not as formal as apprenticeships, the relationships developed during these training events might be described as “knowledge partnerships.” Thanks to these partnerships, technicians can augment their product and equipment knowledge and help push the industry forward by adopting new technologies and methods.
Leveraging Trusted Manufacturer Partnerships
“We rely on our manufacturer partners for much of the content that forms the foundation for many of our mobile and on-site training sessions,” says DelConte. “Our partners also collaborate with us to share updates about product innovations. Manufacturers help us align with macro trends that dictate where the propane industry is headed.”
Initially, manufacturers might provide products, brochures, videos and other materials to support training opportunities. As partnerships grow, training opportunities evolve. Over time, classes might focus on single product lines or product developments. According to DelConte, partnerships with manufacturers are how training providers can incorporate resources to help propane professionals stay up to date on the latest product information and installation methods.