Wednesday, August 30, 2017
(August 30, 2017) — The Certified Employee Training Program, CETP, is marking its third decade affording accredited, industry-leading instruction to propane company personnel this year. Launched in 1987, the world-class and widely recognized curriculum has undergone several revisions to expand access and flexibility and pare expense. But the scope of the propane industry’s safety efforts include much more. With the safe use and handling of propane by customers and workforce professionals the industry’s top priority, a variety of materials have been developed for various audiences by the Propane Education & Research Council (PERC). The list continues to grow.
PERC’s wide-ranging outreach is committed to ensuring the safety of consumers who use and depend on propane to heat homes, cook food, tend landscapes, and power appliances that enrich lives. Its Propane Emergencies program has been adopted by 27 state firefighter training agencies, as well as by numerous marketers. It helps emergency responders develop the skills necessary to manage a propane emergency in both transportation and at fixed facilities. The council also provides resources to assist operators of propane equipment and autogas vehicles. Compliance materials are offered to provide information on U.S. Department of Transportation, Occupational Safety and Health Administration, and Environmental Protection Agency regulations that apply to propane and what must be done to meet regulatory requirements.
Further, the extensive and sustained work to promote safety in all aspects of operations is seen by the National Propane Gas Association (NPGA) as an attribute to be promoted as work by the Workforce Development Task Force ramps up. The panel of volunteer propane professionals is developing recommendations and strategies to attract younger employees to the industry. Propane’s good safety record, in addition to the extensive availability of career-building training opportunities, will likely factor in task force recruitment recommendations.
Stuart Flatow, vice president of safety and training at PERC, comments, “The primary focus is to reduce barriers to quality training and communicate with customers about safety, mindful that efforts must be aimed at helping marketers with the challenges of retaining customers, getting insurance and supply, and retaining workers. In other words, provide useful services to our frontline people.”
Flatow outlines that a recent initiative to further streamline instruction and boost effectiveness is PERC’s blended learning program, which is designed to reduce time out of the office while expanding the knowledge employees need to do their jobs safely and effectively. He explains that blended learning is a hybrid approach combining online training with classroom work that allows time to review online prior to attending a class. As a blend of online and classroom education, the approach allows more time for instructors to focus on technical concepts, to conduct more hands-on activities, and provide additional time for review before students take the NPGA CETP certification exam. Access to online learning is free.
“Blended learning is CETP online,” Flatow clarifies. “It lowers the barrier of driving 200 miles to receive training and recognizes that not everyone learns in the same way. Blended learning will also benefit the employer, who will go online and register the employee, who then will complete the training by a set time.” He expands that marketers have told PERC they like programs that provide advancement “in smaller pieces,” and that as employees embark on their industry education the CETP curriculum can be broken down into “bite-size pieces online” that facilitate “mini-training” that is task appropriate.
The PERC vice president emphasizes that in developing its training programs, the council consults with workforce development and certification professionals, technical schools, and employers. All are fully vetted prior to roll-out. The development process is not top-down, but rather bottom-up. “We interview marketers to learn about their challenges in hiring and training. We contact technical school boards to gather their expertise regarding curriculum and job placement. There are robust communications within the industry before we ask for funding.”
That communication and outreach includes state propane gas association executives, especially, but not exclusively, at the industry’s annual National Trainers Conference. Flatow says a breakout session at the event seeks to engender a shared vision of workforce training and development with the aim of reducing barriers and ensuring employees understand concepts. He adds that with 30% of students failing the skills assessment, training can be moved forward under blended learning by breaking the CETP curriculum down into smaller segments, the completion of which is documented and kept on file.
“This assists with the recruitment of younger people who are more adept with an online curriculum,” says Flatow, as well as expediting company training efforts through more manageable and skill-acquired stages. The goal is not to negate or undermine the NPGA skills assessment or certification, but rather to add flexibility through a task-based, step-by-step certification process. “This is another move in the direction of a streamlined, more effective, less costly system. Marketers are our customers and we are alert to their needs. We have our ears to the ground to learn what they want. Again, the goal is to reduce barriers.”
In addition, refresher training is available online that can be customized with state-specific requirements. The new Remaining Current program utilizes each CETP certification area. CETP certification holders need to complete the refresher training once every three years for each certification they hold. No written test or skills assessment is required. All courses are available as a PowerPoint presentation. For those CETP training programs currently in an e-learning format, the refresher training will be available online through the Industrial Training Services OnBoard LMS (Learning Management System).
Importantly, an existing certification will not expire or be considered invalid if refresher training is not completed. As well, if the training is completed online, records are updated automatically. If it is completed in a classroom, a registered proctor or skills evaluator will submit the information to Industrial Training Services to update the records. While the training is available at no cost, NPGA charges a $35 fee for transcripts and recordkeeping.
On the consumer side, Flatow notes the objective is to not only lift barriers but to mitigate the “fear factor.” PERC has developed a series of six consumer safety videos designed to advance propane in a soft-sell manner and as a smart choice. Included are simple steps to take to stay safe. They also include information on natural gas coming into a community, completing conversions safely, and what to do so as not to void an equipment warranty.
The council has also developed an online video that addresses do-it-yourselfers. It may be viewed at diysafety.org. “If you’re planning to install, service, relocate, or repair propane equipment on your own, it’s a good idea to know about the unnecessary costs and risks associated with repairing propane equipment yourself,” viewers are cautioned. Emphasized is that when handling propane it’s best to leave it to a qualified professional. There is also a short form that can be filled out to connect property owners with a propane pro.
Recruitment
Eric Kuster, director of safety and certification at NPGA, is serving as the association’s staff liaison for the Workforce Development Taskforce. He reports the panel is focusing on leveraging the propane industry’s extensive safety and training efforts to attract new entry-level personnel, and that new materials are being sketched out with the aim of making them available by the first of next year.
He adds that what’s being discussed is how to improve delivery methodologies. Paper and DVDs have moved online and may migrate further to mobile devices such as smart phones and tablets. “This would be a way to make safety information available to field staff at a moment’s notice,” Kuster observes, “and the younger workforce is immersed in the technology and knows how to use it. To them it has a modern, familiar look and feel.” However, work must be coordinated with NPGA’s codes and standards team so safety won’t be compromised.
Mollie O’Dell, NPGA vice president of communications, asserts that CETP is a positive for the industry’s employee recruitment initiative. “It can teach you a trade and provide a wide variety of career opportunities—from the office to delivery. The materials marketers have in hand can provide a career path for new employees. The propane industry has a great safety record to stand on, and a training program that provides an abundance of learning opportunities.” —John Needham
(Published in the August 2017 ediiton of Butane-Propane (BPN) magazine)
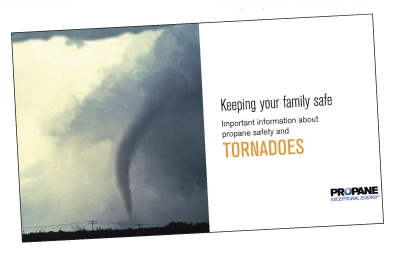
PERC’s wide-ranging outreach is committed to ensuring the safety of consumers who use and depend on propane to heat homes, cook food, tend landscapes, and power appliances that enrich lives. Its Propane Emergencies program has been adopted by 27 state firefighter training agencies, as well as by numerous marketers. It helps emergency responders develop the skills necessary to manage a propane emergency in both transportation and at fixed facilities. The council also provides resources to assist operators of propane equipment and autogas vehicles. Compliance materials are offered to provide information on U.S. Department of Transportation, Occupational Safety and Health Administration, and Environmental Protection Agency regulations that apply to propane and what must be done to meet regulatory requirements.
Further, the extensive and sustained work to promote safety in all aspects of operations is seen by the National Propane Gas Association (NPGA) as an attribute to be promoted as work by the Workforce Development Task Force ramps up. The panel of volunteer propane professionals is developing recommendations and strategies to attract younger employees to the industry. Propane’s good safety record, in addition to the extensive availability of career-building training opportunities, will likely factor in task force recruitment recommendations.
Stuart Flatow, vice president of safety and training at PERC, comments, “The primary focus is to reduce barriers to quality training and communicate with customers about safety, mindful that efforts must be aimed at helping marketers with the challenges of retaining customers, getting insurance and supply, and retaining workers. In other words, provide useful services to our frontline people.”
Flatow outlines that a recent initiative to further streamline instruction and boost effectiveness is PERC’s blended learning program, which is designed to reduce time out of the office while expanding the knowledge employees need to do their jobs safely and effectively. He explains that blended learning is a hybrid approach combining online training with classroom work that allows time to review online prior to attending a class. As a blend of online and classroom education, the approach allows more time for instructors to focus on technical concepts, to conduct more hands-on activities, and provide additional time for review before students take the NPGA CETP certification exam. Access to online learning is free.
“Blended learning is CETP online,” Flatow clarifies. “It lowers the barrier of driving 200 miles to receive training and recognizes that not everyone learns in the same way. Blended learning will also benefit the employer, who will go online and register the employee, who then will complete the training by a set time.” He expands that marketers have told PERC they like programs that provide advancement “in smaller pieces,” and that as employees embark on their industry education the CETP curriculum can be broken down into “bite-size pieces online” that facilitate “mini-training” that is task appropriate.
The PERC vice president emphasizes that in developing its training programs, the council consults with workforce development and certification professionals, technical schools, and employers. All are fully vetted prior to roll-out. The development process is not top-down, but rather bottom-up. “We interview marketers to learn about their challenges in hiring and training. We contact technical school boards to gather their expertise regarding curriculum and job placement. There are robust communications within the industry before we ask for funding.”
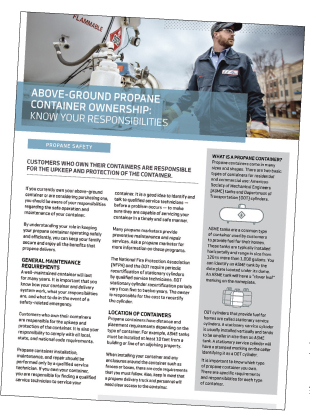
That communication and outreach includes state propane gas association executives, especially, but not exclusively, at the industry’s annual National Trainers Conference. Flatow says a breakout session at the event seeks to engender a shared vision of workforce training and development with the aim of reducing barriers and ensuring employees understand concepts. He adds that with 30% of students failing the skills assessment, training can be moved forward under blended learning by breaking the CETP curriculum down into smaller segments, the completion of which is documented and kept on file.
“This assists with the recruitment of younger people who are more adept with an online curriculum,” says Flatow, as well as expediting company training efforts through more manageable and skill-acquired stages. The goal is not to negate or undermine the NPGA skills assessment or certification, but rather to add flexibility through a task-based, step-by-step certification process. “This is another move in the direction of a streamlined, more effective, less costly system. Marketers are our customers and we are alert to their needs. We have our ears to the ground to learn what they want. Again, the goal is to reduce barriers.”
In addition, refresher training is available online that can be customized with state-specific requirements. The new Remaining Current program utilizes each CETP certification area. CETP certification holders need to complete the refresher training once every three years for each certification they hold. No written test or skills assessment is required. All courses are available as a PowerPoint presentation. For those CETP training programs currently in an e-learning format, the refresher training will be available online through the Industrial Training Services OnBoard LMS (Learning Management System).
Importantly, an existing certification will not expire or be considered invalid if refresher training is not completed. As well, if the training is completed online, records are updated automatically. If it is completed in a classroom, a registered proctor or skills evaluator will submit the information to Industrial Training Services to update the records. While the training is available at no cost, NPGA charges a $35 fee for transcripts and recordkeeping.
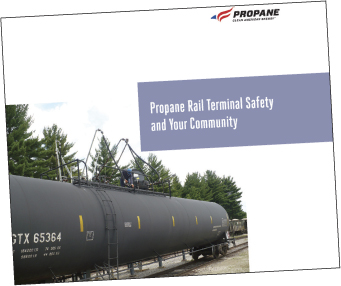
On the consumer side, Flatow notes the objective is to not only lift barriers but to mitigate the “fear factor.” PERC has developed a series of six consumer safety videos designed to advance propane in a soft-sell manner and as a smart choice. Included are simple steps to take to stay safe. They also include information on natural gas coming into a community, completing conversions safely, and what to do so as not to void an equipment warranty.
The council has also developed an online video that addresses do-it-yourselfers. It may be viewed at diysafety.org. “If you’re planning to install, service, relocate, or repair propane equipment on your own, it’s a good idea to know about the unnecessary costs and risks associated with repairing propane equipment yourself,” viewers are cautioned. Emphasized is that when handling propane it’s best to leave it to a qualified professional. There is also a short form that can be filled out to connect property owners with a propane pro.
Recruitment
Eric Kuster, director of safety and certification at NPGA, is serving as the association’s staff liaison for the Workforce Development Taskforce. He reports the panel is focusing on leveraging the propane industry’s extensive safety and training efforts to attract new entry-level personnel, and that new materials are being sketched out with the aim of making them available by the first of next year.
He adds that what’s being discussed is how to improve delivery methodologies. Paper and DVDs have moved online and may migrate further to mobile devices such as smart phones and tablets. “This would be a way to make safety information available to field staff at a moment’s notice,” Kuster observes, “and the younger workforce is immersed in the technology and knows how to use it. To them it has a modern, familiar look and feel.” However, work must be coordinated with NPGA’s codes and standards team so safety won’t be compromised.
Mollie O’Dell, NPGA vice president of communications, asserts that CETP is a positive for the industry’s employee recruitment initiative. “It can teach you a trade and provide a wide variety of career opportunities—from the office to delivery. The materials marketers have in hand can provide a career path for new employees. The propane industry has a great safety record to stand on, and a training program that provides an abundance of learning opportunities.” —John Needham
(Published in the August 2017 ediiton of Butane-Propane (BPN) magazine)