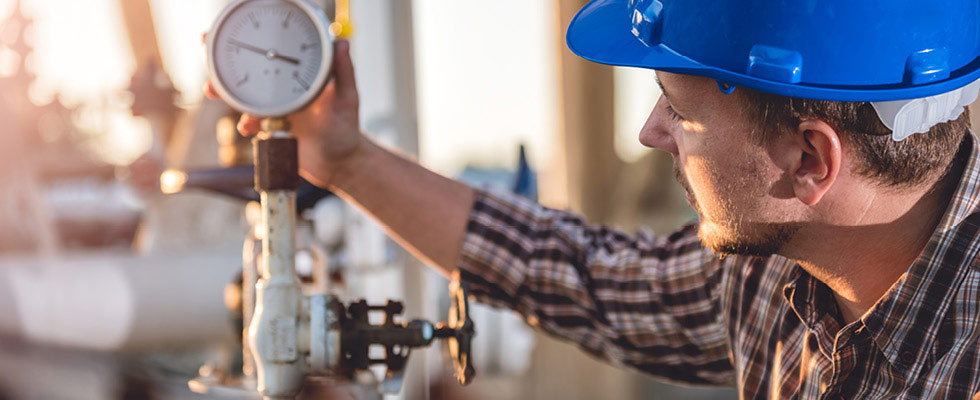
As all propane marketers know, trying to stay on top of constantly changing safety codes and regulations can be a challenge. You’re already dealing with staffing issues, ongoing equipment maintenance, changes to delivery schedules — which are especially complicated during the winter season — and myriad other daily operational requirements. But the safety of your employees and your customers must remain your highest priority.
Establishing a system to address constant updates to safety codes and regulations is crucial to your company’s success. Of course, you want to keep your employees and customers safe — it is the right thing to do — but it’s also important to understand your company may never overcome a major safety incident that triggers serious harm to a customer or a team member. Not only would that cause you mental and emotional anguish for years, but the financial costs also involved could devastate your company. Propane businesses that experience such a horrendous incident rarely recover.
Aside from it being the right thing to do, you also want to establish a reputation in your community for providing safe, reliable service. Being known for staying on top of safety codes and regulations is extremely important in gaining new customers and retaining your existing customers.
Your Company’s Value Is at Stake
There is another important reason to stay on top of ongoing changes to safety codes and regulations: The value of your company is at stake. If you don’t have the latest safety protocols in place and the documentation to support those protocols, the valuation of your company by a potential buyer will likely not match the amount you hope for.
In fact, at EDP, when we assess a company as a candidate for acquisition, we take a very close look at that company’s safety standards, practices and documentation. If they don’t meet our requirements, we will likely pass on moving forward with plans to acquire that company.
So, if you are thinking about selling your business in the coming years, it is crucial to stay on top of the latest safety codes and regulations — as well as safety training protocols and the documentation to support it — in order to achieve the sale price you’d like.
But how do you stay on top of constantly changing safety codes and regulations? There are steps you can take to ensure you stay abreast of these changes in the future. Here are nine suggestions that should help:
- Implement the Propane Education & Research Council’s (PERC) safety training for your employees. If you haven’t already required all your employees to complete PERC’s safety training courses, now is the time. PERC’s new task-based programs — with specific courses based on job titles/function — are accredited through the International Accreditors for Continuing Education & Training. They can be done either online through the PERC Learning Center or in traditional instructor-led classes, in-house or through a state propane gas association. They are replacing PERC’s Certified Employee Training Program. Not only is it important for all your employees to participate in these industry safety training courses, but it is also an excellent way to position your company as a safety-first operation. When you can honestly tell your customers that all of your employees have gone through safety training, that says a lot about your company’s safety culture. Be sure to promote that on your website.
- Look to your industry associations. National industry associations like the National Propane Gas Association (NPGA) and PERC offer invaluable information for those running a propane business. At the very least, you should pay attention to their ongoing safety updates. But it is also imperative you pay close attention to your state or regional association, since updates to regulations can vary by state. Pay your dues, watch for their educational and safety updates and — as noted above — take advantage of the safety training programs they offer.
- Safety culture starts at the top. Insist on monthly safety meetings with your team. Don’t skip them. When your monthly safety meetings lapse into occasional meetings, your employees will sense that safety is not a high priority for you. That is not the kind of culture that will build their confidence in your leadership and it won’t help you win new customers or retain existing customers over the long term. In fact, safety-focused managers should consider scheduling one longer monthly safety meeting, then holding shorter meetings throughout the month as new safety issues — such as code and regulation updates — arise.
- Sign up with the National Fire Protection Association (NFPA) to receive their updates. The NFPA is constantly updating both NFPA 58 and NFPA 54 requirements, so paying attention to those updates is crucial.
- Read your trade publications. In addition to national print trade magazines, watch for regular weekly or monthly email updates. Furthermore, be sure to also thoroughly read the magazines, newsletters or emails produced by your state or regional association.
- Attend industry meetings and conferences. Depending on the size of your operation, you may not be active with NPGA or PERC. But even members who are not active month-in and month-out can benefit from attending association meetings. For instance, the NPGA’s annual Southeastern Expo — which took place in April in Charlotte, North Carolina — always offers valuable sessions on safety codes and regulations. Likewise, the Western Propane Gas Association’s (WPGA) annual convention in May in Reno, Nevada, offered similar safety sessions. In fact, the WPGA offered a session focused on NFPA 58 in this year’s conference schedule. So, between state, regional and national industry associations, you have multiple options to choose from for scheduling safety training for you and your team.
- Look to your vendors and suppliers. The industry professionals you turn to when buying equipment like tanks, regulators, meters, valves, etc., are constantly working to ensure the equipment they sell meets the latest safety standards. So, reach out to your vendors and suppliers with questions about the products they sell. They can be a wealth of insights and information and are often willing to provide personalized training sessions for your employees.
- Read equipment and parts manuals. In addition to talking with your vendors and suppliers about safety updates to their products, read their manuals and keep them handy. Share information from these manuals with your team members during your regular safety meetings and be sure your technicians read through the manuals thoroughly. Also, ensure you have a filing system for these manuals so they are at your fingertips when questions arise.
- Partner with your insurance company. Your insurance provider has a vested interest in making certain you run a safe operation. Don’t just consider the company as a “vendor.” Work closely with them to ensure you have not only the latest information, but also the best coverage for your business.
In summary, staying on top of constantly changing safety codes and regulations for your propane operation can initially seem overwhelming. By embracing these suggestions, you should find it a bit easier to manage those changes without too many headaches.