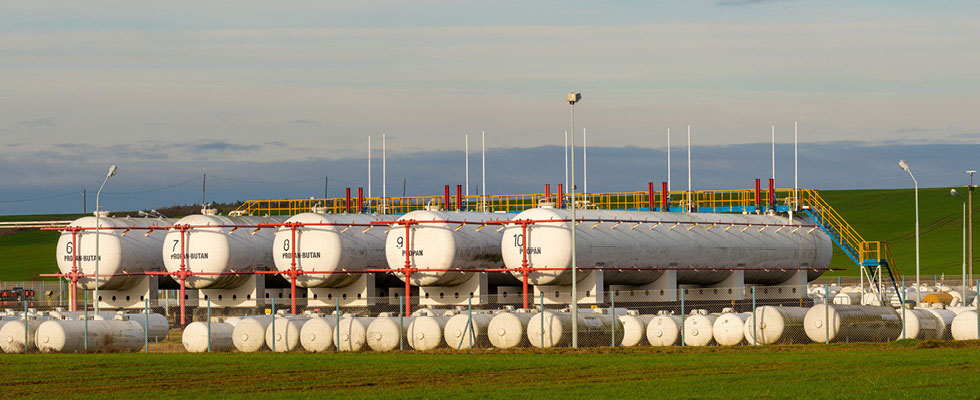
Have you ever wondered what the most common regulatory compliance violations are at bulk plant operations and how they can be resolved? We’re going to dive into the most frequent issues uncovered during bulk plant inspections.
Maintaining regulatory compliance with respect to your bulk plants can be a challenge; that’s why it’s critical to know what to keep an eye out for — along with having a bulletproof inspection and maintenance process — to help your facility and employees stay safe and secure.
Emergency Shutoff Valves Not Working Correctly
The most frequent issue I encounter at bulk plants is emergency shutoff valves (ESVs) not being used properly. Every staff member handling propane needs to be trained on how and why the ESV policy should be followed. After all, if an emergency situation calls for it, ESVs must be able to close at a moment’s notice.
The ESV that closes the vapor and liquid valves to the container and piping in your bulk plant can experience many issues, especially when they are not tested regularly. Common problems include not closing due to a lack of maintenance or getting stuck in the open position. Management at your bulk plants should verify the ESVs at least once a month to ensure the valves work properly and identify any parts that need to be replaced.
Unsecured Vapor & Liquid Hoses
Vapor and liquid hoses being unsecured without the presence of a qualified individual are a major (and common) issue at bulk plants that I have inspected during my time as a propane safety expert and bulk plant inspector. Vapor and liquid hoses should always be secured and only engaged in the presence of a representative. They should also be properly plugged and/or capped to protect hose-end fittings. Compliance in this area will greatly reduce the risk of a catastrophe and help protect the safety of your propane bulk plant establishment.
Safety Decals & Markings Missing or Unreadable
Over time, safety decals and markings will fade away due to weather conditions and regular wear and tear, causing a potential safety issue. Replacing these markings and decals when they show signs of aging or fading is an easy preventative measure to stay in compliance and provide new and seasoned hazmat handlers with the details they need to keep safe. Don’t let these safety decals and markings at your bulk plants be something your team takes for granted — they should be highly visible and in good enough condition to be easily deciphered by anyone handling the materials or equipment.
Unlocked Gates & Incomplete Fences
Did you know that many bulk plants aren’t entirely fenced in? Have you heard that some bulk plant operators don’t lock their front gate, or use a dummy lock that only looks secure? Recently, a propane marketer who left their bulk plant unlocked was featured in an online video that a content creator made. This is a dangerous hazard and leaves a bad taste in viewers’ mouths when they think about your brand. Having a complete fence around your bulk plant and locking gates at night is one simple way to prevent bobtail theft, personal injury and other liabilities.
Methanol Stored Within 20 Feet of Propane Storage Containers
Finally, all propane containers should have proper crash protection. Methanol should be stored in a cool, dry, well-ventilated area away from direct sunlight and moisture, and it should also be kept a minimum of 20 feet from the point of transfer. Methanol being stored too close to propane can spell trouble for your bulk plants, which is why it’s important to check where your methanol is being stored and choose a new location if it is too close to where propane is stored.
Identifying & Resolving Common Issues at Propane Bulk Plants
Do you complete annual, as well as monthly, bulk plant inspections? How does your team track issues and remediation for problems discovered during the inspections? How do you train new individuals who may be responsible for your bulk plant inspections?
Paper and PDF safety inspections are a thing of the past, and the new standard has become digital propane safety inspections, which are completed, saved and recalled on the cloud. If you have multiple locations, some platforms allow you to look at the status of all locations in a single dashboard, saving you time and improving your operational efficiency. Using the latest technology plays a key role in better regulatory compliance — it is more efficient than paper forms and PDFs and can save you billable hours. You can use digital routine bulk plant inspections to reduce the rate of omissions and errors within your inspection reports and highlight any potential safety issues. Some platforms even automatically generate management reports, which can help identify important follow-ups.
I highly recommend consulting a propane safety expert for assistance with your bulk plant inspections and reporting. By doing so, you will greatly reduce your error rate and do your part in keeping your community and company safe and secure.