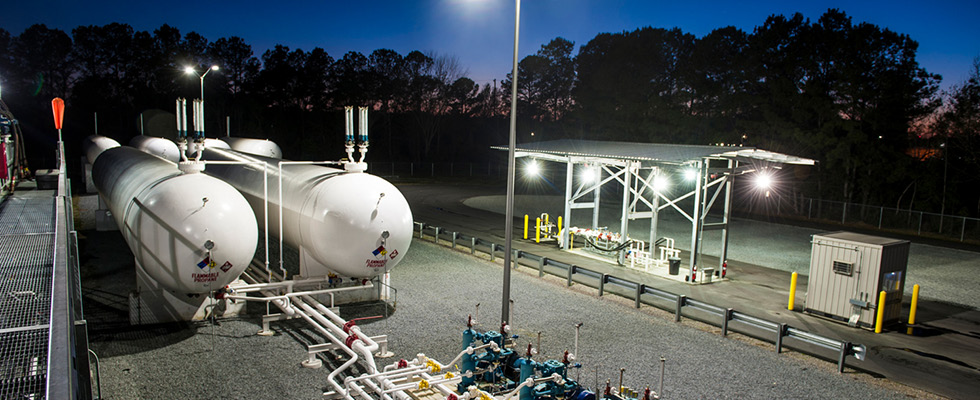
Safety is always a top-of-mind issue for members of the propane industry, but it is a way of life for those working in propane terminals. If compliance is not ingrained into company culture, the consequences can be lethal.
To get deeper insights on the critical role safety plays in midstream propane terminals, BPN heard from Mike Walters, vice president of safety and fleets at Superior Energy Systems.
Can you describe your current role at Superior Energy Systems?
I am vice president of safety and fleet. I operate the safety program and training-related content. I have a responsibility to help Superior Energy Systems provide a safe workplace and help the employees work safely at the same time. It’s a very unique position to be in.
Have you always been interested in safety? If not, what led you to pursue a career in that field?
I didn’t pursue it. In my industry hall of fame speech, I talked about this when I was acknowledging people in the industry — people putting you into positions you weren’t qualified for and letting you grow into it. I didn’t even intend to be in the propane industry. It found me.
Back in those days, safety was about compliance and equipment. [If] you comply with all the codes and laws and have decent working equipment, you’re safe, right? We would inspect the plant, the equipment and the trucks.
But that is just a piece of the puzzle. I joined the National Fire Protection Association and the American Society of Safety Engineers (now known as the American Society of Safety Professionals), and I took a couple of classes.
After a couple of months, the light went on. Safety is about the people. Safety is about behavior — the decisions people make, the situations they put themselves in. Educating people to lead them toward making a better decision is everything when it comes to safety.
What are a couple of the most critical safety implementations at a midstream propane terminal?
Generally, terminals have to comply with regulations beyond the rest of the industry, like process safety management. It’s not so much a regulation, it’s a lifestyle. It’s the way you operate the facility. Process hazard analysis means that during every task that’s performed — from hooking up the truck to transferring liquid — the individual performing the task is aware of what the accident probability is. Everything must be approached and executed with a risk matrix.
How have you witnessed propane safety evolving? What can we attribute that evolution to?
One of the biggest things that happened with respect to behavioral safety in the propane industry was [the Propane Education & Research Council’s] embrace of Charlie Morecraft. ‘Remember Charlie’ is a film of a 56-minute presentation that he gives.
There was a gasoline additive mix, and ignition occurred because he left his truck running. There was a big fire and he was severely burned. He talked about how it affected him and everyone around him. He took safety for granted.
What we learned from him is that safety is about behavior and the decisions people make. Yes, safety is still about compliance and equipment to a degree, and we have [Department of Transportation] and [Occupational Safety & Health Administration (OSHA)] mandates to follow, but equipping people to make the right decisions is critical. But, taking ownership of your own personal safety and not taking safety for granted is [Charlie’s] message. He says it is time to lose the ‘it’ll never happen to me’ attitude.
How is safety coordinated from the terminal builder perspective? Is responsibility for safety during the terminal build outlined by the contracted builder or the company that owns the terminal?
I would say both. When you’re building a terminal from scratch, you’ve got bare ground, so there is really nothing for the property owner to drive with respect to safety. The industry in general operates under General Industry standard, OSHA 1910, but we at Superior Energy Systems operate under the Construction Standard, OSHA 1926, which is more stringent. Once the terminal is built, then the owner of the terminal is driving a piece of it, but the contractor drives some of it, too. OSHA regulations have changed throughout the last decade. It’s a joint effort.
How can propane companies help ensure safety standards are implemented? What role does company culture play in effectively integrating safety codes?
Company culture is everything. If the company culture isn’t right, the employees know it. Leading by example is important, and that demonstrates the company culture. At Superior Energy Systems, we have an excellent safety culture, and I’ve watched the owner of the company voice it. We have many policies and procedures, including a Stop Work Authority, which gives employees the option to stop work if there is an unsafe condition. This policy gives them the ability to take ownership of their safety.
What do you feel is the best way to get employees on board with critical propane safety guidelines?
Dialogue — keeping clear and consistent dialogue between employees and encouraging them to always put safety first. What I tell my people is, if you’re doing something and you think, ‘That could have turned out bad,’ that can be labeled a near miss of injury or incident, and you must stop and find a safer way. It is critical that employees feel comfortable coming to their supervisors and each other for help with finding that safer way.
Can you describe the Personal Risk Assessment you developed? What tips would you give for companies looking to use a similar tool for their own employees?
I wrote that for AmeriGas in the mid-2000s. The Personal Risk Assessment is about the people. For every task, ask yourself a series of questions. First, survey your surroundings and ask yourself, ‘Will I be in a safe position? Do I have the right equipment? Is it in good working condition? Do I have the personal protective equipment I need? Have I been trained for this task?’ And the last question is, ‘What’s the worst that could happen?’
If the answer to the above is an accident or an injury, then you have to stop and find a safer way. I tell people that everybody should commit this concept to their subconscious for use in their everyday lives.
Are there any immediate resources available to companies that might not be able to hire a full-time safety manager? Where would you suggest they begin?
I would say the appropriate place to start is reaching out to your state propane association. Usually, safety individuals like me are engaged in state associations. If you can’t have a full-time safety manager, you can always get a consultant. That’s where you should begin.