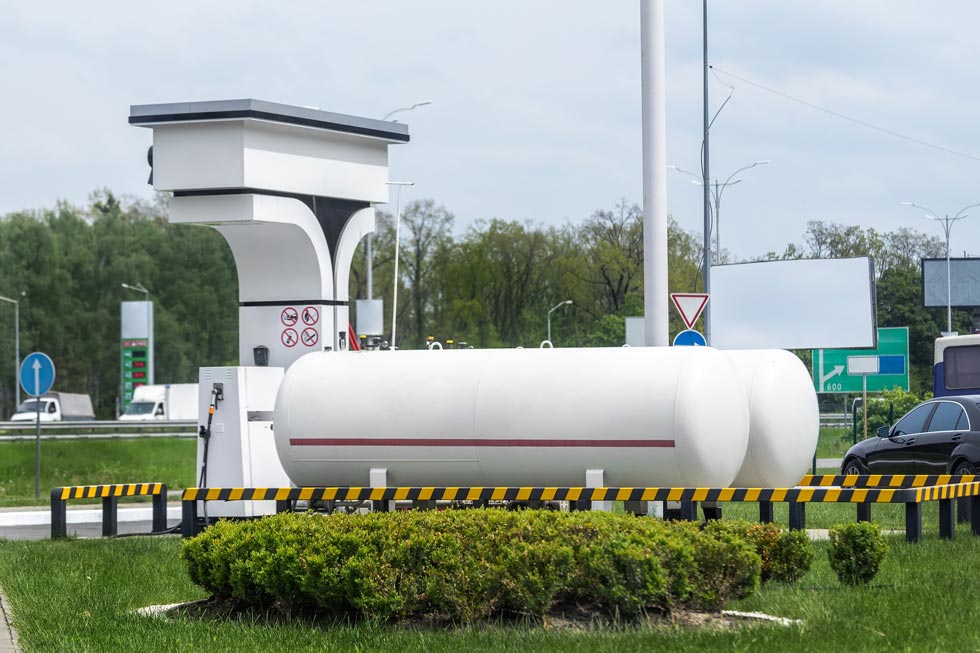
What’s that, you say? You’ve always wondered what makes an autogas dispenser different from the propane dispensing equipment you have used for cylinder filling? The equipment required to fill barbeque cylinders, although similar in many respects, is quite different from the required equipment for dispensing autogas.
In the propane industry, there are many manufacturers of autogas dispensers, and depending on your specific needs, you have plenty of quality dispenser manufacturers to choose from. When making your selection, you will find there are some common components and features found with most dispensers on the market today. Although not intended to be all-encompassing, here is a brief overview of the major components that make up an autogas dispenser.
- Enclosure construction — Depending on the location where the dispenser will be installed, you should consider the materials from which the enclosure is constructed. For instance, an installation near salt water may present a largely corrosive environment and require more robust construction materials, such as stainless steel. A dispenser installed in sunny Arizona may last much longer if the exposed components have UV protection. Proper application and excellent quality are important for dispenser longevity in the harsh elements.
- High differential pump — Although not necessarily located within the dispenser, choosing the proper liquefied petroleum gas (LPG) pump is critical to the dispenser’s performance. Today’s liquid propane vehicle systems require significant differential pressure between the supplied LPG storage tank pressure and the output pressure of the LPG pump. Internal pressures within the fuel delivery system of the vehicle must be overcome to fill the vehicle tank efficiently. It is recommended to reference the vehicle OEM or vehicle LPG fuel system manufacturer recommendations when determining the system differential pressure required for optimum performance. High differential bypass — Paired with the high differential pump, and equally as important to efficient autogas dispensing, is the high differential bypass. Adjustments to the spring compression in the bypass will dictate the amount of differential pressure that a given pump can produce within its performance curve. Differential pressures are typically found to be set between 130 PSI and 150 PSI on most autogas systems that produce an acceptable GPM delivery at the nozzle.
- Dispenser register — The register reports the amount of fuel dispensed, and when dispensing in a retail sales scenario, can display the price per unit and total sale as well. Most registers today are electronic in design and communicate with fuel management equipment using a two-wire system. When connected to fuel management equipment, mechanical registers require a more in-depth wiring configuration that uses relay logic to communicate with and energize system components.
- LPG dispenser meter with temperature-compensated, pulse-output communication — Measuring the volume of LPG being dispensed and communicating this amount accurately to the register in the dispenser is required for the retail sale of autogas. Regardless of the type of meter, from positive displacement to mass flow (Coriolis) technology, a temperature-compensated electronic pulse must be created and sent to the register for the operator’s reference when dispensing. Additionally, most fuel management equipment uses the pulse output signal from the dispenser to monitor and record transaction data.
- Autogas filtration — Choosing the proper LPG filter is critical to the dispenser’s performance, as well as the engine performance of the vehicles being fueled. Removal of contaminants in LPG such as heavy ends and oils is very important when dispensing autogas. Dispensing equipment repairs aside, expensive vehicle fuel delivery system repairs are costly in dollars, as well as time for your customers. Properly installed filtration in conjunction with accurate documentation of filter cleaning and replacement is highly recommended when fueling autogas vehicles.
- Autogas fueling nozzles — Depending on the dispenser you have chosen, you may have one or two fill hoses. Each fill hose will require an autogas nozzle to connect to the vehicle. There are many nozzle types used globally; however in the U.S., there are two primary styles that are most used. The ACME threaded connection, which has been around for some time, and the Euro-style nozzle are both considered to be low-emission equipment. In 2020, the K-15, or Euro “push to connect”-style vehicle-mounted filler valve, was officially adopted as the style that all vehicle manufacturers must provide on their LPG vehicles moving forward per NFPA 58. The 2024 edition of NFPA 58 allows for this Euro-style nozzle to be used without requiring specific operator training in LPG dispensing. Like the gasoline and diesel dispenser, LPG dispenser fueling instructions need only be provided to the fueling public at the dispenser.
- Pull-away protection fill hose — Because the dispenser filling hose is connected to both the dispenser as well as the vehicle, the opportunity for the vehicle to drive off before completely breaking the fueling connection as designed is significant. The pull-away protection device or valve is designed to separate during the pull-away and shut off LPG flow from both sides of the separated valve in the event of a drive off.
- Pull-away protection dispenser — As a portion of the vehicle crash precautions required at today’s autogas fueling sites, the use of a safety coupler is required. The coupler is typically installed between the dispenser piping and the liquid propane supply piping as it meets with the dispenser. The safety coupler is designed to separate during a vehicle collision with the dispenser and shut off LPG flow from both sides of the separated safety coupler.
- Integrated fuel management (in dispenser) — Requiring authorization to dispense fuel is important to most autogas fueling equipment owners. If tracking and reporting your autogas fueling site transaction data is important to you, some manufacturers offer fuel management software that is integrated into their dispenser. This dispenser configuration is a convenient way to monitor and manage your fueling site. Storage tank fuel level monitoring, fuel usage, driver and vehicle information are the most common data to monitor and report. Depending on the dispenser manufacturer you choose, such options as LPG order planning and purchasing can be done automatically.
- Fuel management (site management options) — If your fueling site already has fuel management equipment installed, you may wish to simply integrate your new LPG dispenser into this existing technology. The most common authorization equipment is a pedestal where the operator would present their fueling card or input their ID number. Be it cloud-based or hard line wired to your back office, there are multiple options that can be installed to retrieve the fueling transaction data. Most fuel management equipment requires a pulse signal that is provided by the dispenser. This pulse signal originates from the LPG meter and reflects the volume of LPG being dispensed on any given transaction.
The common components found in today’s autogas dispensers are worth your review and understanding before you purchase. Finding the autogas dispenser that fits the needs of your fueling site today while providing accommodations to help meet your fueling needs down the road is extremely important. Take the time to properly plan and discuss your specific fueling site needs with one of the many qualified autogas dispenser manufacturers in our industry. You will be happy you did!