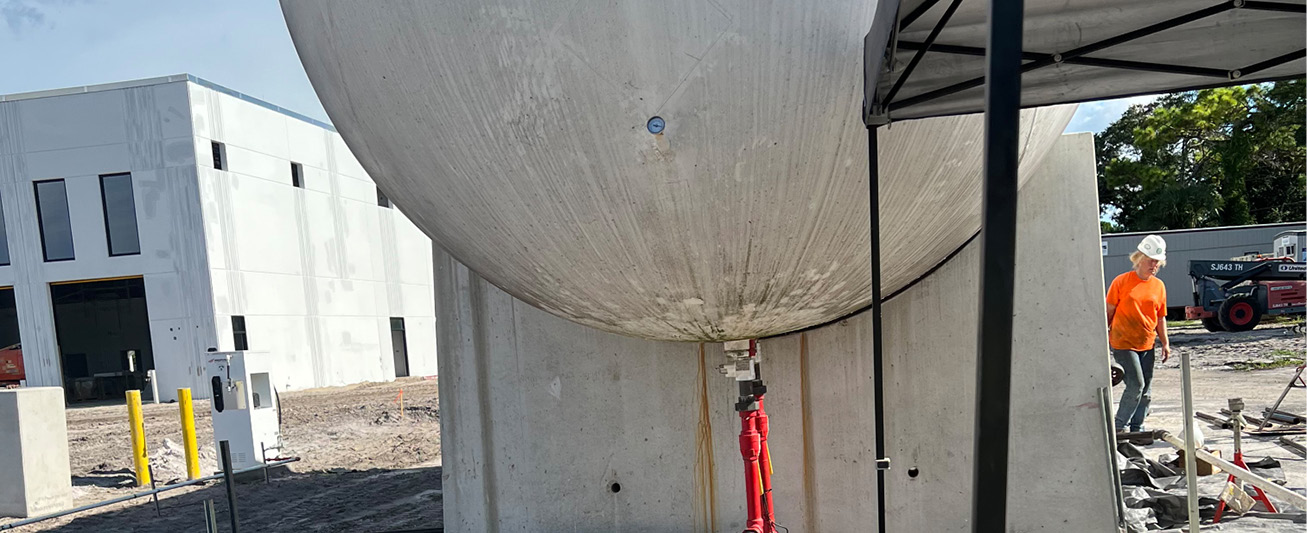
Women are making a direct impact in every area of the propane industry; Charlotte Jones, the manufacturing foreman at Superior Energy Systems, is proof of that. A jack-of-all-trades, Jones often has her hands involved in many projects at the same time, from overseeing essential manufacturing processes to on-site installations of propane autogas systems.
Join BPN on this interview with Jones to learn more about her experience in the industry and her valuable insights into propane autogas manufacturing, among other things.
Please describe your current position at Superior Energy Systems.
I help oversee all manufacturing that is done on-site at Superior Energy Systems (SES) for midstream, standby power and autogas systems. I also prepare the materials needed for our service and installation teams and travel to those jobs as needed.
Please describe your background, your career history and how you ended up in your current position as manufacturing foreman.
I came to Superior Energy Systems from another company where I installed commercial sprinkler systems for fire prevention. I was initially hired at Superior Energy Systems as a pipe fitter, and my job has evolved from there. I have worked my way up to now leading our manufacturing team, which consists of pipe fitters, welders and service technicians. I also travel quite often to various jobs, including storage (midstream) and industrial installations, autogas infrastructure installations and service calls of all sorts.
What are the biggest changes you’ve noticed in the autogas dispenser sector in your 14 years with Superior Energy Systems? Are there any major successes or challenges?
Superior Energy Systems created the first propane autogas dispenser in 2010, right around the time I got my start. I remember thinking what a neat concept autogas was at that point. I think there has always been a challenge to keep pace with the market demands, and we have evolved dramatically in terms of infrastructure technology. We now offer proprietary, web-based fleet management software embedded in our dispensers and top-of-the-line equipment in terms of emissions, safety and reliability. Those changes have made autogas a top choice for fleets when it comes to alternative fuels, which is a major industry success.
Another thing I am proud of was Superior Energy Systems hitting a major milestone of more than 100 million gallons of fuel pumped through its line of PRO-Vend 2000 autogas dispensers [in 2023]. I have had my hands on nearly every one of the 1,600-plus dispensers we have manufactured, and the milestones we are hitting truly make all the hard work feel even more worthwhile.
What is the most rewarding aspect of your role?
I think being able to lead a team that can take some parts and pieces and essentially build something in a matter of days that is going to be a critical part of a business’ success is very rewarding. Propane is such a versatile fuel and having the ability to take engineering drawings and create infrastructure that uses propane in so many ways keeps my energy going. The autogas side is fairly systematic since we are usually building to the same spec depending on the type of dispenser; but even then, we have fleets that need specific nozzles or even different languages for units going outside of the U.S. For midstream and industrial standby power jobs, nearly every job is designed and built to order and specified to the customer’s needs and uses. We pride ourselves on the ability to do that and simultaneously create high-quality, safe and user-friendly products.
What are the biggest internal and/or external challenges you and your team are currently facing?
Labor shortages are a challenge, but SES has been lucky to have dedicated staff, most of whom have been with the company for over 10 years who are great to work with, but we could always use more of those folks. At times, it can feel like I have 10 balls I am juggling, but I also think that challenge keeps me going. I would rather be juggling manufacturing and installs than sitting still, waiting for the next job to come.
Are there any upcoming regulations that will be impacting autogas dispensers soon?
Weights and measurements. Canadian Standards Association (CSA) and Underwriters Laboratories (UL) requirements are constantly changing, and we have an engineer on staff who is tasked with the challenge of keeping up with those changes. One of my main responsibilities is confirming that all new parts coming into the shop to be assembled meet or exceed those code requirements, as well as the parts we manufacture ourselves.
How do you effectively adapt your team and manufacturing processes to shifting safety regulations?
Superior Energy Systems has always made safety a top priority when it comes to product manufacturing and installations. Our leadership feels so strongly about this that we have a vice president of safety, Mike Walters, on staff. I communicate with Mike weekly on safety regulations and changes, and he ensures our manufacturing team has all the necessary training they need regarding industry safety. I feel completely capable, safety-wise, whether I am in our manufacturing facility or on-site at an installation and am thankful the company prioritizes a safety-first culture in everything we do.
How would you define your approach to leadership? What is your vision of an ideal leader, specifically in a manufacturing context?
I would say my leadership style is task-oriented or direct. I believe in setting clear goals and encouraging those around me through hands-on learning. What we do at Superior Energy Systems is not as easy as looking at a piece of paper and putting the same parts together every time, which can be challenging. I set high expectations — not only for my team, but for myself, which I think also encourages my team to do their best every time for every job.
What is one thing you wish propane marketers knew about the behind- the-scenes of manufacturing?
Our supply chain is always the hardest part of manufacturing. Working with many suppliers with varying lead times is a challenge. It is a constant balance to meet customer expectations with lead times and give ourselves a safety net for delays. We have a lot of very patient and understanding customers, and we really appreciate their support and trust.
How do you prioritize a healthy company culture in a setting that often requires efficient workflow to meet strict deadlines?
My generation was taught to work as hard as we can for as long as we can. The younger generation coming into the workforce has a different outlook on prioritizing mental health and their personal time, which has somewhat shifted my mindset. I now work more to prioritize those values and encourage my team to make sure they are doing what they need to do to be the best version of themselves, which is not always easy when you work on such tight timelines. We often pick up the slack for our teammates who are away, which I think creates a culture of positive teamwork.
If someone were just entering your current role, what piece of advice would you give to them as they start this new position?
I would say be patient and learn as much as you can. I came into this industry hardly knowing the different uses of propane. With encouragement from leadership, I dove in headfirst to learning; it allowed me to get hands-on experience quickly, which has helped me move up at Superior Energy Systems. I would also say don’t be afraid to start at the bottom. So many of our staff here started just like me, filling bottles or fitting pipes, and while that doesn’t seem exciting at the time, it opened a lot of doors for me. Patience and perseverance with a positive attitude can take you far in life.