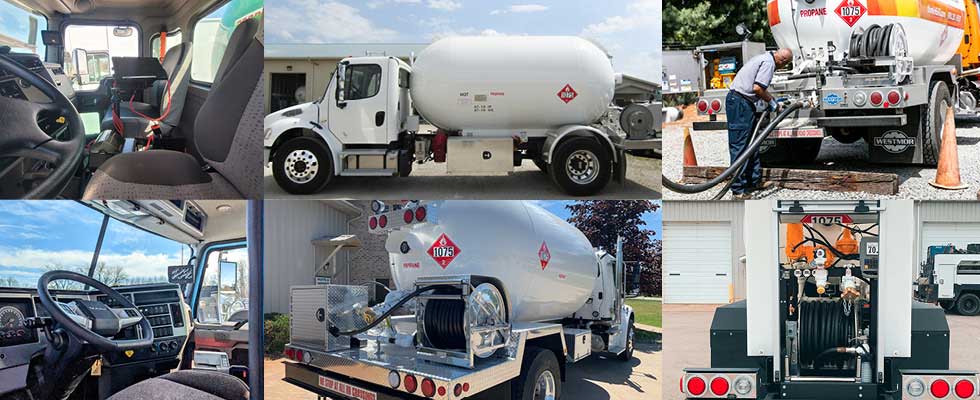
The significance of the bobtail in the propane industry can’t be ignored. Each time a bobtail driver heads out on a delivery route, your company’s dependability is on display. It’s therefore of utmost importance to get the best use out of your bobtails, focus on necessary maintenance investments and keep an eye on the latest features that can improve your drivers’ time on the road.
Ahead, learn more about these topics from Mike VanDenBoom, president of Signature Truck Systems; Joey Runnels, vice president of Mississippi Tank Company; Jerry Jones, vice president of Pacific Truck Tank Inc.; Marla Verlinde, propane division sales & marketing for Arrow Tank & Engineering; Brady Griffith, regional sales manager — northwest region for Westmor Industries; and Rob Vandemark, vice president of IPS Equipment Inc.
What is your advice for maximizing the use of bobtails?
Runnels: Utilize a good GPS routing system with tank monitoring, and maintain the complete system, grease, pump and bypass pressure settings.
VanDenBoom: Tank monitoring takes away guesswork. A good routing system is important. Split shift drivers and use part-time drivers during the heavy delivery season.
Jones: Take advantage of technology, such as an electronic logging device or tablet computer in the truck cab to collect comprehensive data that can be used to reduce overall costs and support drivers. The device facilitates communication between drivers and dispatchers and allows for route efficiency and a reduction of fuel costs and drivers’ time in the field. The device can also be set to monitor the health of a vehicle and alert fleet managers when repairs or maintenance are needed. Also, the data can be used to make fleet decisions, such as whether a vehicle requires more maintenance or if a new vehicle should be considered.
What’s the No. 1 maintenance tip most fleet managers forget?
Runnels: Clean the meter strainer.
Verlinde: Go to the truck wash! Washing trucks is the best value any company can bring to their fleet. We use a one-piece stainless steel deck with integrated platform-style fenders. This design uses the best material and coverage to protect and maintain the appearance of the bobtail. However, the truck chassis frame and many undercarriage components are made of materials that are vulnerable to deteriorating quickly from chloride road deicers, so routine washes are critical. It’s also important to involve drivers in new truck purchases. By involving them in the process, they will be more likely to treat the truck like their own. After performing a thorough orientation with the drivers, operators are appreciative when seeing the completed unit for the first time, and managers report they take more pride in their work.
Griffith: Check your tie-down bolts!
Vandemark: A maintenance issue we see is lack of grease in the power take-off (PTO) shaft and product pump. This must be properly maintained to pump proficiently. Applying a little grease to the PTO shaft and pump can keep it working smoothly. Contact your bobtail builder or product pump manufacturer for proper ways to grease the pump and PTO shaft each time you perform preventative maintenance. Failure to do this can result in damage and possible issues while delivering gas to your best customers.
What new features are making jobs easier?
VanDenBoom: The new Kenworth chassis has a lower profile and easier entry and exit.
Jones: Vehicle cameras and sensors are helping our customers. It is now common for a vehicle to include a dual camera on the windshield that records the front of the vehicle and inside the cab; plus, there’s a backup camera with sensors at the rear to aid the driver. The 5-minute idle shutdown timer saves fuel by preventing a vehicle from idling for long periods. We also use a valve in the pumping system that drops the unit into cylinder mode when filling smaller tanks to lower the pressure on the system. For safety, we use proximity sensors to detect metal and stop the truck from moving until the nozzle or other equipment is properly stowed.
Griffith: The Ergoload Deck design places the spray-fill and vapor-return lines approximately 20 inches lower than traditional fill heights. Drivers load more ergonomically when they fill their bobtail, keeping the heavy hoses waist-high versus lifting it over their shoulder. The swiveling hose reel on the Pathway Delivery System allows drivers to select the path that works best for their propane delivery while providing a safe, ergonomic driver experience. Just turn the reel to the angle that works best, lock the reel into place and pull the hose in the direction of the tank you’re delivering to.
Vandemark: Our Clear Vision Enclosure design allows the driver greater vision when backing up. With the benefits of covering the meter, hose reel and piping while being lightweight and durable, the driver has clear vision backing into tight spots. As the driver pulls the delivery hose out and rewinds it back onto the reel, the hose reel chain will start to stretch over time. For easy maintenance, the driver can remove a few bolts and roll the cabinet back to gain access to the hose reel, as well as valves and fittings behind the meter. With the Clear Vision Enclosure rolled back, the driver can stand next to the hose reel motor and make the necessary adjustments. When done, roll the cabinet back and tighten into position.