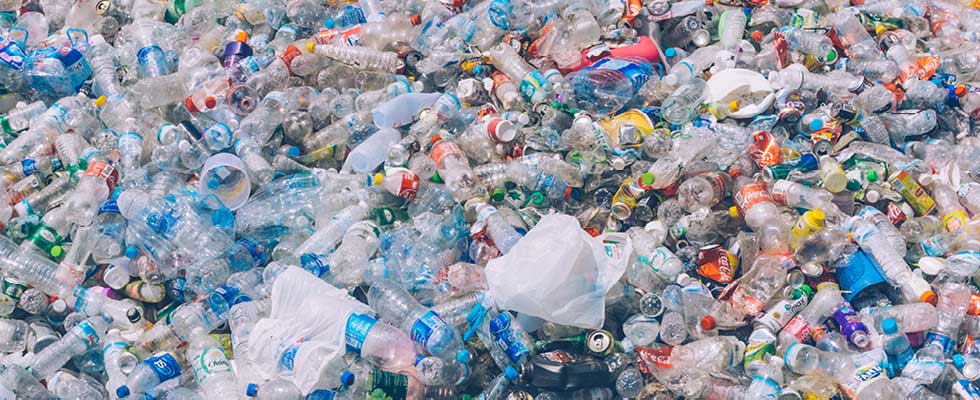
Waste from polyethylene (PE) and polypropylene (PP), the two most produced polymers globally, accounts for approximately half of the 5 billion tons of plastic that have been landfilled or leaked into the environment since the 1950s.1 Today, only 12% of all plastic is mechanically recycled.2 Several bottlenecks lead to such a low recycling percentage. For example, plastic waste has to be separated and cleaned to remove post-consumer debris prior to mechanical recycling, but material recovery facilities still rely heavily on manual sorting, which limits high-volume processing.3 Further, polymers are often chemically blended with additives that cannot be separated by physical methods, making some mechanical processing — such as shredding — more challenging.
Still, even with better sorting technologies, each round of mechanical recycling progressively degrades the functional properties of the plastic, inevitably leading to downcycling and eventual landfilling.4 Alternatively, polymers could be broken down at the molecular level, a process called chemical recycling. This would be a game changer for the plastic industry, as it can unlock ways to process unsorted and dirty plastic mixtures into building blocks that can be repolymerized into the original plastic an infinite number of times with no loss in quality. This could result in savings up to US$176 billion per year, equivalent to 3.5 billion barrels of oil — thereby sparking a global effort both in industry and academia to turn the vision of chemical recycling into reality.4-5
Today, among the different strategies reported for the chemical recycling of polyolefins, hydrogenolysis shows great promise. Hydrogenolysis is a type of chemical reaction that utilizes hydrogen gas (H2) to break the bonds in the polymer chain, generating shorter hydrocarbons at mild temperatures (less than or equal to 300 C) in the presence of a catalyst (i.e., a material that accelerates a chemical reaction without being consumed by it).
While an active catalyst almost always leads to the total conversion of the starting polymer, the random cleavage of the polymer chain results in product mixtures comprising hydrocarbons ranging from heavy paraffins to methane.6-8 While promising, this product mixture could translate into considerable separation costs or in low returns, due to the low value of methane.
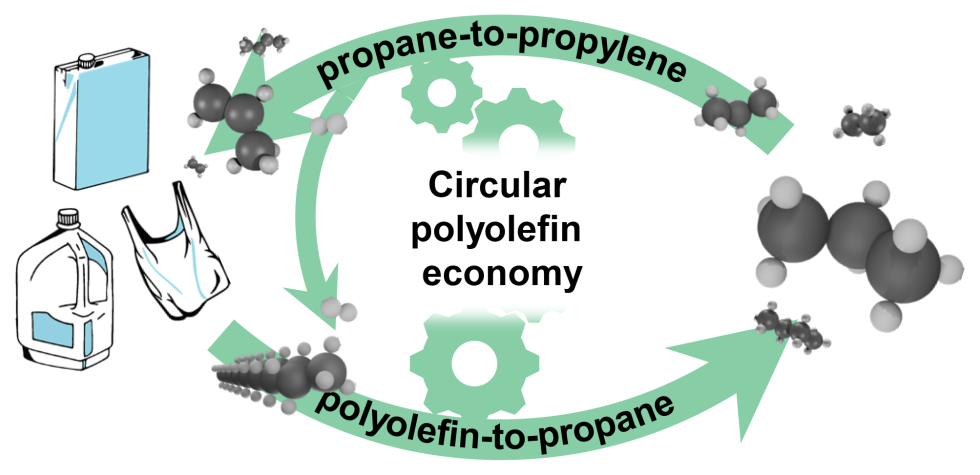
Now, we have demonstrated a new process to convert both single or mixed streams of PE and PP almost exclusively into propane gas. The carbon efficiencies of this process exceed 80%, with the rest being useful ethane and butane.8 Propane is a desirable product on its own, but also has the potential to be turned back into virgin plastic by first undergoing dehydrogenation to propylene monomer via commercial processes. In addition, the H2 generated from the dehydrogenation step could be fed back to a polyolefin recycling unit, which allows for the reutilization of all the carbon and hydrogen atoms for a circular polyolefin economy (see Figure 1).
The catalyst we developed was composed of two ingredients: cobalt and a microporous aluminosilicate material called a zeolite. Both components work together in the presence of hydrogen to activate the polyethylene and selectively cut it into blocks of three carbon atoms to form propane. While the mechanism of how this combination works is still under investigation, the highly selective behavior likely originates from the cooperation between the pores in the zeolite, which control where the long polyolefin chains should react, and the cobalt nanoparticles, which activate hydrogen and keep the zeolite from deactivating.8
For this technology to be used in larger scales, several questions need to be answered first. For instance, it is not yet known what impact contaminants in the feedstock have on the performance and stability of the catalyst. PE and PP are made of carbon and hydrogen exclusively, while other plastics like polyvinyl chloride (PVC), commonly found in mixed polyolefin waste, contain elements like chlorine that are likely to degrade the catalyst.
With this scope, we are collaborating with the National Renewable Energy Laboratory to conduct in-depth analyses to assess the technoeconomic feasibility of a chemical plant using this technology to process 10 tons/hour of polyolefin waste; we are also performing tests in our laboratory to assess the impact of contaminants and scale up this process. These efforts are conducted in the frame of the Bio-Optimized Technologies to keep Thermoplastics out of Landfills and the Environment (BOTTLE™) consortium, a DOE-funded conglomerate of universities and National Laboratories across the U.S. that is developing new chemical upcycling strategies for today’s plastics and redesigning tomorrow’s plastics to be recyclable-by-design.
All in all, while we believe that hydrogenolysis technologies are promising, they represent only a part of the solution. Solving the plastic waste challenge is a colossal endeavor requiring not only the development and implementation of an array of technologies that can process different plastics into different products, but also substantial financial investments and targeted policies at a national and international level.
Guido Zichittella,1 Julie E. Rorrer,1,2 Yuriy Román-Leshkov1
1Department of Chemical Engineering, Massachusetts Institute of Technology, Cambridge, Massachusetts 02139, United States
2Department of Chemical Engineering, University of Washington, Seattle, Washington 98195, United States
References
- Geyer, R.; Jambeck, J. R.; Law, K. L., Production, Use, and Fate of All Plastics Ever Made. Sci. Adv. 2017, 3, e1700782.
- Martín, A. J.; Mondelli, C.; Jaydev, S. D.; Pérez-Ramírez, J., Catalytic Processing of Plastic Waste on the Rise. Chem 2021, 7, 1487-1533.
- Lubongo, C.; Alexandridis, P., Assessment of Performance and Challenges in Use of Commercial Automated Sorting Technology for Plastic Waste. Recycling 2022, 7, 11-37.
- Rahimi, A.; García, J. M., Chemical Recycling of Waste Plastics for New Materials Production. Nat. Rev. Chem. 2017, 1, 0046.
- Vollmer, I.; Jenks, M. J. F.; Roelands, M. C. P.; White, R. J.; van Harmelen, T.; de Wild, P.; van der Laan, G. P.; Meirer, F.; Keurentjes, J. T. F.; Weckhuysen, B. M., Beyond Mechanical Recycling: Giving New Life to Plastic Waste. Angew. Chem. Int. Ed. 2020, 59, 15402-15423.
- Rorrer, J. E.; Troyano-Valls, C.; Beckham, G. T.; Román-Leshkov, Y., Hydrogenolysis of Polypropylene and Mixed Polyolefin Plastic Waste over Ru/C to Produce Liquid Alkanes. ACS Sustain. Chem. Eng. 2021, 9, 11661-11666.
- Celik, G.; Kennedy, R. M.; Hackler, R. A.; Ferrandon, M.; Tennakoon, A.; Patnaik, S.; LaPointe, A. M.; Ammal, S. C.; Heyden, A.; Perras, F. A.; Pruski, M.; Scott, S. L.; Poeppelmeier, K. R.; Sadow, A. D.; Delferro, M., Upcycling Single-Use Polyethylene into High-Quality Liquid Products. ACS Cent. Sci. 2019, 5, 1795-1803.
- Zichittella, G.; Ebrahim, A. M.; Zhu, J.; Brenner, A. E.; Drake, G.; Beckham, G. T.; Bare, S. R.; Rorrer, J. E.; Roman-Leshkov, Y., Hydrogenolysis of Polyethylene and Polypropylene into Propane over Cobalt-Based Catalysts. JACS Au 2022, 2, 2259-2268.