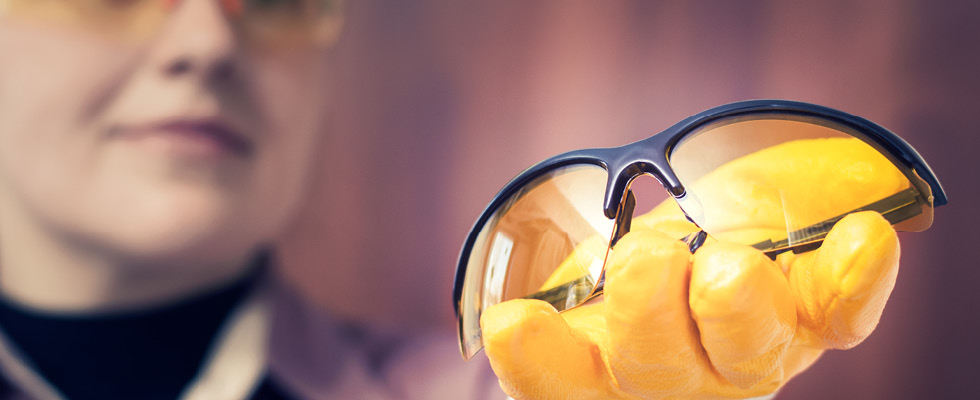
In a recent report from management consulting company J. J. Keller & Associates, 90% of respondents surveyed stated they have trouble getting their employees to wear personal protective equipment (PPE). The “PPE Pain Points Study” was distributed to over 12,000 contacts in a variety of industries.
Most survey respondents (89%) stated they were responsible for purchasing PPE and work for companies with less than 500 employees. With the hazardous environments propane employees are working in on a daily basis, proper and comprehensive use of PPE is paramount.
Among the open-ended comments from respondents, finding comfortable PPE for employees emerged as a common theme as well, with responses indicating the PPE needs to be comfortable enough for employees to wear all day.
Below, hear from the following experts at J. J. Keller & Associates about key report findings, how to improve proper use of PPE in your company and more:
- Robin Marth, EHS editor
- Stephanie Hallman, director of marketing
- Tom Bray, senior industry business advisor
To read the full report, visit jjkeller.com/ppepainpoints.
Can you discuss some of the key findings from the study?
Marth: When we fielded the PPE pain points study, we knew that many employers have a difficult time getting their employees to wear PPE. But what we were surprised to learn is the extremely large percentage — 90% of respondents said they have trouble getting their employees to wear their PPE. Other key study findings were:
- 34% said they had trouble buying PPE in the sizes they need
- 35% struggle to purchase PPE that fits their female employees
- 71% said they often or sometimes experienced supply chain delays in the past year
In addition to sizing and supply chain concerns, heat rose to the top as a PPE issue. Wearing PPE is necessary, of course, to keep workers safe. In extreme heat, however, the PPE itself can add to the risk of increased heat exposure.
How does J. J. Keller advise its clients to encourage PPE use on the job? Are there any strategies or incentives that your team has seen work well?
Marth: Common excuses given in the survey for not wearing proper PPE included “just didn’t want to wear it” and “didn’t think it was necessary,” suggesting employees know they are supposed to wear PPE but choose not to. Employers need to get their employees to think about their reasons for choosing noncompliance and the potential consequences. If employees don’t want to wear PPE or don’t think it’s necessary, they’re choosing to accept the risk of not wearing it. However, employees don’t have the authority to make that choice. The employer requires PPE not only because it prevents injuries, but because federal regulations require the employer to provide PPE and enforce its use.
To encourage the right choice, employers might want to try one or more of the following approaches:
- Impact on others — Point out that an injury has consequences for more than just the employee. It impacts the employee’s family, the company itself and their coworkers.
- Risk and reward — Ask the employee to consider the potential injuries that can result from risky behavior and ask them to think of the life-changing impacts they may experience, such as losing an eye or permanent hearing loss. Wearing PPE may seem like a hassle, but the potential consequences of noncompliance will be far worse.
- Address the objection — Have the employee explain why they don’t wear PPE, such as comfort, fit, etc. Employers can often offer alternatives to mitigate or reduce those problems.
Do you expect supply chain challenges to subside in the coming year or become more plentiful? How should marketers plan to ensure their teams have the adequate PPE on the job?
Hallman: At J. J. Keller, we have started to get glimpses of light within our supply chain. So at this time we don’t anticipate that supply chain challenges will increase — yet we’re not expecting a complete return to “normal” in 2023.
We continue to encourage those looking for PPE to work closely with their preferred PPE supplier to ensure the supplier understands what your needs are and what you expect them to be near term and longer term. If you have seasonal requirements, for example, start the conversation with your supplier now about your spring/summer 2023 needs.
Are there any PPE items that have been harder to get than others?
Hallman: Certainly items that are produced internationally experience delays. At J. J. Keller, we’ve diversified our sources so we have multiple ways to pinch-hit if any one supply chain source is delayed. This has helped to offset ongoing challenges.
In industries like propane where diversity is already a challenge, how do you advise clients to navigate a lack of access to properly fitting PPE for their employees?
Marth: Employers need to shift their mindset from offering universal fit and the generalities of small, medium and large as it relates to their female employees. By staying complacent, the employer risks exposing their female employees to additional hazards due to ill-fitting PPE.
A lack of access is a result of lack of planning. So, determine if a problem currently exists. Discuss with female employees the PPE issues they are experiencing and the best ways to mitigate those issues. Review injury and near miss reports for trends regarding PPE usage. And look for suppliers that offer PPE specifically sized for females.
What are some of the most common Department of Transportation (DOT) and Occupational Safety & Health Administration (OSHA) PPE violations that J. J. Keller observes?
Marth: The National Safety Council unveiled their newest list of “Top 10 Most Frequently Cited Standards” from OSHA for fiscal year 2022, and once again, PPE noncompliance was listed multiple times. Keep in mind, these are only violations that OSHA cited; they are not representative of the (obvious) bigger picture of potential violations and PPE noncompliance!
- No. 1: Fall Protection, general requirements — 5,260 violations
- No. 3: Respiratory Protection, general industry — 2,185 violations
- No. 9: Eye and Face Protection, construction — 1,401 violations
Bray: Regarding the DOT, drivers are still subject to PPE requirements when they are at a manufacturing, loading or unloading facility, jobsite, etc. In those cases, the violations are going to be based on the facilities requirements. The most common driver violations I have encountered in those areas include:
- Not wearing a hard hat (helmet) in an area with overhead hazards
- Not wearing safety glasses when required
- Not wearing close-toed or steel-toed shoes in areas where they are required (Drivers normally aren’t allowed into areas that would require steel toes, but sometimes they are.)
- Not using fall protection when it is available at a facility (unique to flatbed and tanker drivers)
- Not wearing the proper PPE when handling hazardous material
As far as direct DOT requirements, the most common PPE violation involves a carrier sending its drivers to work on the roadway or the road right-of-way without having or using high-visibility clothing, which is a violation of a Federal Highway Administration (FHWA) regulation. Many carriers simply are not aware of the FHWA requirement, and some just don’t enforce it.
One issue here is that most drivers are not assigned to work on the roadway (the facilities where they pick up and deliver to are normally off the roadway).
However, if the driver needs to “tailgate” a load at the roadside (unload on the side of the road), make deliveries while parked on the road, etc., you are assigning the driver to work on the roadway, and the high-visibility regulation would apply.
Are there any important PPE-related training opportunities that business owners often overlook?
Marth: Employers are required to train their employees on the following:
- When PPE is necessary
- What PPE is necessary
- How to properly don, doff, adjust and wear PPE
- The limitations of PPE
- The proper care, maintenance, useful life and disposal of PPE
They also must ensure the employee has an understanding and ability to use the PPE, and they must retrain the employee if they are seen wearing the PPE incorrectly or not at all.
Effective training is crucial for PPE compliance. This can often include a mixture of lecture, hands-on demonstration, video, microlearning, five-minute talks, handouts and knowledge assessments. Not everyone learns the same way, so it’s imperative to have a variety of learning techniques to reach your audience.
As an example, J. J. Keller Safety Management Suite offers a wide variety of training options related to PPE in several different circumstances, including electrical safety for construction PPE, fall protection for general industry PPE, hand and foot protection essentials, eye and face protection — just to name a few.