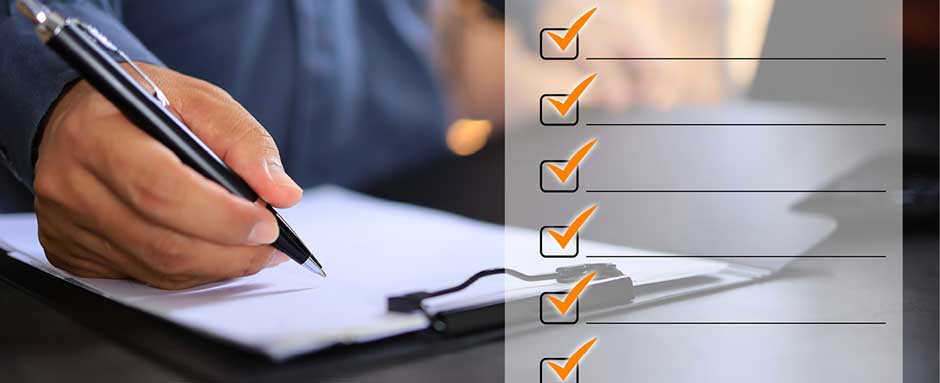
Propane marketers have a lot of responsibilities to balance, with one of the most important being to meet each applicable regulatory compliance requirement. This requires you to provide your team members with the proper tools and training needed to stay safe on the job and meet local and federal safety thresholds.
So, what’s the best strategy to meet these requirements and document your compliance? Conducting regular safety meetings is the first step. In this article, we’ll dive into everything you need to know about how to start your safety meeting process. We’ll discuss the recommended frequency for safety meetings, how to prepare for what topics you’ll cover at each one, important metrics to track, vital follow-ups to perform and methods for securely documenting everything for your insurance underwriter and your personal records.
Recommended Frequency for Propane Safety Meetings
How often should you conduct propane safety meetings within your propane company? The answer will vary based on your company’s policies and procedures manual, but most propane safety experts recommend that you strive to conduct propane safety meetings on a monthly basis. They usually recommend holding safety meetings whenever your internal safety manuals are updated or modified.
Keep in mind that the more frequently you meet with your team, the more solidified your safety processes will be in their mindsets and routines. You may find that meeting more than once a month with your team will work better for your company.
How to Plan Out Your Safety Meeting Topics
Create a calendar and fill in the topics ahead of time. Preparing your safety meeting topics is the key to success — after all, if you have a completed calendar of which topics you will be discussing and when, you’ll minimize the number of barriers that get in the way of hosting your safety meetings. When it comes to organizing your safety meeting topics, these are suggestions to keep in mind:
- Determine topics seasonally based on which subjects are most relevant.
- Focus your safety meetings on any approaching refresher training.
- Review initial training topics with your team when you are onboarding a new employee.
- If there is a safety incident or priority follow-up, use it as a teaching opportunity for your team.
When to Host Safety Meetings
When planning your weekly or monthly safety meeting time slot, consider when will be most efficient and convenient for your safety leadership staff and your employees. For example, holding one first thing in the morning before your drivers have left for their delivery routes might end up working best for everyone.
You should host safety meetings at a time during the week when everyone is available — whether that be in person, remotely or a hybrid of the two.
A hybrid opportunity means that more staff may be able to attend; it is also helpful to be able to record meetings and distribute them afterward. This will simplify follow-ups with team members who are away or on vacation, allowing them to be able to receive the material covered in the safety meeting.
If most of your team is available midday, consider the option of catering a monthly lunch and hosting your safety meeting during that time. You’ll have the opportunity to convey essential safety information while developing team rapport and promoting employee retention at the same time.
How to Start Planning Your Safety Meetings
By now, some safety meeting topics may have come to mind, and you may have begun considering what time during the week would be a good fit for your safety meeting. So, how do you start implementing your plans? Here are some tips that have historically worked for our propane marketer clients:
- Plan out your safety meeting calendar for the next six to 12 months. You can use this as a baseline in future years, so your planning will be even easier from here on out.
- Collect and evaluate various training materials for each meeting. Your company’s policies and procedures manual should align with your training subject, so include that language and those details in your safety meeting’s agenda.
- Incorporate Certified Employee Training Program (CETP) training materials along with NFPA 54 and NFPA 58 regulations.
- Document your safety meeting training and perform follow-ups using the tips in the remainder of this article.
How to Document Your Safety Meetings
You know the old saying — if it isn’t documented, it didn’t happen. Be diligent about documenting your safety meetings; include important details, such as when the meeting took place, what was covered, which safety materials and/or policies and procedures were discussed, and who attended the meeting.
Save this document in an organized location with your other safety meeting documentation so it will be handy if you ever need it. The documentation won’t protect you from liability and risk if you can’t find it down the road.
The Important Metrics & Follow-Ups
Imagine yourself in this situation: You’re hosting regular safety meetings, your team is receiving the information enthusiastically and applying it daily, and you’re documenting the meetings securely.
But then you face a catastrophic incident where one employee makes a critical error. You ask your team how this happened and discover that the employee in question was on parental leave during the safety meeting in which you discussed the topic at hand. The last time they received the relevant information was at their orientation, and their refresher training wasn’t due for another month.
Without tracking safety meeting attendance and following up with anyone who missed it, you’re leaving yourself open to the enormous risk of bodily harm and legal litigation.
Fortunately, this can be solved by keeping tabs on who attended the safety meeting and diligently following up with anyone who wasn’t there. Sharing the information with all employees — regardless of whether they were out sick or on vacation during the meeting in question — is your best bet to ensure your company is putting your employees’ and company’s safety at the forefront.
Make Things Easier for Yourself & Your Team
It’s natural for us to push things off that we don’t feel are convenient. If safety meetings are a huge hassle to plan and implement, you may find yourself putting less effort or time into them than they deserve, even if you understand how important they are to your safety program.
It’s a wise decision to make things easier for yourself by working with an external safety provider who can provide you with safety meeting topics and materials to cover each month.
That’s right — there are third parties who can organize your topics and provide all necessary materials on a monthly or annual basis to help ensure that you are covered without having to dedicate hours of your monthly schedule to the project or worry about missing something important.
In addition to using the monthly safety materials to meet with your team, you can use them to quiz team members individually, giving you the chance to see where additional training is needed.
It will also reveal where you’re doing a great job and help you determine what to keep in your training regimen as it evolves over time. When planning future years’ safety meeting calendars, you or your third-party provider can incorporate any topics that didn’t fit into your calendar from the previous year, along with identified areas needing improvement.
Allow Safety to Become a Habit at Your Company
Safety training doesn’t end with initial onboarding training or CETP certification. Rather, regular safety training and meetings with your team are critical to maintain compliance with the Department of Transportation, the Occupational Safety and Health Administration and state regulatory requirements.
It sounds like a lot, but if you follow the steps listed above, you’ll be on the right path to implementing regular safety meetings that keep your propane customers, employees and company safe long term.