Thursday, September 15, 2016
Many safety managers and trainers in the propane industry agree that in today’s environment of litigation and heavy regulation, propane marketers have increased their focus on keeping employees properly trained in the latest aspects of propane safety. But some say it must go further than that — propane companies should develop a culture of safety within their organizations.
Jay Hilliard, safety and operations director for Revere Gas Inc. (Hartfield, Va.), said he is seeing more companies move toward a culture of safety, which he noted can yield great benefits.
“Employees realize the decisions they make on a daily basis are vital to reducing their potential exposure to incidents and accidents,” Hilliard explained. “They learn that their safety is their responsibility and requires them to be focused on the task at hand.”
The culture of safety is the result of recognizing additional safety requirements in the propane industry, including the increasing regulations that marketers must follow. In addition to standards such as NFPA 58, Environmental Protection Agency rules, and U.S. Department of Transportation (DOT) regulations, propane marketers sometimes give less attention to U.S. Occupational Safety and Health Administration (OSHA) standards. Dave Latourell, director of safety and transportation for Paraco Gas (Rye Brook, N.Y.), said employees often take OSHA regulations for granted.
“They’re familiar with fire extinguishers, safety data sheets, signage, and ladder use,” Latourell clarified. “It’s around them, but they don’t recognize there are a lot of codes and standards to go with it. It kind of gets overshadowed in our industry because everyone focuses on the propane part of it. People forget the OSHA standards, which primarily say you’ve got to train your employees, and that then loops us back into DOT requirements. But it’s actually OSHA that’s holding [our] feet to the fire for getting all that stuff done for making sure the employees are safe.”
Dan Waters, owner/trainer for Premier Safety Services (Greenville, S.C.), mentioned OSHA’s recent global harmonization system marking requirements for propane containers as a safety mandate that marketers must face. OSHA has adopted new hazardous chemical labeling requirements as a part of its recent revision of the Hazard Communication Standard, 29 CFR 1910.1200 (HCS), bringing it into alignment with the United Nations’ Globally Harmonized System of Classification and Labeling of Chemicals (GHS). The new system “is causing people a lot of grief,” said Waters, whose company assists propane companies with fewer than 100 employees in complying with DOT and OSHA regulations. The company also conducts Certified Employee Training Program (CETP) training. He noted that marketers are having to buy new labels and throw out old ones. And because of the name change from Material Safety Data Sheet (MSDS) to Safety Data Sheet (SDS), marketers must replace their MSDS digital files with SDS files.
Members of the propane industry whose jobs focus heavily in the area of propane safety note that they see various issues in how safety concerns contribute to a culture of safety.
Educating Customers on the Safety Culture
Benny Gay of ThompsonGas (Frederick, Md.) notes a continuing trend of consumers purchasing space heaters and other equipment from big-box stores and trying to install them on their own.
“They either don’t know of requirements that only qualified personnel perform propane work, or they ignore the requirements, including a leak check following an interruption of service — so they don’t comply with any of the above,” Gay said. “If there’s an incident later, the propane marketer is actually placed at risk, because even though incidents like that were beyond his or her knowledge, if anything pops up in the way of litigation, fingers can be pointed toward the propane marketer. We can’t be responsible for what some consumer takes upon himself in his own home.” He pointed out that the Propane Education & Research Council’s (PERC) duty to warn materials inform residents to call a professional installer rather than install equipment themselves.
Gay added that legislation in Alabama prohibits anyone other than a licensed professional to perform propane-related work. “Those laws may exist in other states, but that’s just an example of one of the states we operate in that has that kind of legislation available to protect the consumer but ultimately the propane marketer as well.” He added that ThompsonGas doesn’t sell appliances that it does not install. The company doesn’t sell over-the-counter parts and will not offer advice about installing appliances. He likened those questions to someone asking a surgeon over the phone how to perform surgery.
“Everyone is money-conscious. That’s what the do-it-yourself trend is all about,” he explained. “We’re by no means opposed to that, but there are some things you just don’t fool around with. Obviously propane is one of them.”
Latourell of Paraco Gas responded that the company teaches employees to avoid risks, and it makes the same effort with customers. He has seen more scenarios in which customers with no gas grill hookups at their homes buy gas grills and want to hook them up themselves.
“We teach our customers when it comes to propane, leave it to the professionals. Give us a call. We accentuate that it should be done by someone qualified. The more they realize when it comes to gas you really need a professional involved, the more they realize the motivation for us is customer safety. Educating our customers is critical to them making the right decision when it comes to gas and calling the professional.”
Culture of Safety Meetings
According to Gay, ThompsonGas has always believed in the culture of safety, and that means stressing the importance of employee safety through monthly safety meetings. The company uses the meetings and the safety material used at the meetings “as a true training tool.” In addition to PERC materials, Gay and his team use additional materials from ThompsonGas’ suppliers and insurance carrier, covering subject matter such as components of a propane system; defensive driving; slips, trips, and falls; electrical safety; and ladders.
Hilliard provided an example in which Revere Gas’ safety committee addressed employees’ personal safety. The committee evaluated several areas of risk to its employees, including entering and exiting the back of its flatbed trucks. The committee came up with a plan to modify them for improved safety. The company installed ladders and grab rails, which provide safer access and minimize the chance of an employee slipping and falling.
“Safety meetings and the safety committee gets you thinking beyond just avoidance, but how to eliminate the hazard,” Hilliard explained. “When you get employees thinking like that, safety becomes part of their everyday life.”
Buy-in from employees on company safety programs is key, Hilliard added. “They’re the ones out every day doing the work, the ones you rely on to make good solid decisions about keeping themselves out of harm’s way and at the same time getting the job done that they’re there to accomplish.” To get that buy-in, management must have an open-door policy, take their concerns seriously, and bring up the concerns at safety meetings, he stated. When employees feel like their input matters, they tend to speak up more and make management aware of other possibly unsafe conditions.
For example, if propane service techs are working on a job on the roof of a building and don’t feel safe, management should consider letting a professional roofer do the work rather than propane techs who are less experienced with roof work, Hilliard stressed. “If it’s outside what they typically do, it has the potential to carry more risk. We encourage employees to come to us when they see things they feel could be done better or safer or, at a minimum, that they feel needs to be looked at.”
Terminology: Leak Check vs. Pressure Test
Latourell believes that propane industry members should remember to use terminology properly. That includes knowing the difference between a leak check and a pressure test. “For years, the terms pressure test and leak check have been interlaced. They’re not the same thing,” he warned, adding that although the service tech might perform the correct test, if he does not document it correctly, he is leaving an opening for liability and potential litigation. Misuse of terminology can change the entire context of a code or concept, he noted, and that can be as simple as missing punctuation.
“I have two English teachers for parents,” he explained. “In a day and age where it’s OK to misspell everything with texting and typing finger to iPhone, you can really change what you accomplish if you’re not being careful with what you’re inputting or documenting.”
Gay also brought up the leak check vs. pressure test issue, and stated that ThompsonGas stresses the difference, especially with new employees and acquisition employees. “It’s as if ‘pressure test’ is a generic term referring to all tests and it isn’t,” he said.
“There is a big difference between the two,” he continued. A pressure test is required on new piping to confirm the integrity and serviceability of the piping, while a leak check is performed on an entire system, whether following a new installation or after an interruption of service, to ensure there are no leaks in the tank, valve, piping, or appliances.
Training: A Trend Toward Customization
Latourell stated that every Paraco employee except for those in corporate administration must complete the CETP Basic Principles and Practices course within their first six months of hire and must follow up with a second course within a year, usually more directed toward their specific duties with the company. The company will eventually require all field employees to finish a third CETP module within their two-year anniversary.
ThompsonGas has become a diverse company, Gay commented, with rail operations, jurisdictional pipeline systems, and a transport company in addition to a retail propane company. Because of that, Gay noted, it departmentalizes its safety training to be more job-specific. As an example, he pointed out that a propane transport driver does not necessarily need to sit through a meeting on leak testing.
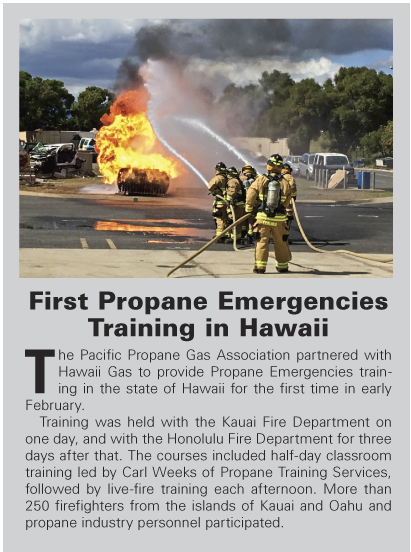
Other Top Safety Issues
Paraco Gas incorporates its uniform policy with safety in mind, including high-visibility clothing, requiring long pants for anyone performing product transfer, safety-toe boots, and “little things that don’t always go over real well with the manpower and entire team,” Latourell noted. Anytime an accident or injury occurs, the company produces an in-depth review of the incident to get to the root causes and make changes and recommendations.
“Whether it’s incorporating the uniform or procedure of policies, or provision of additional equipment, getting to the root cause is normally where you get to the proactive solutions and try to prevent incidents in the future,” he added.
Paraco Gas provides electronic tools, such as GPS systems, for its delivery drivers to minimize distractions. “Driver safety is always key, especially as we operate in commercial and industrial areas,” he noted. “It’s just a lot of maneuvering, a lot of different styles of driving, not just pedestrian traffic. So we’re trying to incorporate less manual process and more electronic processes, eliminating CB radio and focusing on cellular telephone communications but making sure that everyone respects that these things aren’t 100% communication tools automatically,” he continued. Managers and customers want instant gratification, but a driver should not answer the phone while driving or immediately stop what he is doing to answer the phone. “We’re trying to change the mentality that it’s OK to not answer your phone while you’re preoccupied doing something more important.”
Ergonomics is another top safety priority for Paraco Gas, which provides employees with various tools to avoid muscle strain or repetitive motion issues. Because the company offers cylinder exchange services as well as regular propane delivery, the cylinder delivery staff members use hooks to extend their reach and maneuver the cylinders rather than having to climb on the truck and touch every cylinder. Use of hand trucks is encouraged rather than rolling the cylinders.
“We’re giving them more tools to give them more of a sense of what’s going on so they can make sure they do their job safely,” Latourell explained. Combustible gas detectors are an example of such a tool, so employees can detect gas leaks rather than “relying on their noses.” The detectors build customer confidence as well. “When we send our employees out to do product transfers in the field, which is what we consider the most dangerous thing we ask people to do, we make sure we incorporate the proper adaptors, sight flow gauges, and pressure gauges, so these guys can basically have a better assessment of what’s going on in the operation to make sure it goes according to plan and accidents don’t happen. We prefer that guys have more tools than they need so they can use them as needed.”
The increasingly complicated task of keeping employees’ certifications in order is another headache for management. Harold Sweet of Modern Gas Sales, who is president-elect of the Pennsylvania Propane Gas Association, notes that insurance companies want to make sure propane companies are proactive with training to avoid incidents. If a marketer ends up in court, Sweet cautioned, the first thing the opposing attorney will ask is ‘How have you been trained, and what certs do you have?’”
Waters of Premier Safety Services acknowledged that he has seen “more DOT inspections this summer than I’ve seen in my entire life.” Waters, whose service territory covers mostly the northeastern area of the country, added that the DOT inspectors are targeting specific areas of operation rather than conducting an overall inspection. As an example, they might inspect cargo tank leak check records. The department is taking a microscope to driver training records.
“A typical trucking company has to have a driver qualification file, which has 10 things in it,” Waters pointed out. “You have to have a drug and alcohol testing file, hazmat training, vehicle inspection records, and maintenance records. Now the DOT guy is coming in and saying ‘We’re only looking at this 30% of things, and I’m going to look at every ‘i’ and every ‘t’ and make sure it’s crossed, or we’re going to fine you.’” One DOT inspector might show up and look only at cargo tanks, while another might show up soon afterward and look only at cylinder requalification records.
Waters stated that makes it tough for mom and pop companies to keep up, but propane safety experts say keeping the “culture of safety” message is helpful. Hilliard of Revere Gas stated that the company offers rewards for employees who offer ideas to improve safety.
“We do it in different ways,” Hilliard said. “Sometimes it could be a gift card, sometimes we know they have a particular interest in something specific. If we have insight, it shows that we care about them personally.”
Latourell also tries to help employees who want to learn more about safety, whether it’s for their own promotional opportunities or if they are simply interested in following the company’s culture of safety.
“I like to make sure that information is available and accessible to people who want to do a little additional training or self-study, because the more people that are aware of safety and keeping it front and center of what they do, the better chance we have of avoiding accidents and injuries. Trying to develop a safety culture is an ongoing process that’s never done.” —Daryl Lubinsky
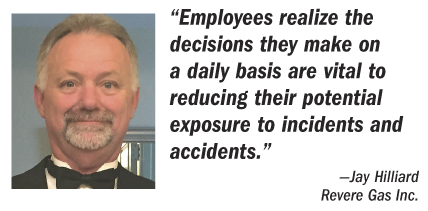
Jay Hilliard, safety and operations director for Revere Gas Inc. (Hartfield, Va.), said he is seeing more companies move toward a culture of safety, which he noted can yield great benefits.
“Employees realize the decisions they make on a daily basis are vital to reducing their potential exposure to incidents and accidents,” Hilliard explained. “They learn that their safety is their responsibility and requires them to be focused on the task at hand.”
The culture of safety is the result of recognizing additional safety requirements in the propane industry, including the increasing regulations that marketers must follow. In addition to standards such as NFPA 58, Environmental Protection Agency rules, and U.S. Department of Transportation (DOT) regulations, propane marketers sometimes give less attention to U.S. Occupational Safety and Health Administration (OSHA) standards. Dave Latourell, director of safety and transportation for Paraco Gas (Rye Brook, N.Y.), said employees often take OSHA regulations for granted.
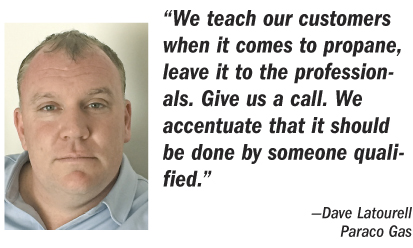
Dan Waters, owner/trainer for Premier Safety Services (Greenville, S.C.), mentioned OSHA’s recent global harmonization system marking requirements for propane containers as a safety mandate that marketers must face. OSHA has adopted new hazardous chemical labeling requirements as a part of its recent revision of the Hazard Communication Standard, 29 CFR 1910.1200 (HCS), bringing it into alignment with the United Nations’ Globally Harmonized System of Classification and Labeling of Chemicals (GHS). The new system “is causing people a lot of grief,” said Waters, whose company assists propane companies with fewer than 100 employees in complying with DOT and OSHA regulations. The company also conducts Certified Employee Training Program (CETP) training. He noted that marketers are having to buy new labels and throw out old ones. And because of the name change from Material Safety Data Sheet (MSDS) to Safety Data Sheet (SDS), marketers must replace their MSDS digital files with SDS files.
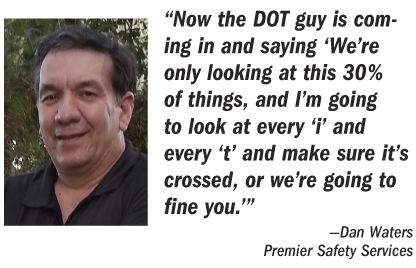
Members of the propane industry whose jobs focus heavily in the area of propane safety note that they see various issues in how safety concerns contribute to a culture of safety.
Educating Customers on the Safety Culture
Benny Gay of ThompsonGas (Frederick, Md.) notes a continuing trend of consumers purchasing space heaters and other equipment from big-box stores and trying to install them on their own.
“They either don’t know of requirements that only qualified personnel perform propane work, or they ignore the requirements, including a leak check following an interruption of service — so they don’t comply with any of the above,” Gay said. “If there’s an incident later, the propane marketer is actually placed at risk, because even though incidents like that were beyond his or her knowledge, if anything pops up in the way of litigation, fingers can be pointed toward the propane marketer. We can’t be responsible for what some consumer takes upon himself in his own home.” He pointed out that the Propane Education & Research Council’s (PERC) duty to warn materials inform residents to call a professional installer rather than install equipment themselves.
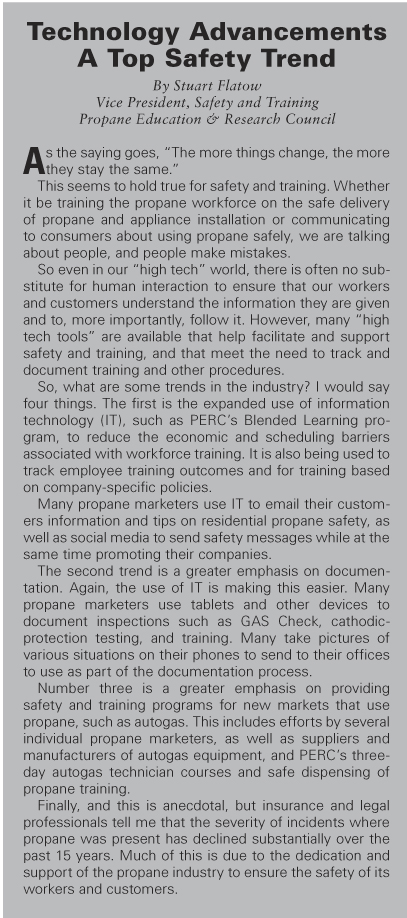
Gay added that legislation in Alabama prohibits anyone other than a licensed professional to perform propane-related work. “Those laws may exist in other states, but that’s just an example of one of the states we operate in that has that kind of legislation available to protect the consumer but ultimately the propane marketer as well.” He added that ThompsonGas doesn’t sell appliances that it does not install. The company doesn’t sell over-the-counter parts and will not offer advice about installing appliances. He likened those questions to someone asking a surgeon over the phone how to perform surgery.
“Everyone is money-conscious. That’s what the do-it-yourself trend is all about,” he explained. “We’re by no means opposed to that, but there are some things you just don’t fool around with. Obviously propane is one of them.”
Latourell of Paraco Gas responded that the company teaches employees to avoid risks, and it makes the same effort with customers. He has seen more scenarios in which customers with no gas grill hookups at their homes buy gas grills and want to hook them up themselves.
“We teach our customers when it comes to propane, leave it to the professionals. Give us a call. We accentuate that it should be done by someone qualified. The more they realize when it comes to gas you really need a professional involved, the more they realize the motivation for us is customer safety. Educating our customers is critical to them making the right decision when it comes to gas and calling the professional.”
Culture of Safety Meetings
According to Gay, ThompsonGas has always believed in the culture of safety, and that means stressing the importance of employee safety through monthly safety meetings. The company uses the meetings and the safety material used at the meetings “as a true training tool.” In addition to PERC materials, Gay and his team use additional materials from ThompsonGas’ suppliers and insurance carrier, covering subject matter such as components of a propane system; defensive driving; slips, trips, and falls; electrical safety; and ladders.
Hilliard provided an example in which Revere Gas’ safety committee addressed employees’ personal safety. The committee evaluated several areas of risk to its employees, including entering and exiting the back of its flatbed trucks. The committee came up with a plan to modify them for improved safety. The company installed ladders and grab rails, which provide safer access and minimize the chance of an employee slipping and falling.
“Safety meetings and the safety committee gets you thinking beyond just avoidance, but how to eliminate the hazard,” Hilliard explained. “When you get employees thinking like that, safety becomes part of their everyday life.”
Buy-in from employees on company safety programs is key, Hilliard added. “They’re the ones out every day doing the work, the ones you rely on to make good solid decisions about keeping themselves out of harm’s way and at the same time getting the job done that they’re there to accomplish.” To get that buy-in, management must have an open-door policy, take their concerns seriously, and bring up the concerns at safety meetings, he stated. When employees feel like their input matters, they tend to speak up more and make management aware of other possibly unsafe conditions.
For example, if propane service techs are working on a job on the roof of a building and don’t feel safe, management should consider letting a professional roofer do the work rather than propane techs who are less experienced with roof work, Hilliard stressed. “If it’s outside what they typically do, it has the potential to carry more risk. We encourage employees to come to us when they see things they feel could be done better or safer or, at a minimum, that they feel needs to be looked at.”
Terminology: Leak Check vs. Pressure Test
Latourell believes that propane industry members should remember to use terminology properly. That includes knowing the difference between a leak check and a pressure test. “For years, the terms pressure test and leak check have been interlaced. They’re not the same thing,” he warned, adding that although the service tech might perform the correct test, if he does not document it correctly, he is leaving an opening for liability and potential litigation. Misuse of terminology can change the entire context of a code or concept, he noted, and that can be as simple as missing punctuation.
“I have two English teachers for parents,” he explained. “In a day and age where it’s OK to misspell everything with texting and typing finger to iPhone, you can really change what you accomplish if you’re not being careful with what you’re inputting or documenting.”
Gay also brought up the leak check vs. pressure test issue, and stated that ThompsonGas stresses the difference, especially with new employees and acquisition employees. “It’s as if ‘pressure test’ is a generic term referring to all tests and it isn’t,” he said.
“There is a big difference between the two,” he continued. A pressure test is required on new piping to confirm the integrity and serviceability of the piping, while a leak check is performed on an entire system, whether following a new installation or after an interruption of service, to ensure there are no leaks in the tank, valve, piping, or appliances.
Training: A Trend Toward Customization
Latourell stated that every Paraco employee except for those in corporate administration must complete the CETP Basic Principles and Practices course within their first six months of hire and must follow up with a second course within a year, usually more directed toward their specific duties with the company. The company will eventually require all field employees to finish a third CETP module within their two-year anniversary.
ThompsonGas has become a diverse company, Gay commented, with rail operations, jurisdictional pipeline systems, and a transport company in addition to a retail propane company. Because of that, Gay noted, it departmentalizes its safety training to be more job-specific. As an example, he pointed out that a propane transport driver does not necessarily need to sit through a meeting on leak testing.
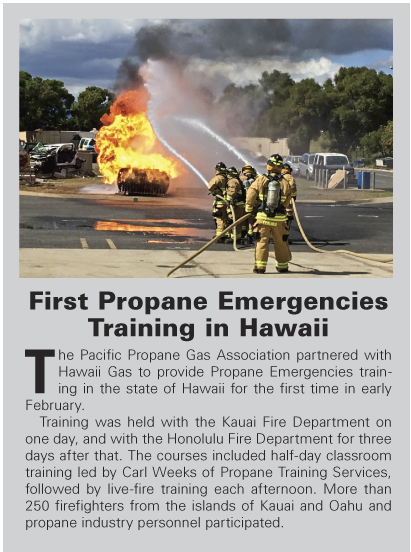
Other Top Safety Issues
Paraco Gas incorporates its uniform policy with safety in mind, including high-visibility clothing, requiring long pants for anyone performing product transfer, safety-toe boots, and “little things that don’t always go over real well with the manpower and entire team,” Latourell noted. Anytime an accident or injury occurs, the company produces an in-depth review of the incident to get to the root causes and make changes and recommendations.
“Whether it’s incorporating the uniform or procedure of policies, or provision of additional equipment, getting to the root cause is normally where you get to the proactive solutions and try to prevent incidents in the future,” he added.
Paraco Gas provides electronic tools, such as GPS systems, for its delivery drivers to minimize distractions. “Driver safety is always key, especially as we operate in commercial and industrial areas,” he noted. “It’s just a lot of maneuvering, a lot of different styles of driving, not just pedestrian traffic. So we’re trying to incorporate less manual process and more electronic processes, eliminating CB radio and focusing on cellular telephone communications but making sure that everyone respects that these things aren’t 100% communication tools automatically,” he continued. Managers and customers want instant gratification, but a driver should not answer the phone while driving or immediately stop what he is doing to answer the phone. “We’re trying to change the mentality that it’s OK to not answer your phone while you’re preoccupied doing something more important.”
Ergonomics is another top safety priority for Paraco Gas, which provides employees with various tools to avoid muscle strain or repetitive motion issues. Because the company offers cylinder exchange services as well as regular propane delivery, the cylinder delivery staff members use hooks to extend their reach and maneuver the cylinders rather than having to climb on the truck and touch every cylinder. Use of hand trucks is encouraged rather than rolling the cylinders.
“We’re giving them more tools to give them more of a sense of what’s going on so they can make sure they do their job safely,” Latourell explained. Combustible gas detectors are an example of such a tool, so employees can detect gas leaks rather than “relying on their noses.” The detectors build customer confidence as well. “When we send our employees out to do product transfers in the field, which is what we consider the most dangerous thing we ask people to do, we make sure we incorporate the proper adaptors, sight flow gauges, and pressure gauges, so these guys can basically have a better assessment of what’s going on in the operation to make sure it goes according to plan and accidents don’t happen. We prefer that guys have more tools than they need so they can use them as needed.”
The increasingly complicated task of keeping employees’ certifications in order is another headache for management. Harold Sweet of Modern Gas Sales, who is president-elect of the Pennsylvania Propane Gas Association, notes that insurance companies want to make sure propane companies are proactive with training to avoid incidents. If a marketer ends up in court, Sweet cautioned, the first thing the opposing attorney will ask is ‘How have you been trained, and what certs do you have?’”
Waters of Premier Safety Services acknowledged that he has seen “more DOT inspections this summer than I’ve seen in my entire life.” Waters, whose service territory covers mostly the northeastern area of the country, added that the DOT inspectors are targeting specific areas of operation rather than conducting an overall inspection. As an example, they might inspect cargo tank leak check records. The department is taking a microscope to driver training records.
“A typical trucking company has to have a driver qualification file, which has 10 things in it,” Waters pointed out. “You have to have a drug and alcohol testing file, hazmat training, vehicle inspection records, and maintenance records. Now the DOT guy is coming in and saying ‘We’re only looking at this 30% of things, and I’m going to look at every ‘i’ and every ‘t’ and make sure it’s crossed, or we’re going to fine you.’” One DOT inspector might show up and look only at cargo tanks, while another might show up soon afterward and look only at cylinder requalification records.
Waters stated that makes it tough for mom and pop companies to keep up, but propane safety experts say keeping the “culture of safety” message is helpful. Hilliard of Revere Gas stated that the company offers rewards for employees who offer ideas to improve safety.
“We do it in different ways,” Hilliard said. “Sometimes it could be a gift card, sometimes we know they have a particular interest in something specific. If we have insight, it shows that we care about them personally.”
Latourell also tries to help employees who want to learn more about safety, whether it’s for their own promotional opportunities or if they are simply interested in following the company’s culture of safety.
“I like to make sure that information is available and accessible to people who want to do a little additional training or self-study, because the more people that are aware of safety and keeping it front and center of what they do, the better chance we have of avoiding accidents and injuries. Trying to develop a safety culture is an ongoing process that’s never done.” —Daryl Lubinsky