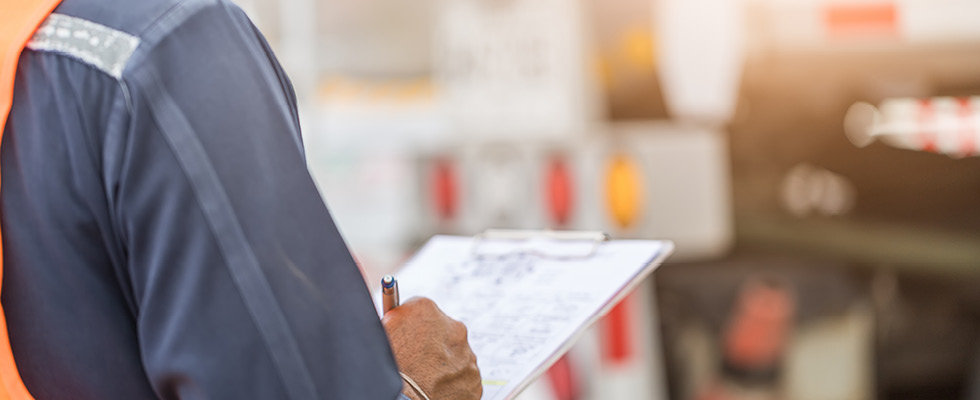
Underground storage tanks are widely used for storing petroleum products, chemicals and other hazardous materials, including propane. However, these tanks are highly susceptible to corrosion, which can lead to structural failure, environmental contamination and severe financial consequences.
To mitigate these risks, cathodic protection is a critical method used to prevent corrosion and extend the lifespan of underground tanks.
Why Is Cathodic Protection Important?
Corrosion occurs when metal reacts with environmental elements such as moisture, electrical current and different chemical compositions, which attack the steel structure of the tank, resulting in rust and pitting and weakening the overall structural integrity of the tank.
Cathodic protection works by altering the electrochemical environment of the tank to prevent corrosion. There are two primary types of cathodic protection systems:
- Sacrificial anode systems: These systems use highly active metals (such as magnesium or zinc) that corrode in place of the tank, thereby protecting it from deterioration.
- Impressed current systems: These involve an external power source that delivers a controlled electrical current to counteract the corrosion process. For this article, we will not focus specifically on this system.
By implementing cathodic protection, underground storage tank owners can significantly reduce maintenance costs, enhance safety and comply with environmental regulations. Within the propane industry, the focus is around sacrificial anode systems and tank coating.
Cathodic Protection in the Propane Industry
For underground propane tanks, cathodic protection is not just a recommendation — it is a regulatory requirement. Propane tanks are made from steel, which is highly susceptible to corrosion when buried underground. The application of cathodic protection ensures that the structural integrity of the tank is maintained over time, reducing the risk of gas leaks and explosions.
NFPA Guidelines & Regulations
The National Fire Protection Association (NFPA) 58 guidelines set the foundation for cathodic protection requirements, but it is important to recognize that these standards represent the minimum requirements for compliance. Industry best practices often go beyond these baseline regulations to ensure enhanced safety, extended tank longevity and reduced risk of failure. Proactive maintenance and more frequent monitoring of cathodic protection systems can further safeguard against potential hazards. By exceeding NFPA standards, propane marketers and tank owners can achieve greater reliability and operational efficiency.
The NFPA provides key regulatory guidance for the propane industry, particularly in NFPA 58: Liquefied Petroleum Gas Code. This code outlines specific requirements for the installation, maintenance and monitoring of cathodic protection systems for underground propane tanks:
- Cathodic protection system installation: NFPA 58 mandates that underground propane tanks be equipped with a cathodic protection system, including a sacrificial anode and OEM-approved tank coating at the time of installation.
- Periodic testing: The regulation requires that cathodic protection systems be tested at the time of installation, 12-18 months after installation, and then at least every 36 months to ensure they are functioning correctly.
- Minimum protection levels: The cathodic protection system must maintain a minimum voltage potential to effectively prevent corrosion, typically measured at -0.85 volts or more negative, with reference to a saturated copper-copper sulfate half cell.
- Recordkeeping requirements: Propane tank owners must maintain documentation of cathodic protection system inspections and testing results for regulatory compliance for at least the last two inspections.
- Anode replacement: When sacrificial anode systems are used, they must be periodically checked and replaced as needed to maintain protection levels.
Failure to comply with NFPA 58 regulations can lead to fines, legal liabilities and increased risk of propane leaks that could result in catastrophic incidents.
Overlooking Cathodic Protection
Failure to install or properly maintain a cathodic protection system can have devastating consequences. As highlighted in 'Best Practices for Anchoring & Maintaining Propane Tanks in Coastal Areas,' tanks in coastal areas are particularly susceptible to corrosion due to environmental factors. Some of the major risks include:
- Catastrophic costs: The financial implications of failing to monitor and respond to corrosion issues can reach into the hundreds of millions of dollars due to legal claims, regulatory fines, cleanup costs and reputational damage.
- Structural failure: Over time, corrosion weakens the tank walls, making them prone to leaks and collapse.
- Propane leaks and explosions: Unlike petroleum leaks, propane gas leaks pose an immediate explosion hazard if exposed to ignition sources.
- Environmental pollution: Corroded propane tanks can release hazardous substances into the soil.
- Legal and financial penalties: Noncompliance with NFPA 58 and other regulatory standards can result in hefty fines and liability claims.
- Loss of business and reputation: Propane suppliers and distributors risk severe reputational damage if their tanks cause safety or environmental hazards.
Real-World Examples of Corrosion-Related Failures in Propane Storage
Several incidents highlight the dangers of failing to protect underground tanks:
- Residential propane tank leaks: Cases have been reported where improperly maintained underground propane tanks developed leaks due to corrosion, leading to fires and explosions.
- Commercial propane storage failures: Businesses that store large amounts of propane have faced regulatory penalties and financial losses due to tank corrosion.
- Legal actions: Property owners have filed lawsuits against propane suppliers when underground tanks failed due to insufficient protection.
Technological Advancements in Cathodic Protection Monitoring
Traditional cathodic protection systems require periodic manual inspections, which can be inefficient and prone to human error. However, modern technology now allows for real-time monitoring and automated maintenance of cathodic protection systems. Key benefits of this technology include:
- Real-time data monitoring: Allows operators to track the effectiveness of cathodic protection systems remotely via cloud-based platforms.
- Automated alerts: Sends notifications when protection levels drop below optimal thresholds.
- Twice-daily cathodic monitoring alerts: A major differentiator for marketers, providing frequent updates and allowing for quick response to potential issues.
- Increased accuracy: Provides precise measurements, reducing the risk of undetected corrosion.
- Cost efficiency: Minimizes the need for manual inspections and reduces maintenance expenses, protecting one of your most expensive — and valuable — assets.
Financial & Legal Benefits of Cathodic Monitoring Technology
Implementing advanced cathodic monitoring technology can provide significant financial and legal advantages for propane marketers and tank owners. By maintaining continuous monitoring and detailed reporting, businesses can:
- Save thousands of dollars: Proactively proving compliance and responsible tank management can help reduce insurance premiums and legal liabilities.
- Provide documentation for legal and insurance purposes: Detailed monitoring records serve as evidence of due diligence in preventing corrosion-related failures, which can be crucial in legal disputes or insurance claims.
- Avoid catastrophic costs: The financial impact of failing to monitor and respond to cathodic protection system failures can reach into the hundreds of millions of dollars due to legal claims, regulatory fines, cleanup costs and reputational damage.
- Enhance business reputation and customer trust: Demonstrating a commitment to safety and compliance reassures customers and strengthens business credibility.
By integrating innovative cathodic protection technologies, propane industry professionals can enhance their corrosion prevention strategies, ensuring the long-term safety and efficiency of their underground propane tanks.
Safety & Peace of Mind for Marketers & Customers
Beyond regulatory compliance, ensuring the integrity of underground propane tanks through cathodic protection provides peace of mind for both marketers and customers. For marketers, a well-maintained cathodic protection system minimizes liability, prevents costly environmental cleanup and protects business reputation. For customers, it guarantees their propane supply is stored safely, reducing the risk of hazardous leaks or failures.
Investing in advanced cathodic protection measures fosters trust between suppliers and consumers, reinforcing the commitment to safety and reliability in the propane industry.
Cathodic protection is an essential measure for safeguarding underground propane tanks from corrosion-related failures. Without adequate protection, underground storage tanks pose significant environmental, financial and safety risks. However, with the advent of modern cathodic protection monitoring systems, propane tank operators can now ensure continuous protection monitoring with greater accuracy and efficiency.
Compliance with NFPA 58 guidelines and investing in robust cathodic protection solutions are not only regulatory necessities, but also crucial steps toward sustainable and safe propane storage operations.