Monday, April 17, 2017
Autogas is growing, and in a big way. It no longer is the niche segment of the industry that it was in the past several decades, but is now recognized as one of the best growth opportunities in the market. With this change comes growth in the scale and design of fueling stations. While the traditional 1000-gal. to 2000-gal. skid-mounted systems are still in demand and will continue to be, as the sizes of the fleets grow, so does the size of the station. With the prolific demand for school buses in particular, the scope and size of refueling stations has grown exponentially, and nowhere more so than in Texas, of course, where bigger is always better!
School districts like Leander ISD, Houston ISD, Clear Creek ISD, Conroe ISD, and municipal fleets such as VIA Metropolitan Transit and the city of San Antonio have autogas stations we wouldn’t have imagined just 10 to 15 years ago. Twelve 30,000-gal. storage tanks, as many as 10 or more dispensing hoses, integrated fuel management, and fully automated safety controls are likely part of the station of today. Many are located in congested areas requiring special permitting and very comprehensive fire safety analysis. In effect, autogas stations of all sizes are now being looked at in the same way as those for gasoline, diesel, and aviation fuels have been scrutinized and standardized on design for more than 50 years. This is a positive direction in that these requirements further add to the acceptance by both regulators and fleet operators and management, who take comfort in the safety, reliability, appearance, and user friendliness of the fuels they are familiar with. Cabinet dispensers, free-standing meters, and minimal safety measures are now, more often than not, seen as unacceptable. Acceptance of the overall experience of fueling from the driver, to the fleet manager, to the local fire marshal or AHJ are now equally critical and part of the investment decision, as the fuel savings and environmental benefits—and propane autogas is actually in a good position to capitalize on this. No longer do these stations need to be approached from the minimalist perspective common to a small reseller station. A large-scale autogas station, incorporating more safety and automation, while a very substantial investment, is frequently far less expensive than the cost of a similar scale gasoline or diesel station with an expense that large fleet operators understand and can justify.
These issues also generally require a higher level of safety designed into the station system. Where in the past internal valves might only be used on the liquid supply line to the pump, they are now installed in all openings—pump supply, bypass return, and vapor return from dispenser meters. Dedicated tank design to accommodate these openings and additional separate openings for transport offloading are now common. Internal valves that were once left open all the time and only closed in the event of an emergency with a mechanical or pneumatic emergency shutoff, sometimes using propane vapor, are now normally closed and only opened on command from the dispenser as needed. Complex sequencing and control panels are designed to ensure the pumps are properly primed and vapor displaced before energizing the pump motors. Where the dispenser might have had a separate and sometimes inconspicuous electrical shutoff, it now has a single-point and fueling industry standard EPO (emergency power off) button that closes the internal valves and interrupts the electrical continuity for ALL conductors entering the hazardous areas. Tanks are sometimes painted with intumescent paint or other coatings to give them a longer safe exposure time when exposed to fire. Leak and gas detection systems that sound an audible and/or visual alarm once reaching a percentage of the lower flammability limit, and automatically trigger the EPO system, are also options.
Large fleets with a substantial percentage of propane-powered vehicles also require a much higher reliability factor. Where one small pump might be adequate to deliver a minimal flow rate to one or two delivery hoses, now several pumps are required, and often, several more for redundancy. Where pumps were once controlled by simple on-off switches, they are now powered through sequencing control panels with variable frequency drives (VFDs) to eliminate the potential for vapor lock, and provide consistent and peak flow rates, while effectively reducing power consumption. VFDs are no longer just used for phase conversion, but as sophisticated motor drive controls, programmed to maintain line pressure at all times, from rapid start to flow. Some of these stations with multiple dispensers can be located as far as 300 to 500 feet from the storage tank. When 50% or more of a fleet is operating on propane, even a small possibility of a system failure and inability to flow, is unacceptable. Reliability must be a major consideration in design.
The use of more and more sophisticated fuel management systems, well known to the gasoline and diesel industry, are now being integrated with autogas. However, these can pose new issues not experienced in the past. The installers and distributors of these systems most often have no experience with LPG, and are frequently afraid to touch it. The use of true RMFDs (retail motor fuel dispensers) certified by NTEP for the service in which they are being used, and UL 495 and other listings are often now a requirement. Dispenser manufacturers can expect that they will have to integrate with these systems, and most likely, will have to either directly make the installation and connections, or be prepared to provide substantial assistance. Fuel management options such as RFID proximity systems, using radio frequency to identify, authorize and transfer data for vehicle fueling, are common. With the new, unique, and frequently inconsistent location or type of autogas fill valve, the LPG system can very often be blamed for faults in the fuel management system. Support, both at the time of installation and ongoing, is critical.
A typical example of this is Houston Independent School District (HISD). HISD shop manager, Andres Montes, has seen his fleet grow over the years since its first trial with autogas buses in 2011. The use of aftermarket systems was a major problem in the early adoption of LPG then, but with the introduction of OEM vehicles from Blue Bird, Thomas Built and others, large fleets have found more comfort and reliability. “Having OEM-installed systems is the only way to go; having factory support makes it the best choice,” says Montes.
The school district is planning to grow its autogas fleet to 50% in the next year, and add a second refueling station. With 161 buses and 20 light-duty Ford vans, it used more than 600,000 gallons of autogas in 2016, and could as much as double that in the next year or two.
HISD currently has one fueling station. This station, designed and installed by Propane Specialty Service (PSS; Leesville, Texas), has one 18,000-gal. tank with four dual-hose dispensers for autogas, a larger presence than it has for diesel and gasoline. The station, as designed and installed by PSS, has three Blackmer LGL158 pumps, two as primary and the third for redundancy. The pump motors are powered by TECO variable frequency AC drives, programmed for the specific needs of the site. Because of the extreme Texas climate, the drives are mounted outside in purpose-built enclosures with temperature controls. The drives are controlled through a sequencing control panel, and started on command from the pump controls of the Parafour P4-200 series dispensers. Each hose has a BlueMoon filter installed to protect the liquid injection systems on the vehicles. Pump starting voltage is delivered by the drives, after the dispenser command to the control panel opens the storage tank internal valves, with a time delay function to allow the valves to fully open and prime the pumps. There are several EPO button stations, exactly the same as those used for HISD’s diesel dispensers, located both under the refueling canopy and near the pumping station by the tank. Internal valves are controlled with a Parafour P4-ECO-air, a self-contained and maintenance-free air compressor. The FuelForce fuel management system works with the dispensers seamlessly. “The use of advanced technology, safety, and components is very beneficial to HISD. It lets us monitor fuel usage, mileage, and users, while helping us maintain a safe environment for fueling,” says Montes. “Obviously there is a comfort and acceptance level in having a fueling system with dispensers similar to our diesel and gasoline dispensers, since the refueling procedures are basically the same. Overall there has been very positive support from the school system and the students’ parents, due to noise reduction and emissions levels.”
While these stations are not a small investment, they are still less than 50% of the cost of a new diesel or gasoline station of similar capacity, and have much lower on-going costs for monitoring and maintenance. This was a very significant investment on behalf of HISD with support from grants provided by the state of Texas. Montes is proud of the accomplishment and is pleased with the experience both in fuel savings for the school district, and with the reliability, service, and support for the system from the manufacturers and installers. “Grant funding played a big role in initially purchasing propane buses and infrastructure, but also the fact that HISD is contributing to cleaner air is what matters most.”
More such stations are on the way in Texas. The city of San Antonio, which currently has one location with two 18,000-gal. tanks and five single-hose dispensers, will soon start construction of a second fueling facility planned to have a single 230,000-gal. underground tank with five single-hose dispensers. This site will incorporate even more advancements and may be the first site in the U.S. to use deep well submersible pumps, common in most of the world, but not as yet used in the North American markets. This is not exclusive to Texas—other fleets in many states are now adopting the use of much larger capacity stations with expanded use of controls and safety integration.
Propane autogas has come of age in the U.S., and the industry must continue to invest and support greater levels of safety and automation.
(by Robin Parsons, president of Parafour Innovations LLC (Georgetown, Texas)
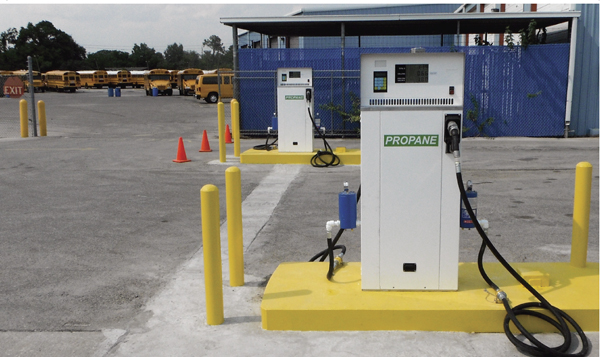
School districts like Leander ISD, Houston ISD, Clear Creek ISD, Conroe ISD, and municipal fleets such as VIA Metropolitan Transit and the city of San Antonio have autogas stations we wouldn’t have imagined just 10 to 15 years ago. Twelve 30,000-gal. storage tanks, as many as 10 or more dispensing hoses, integrated fuel management, and fully automated safety controls are likely part of the station of today. Many are located in congested areas requiring special permitting and very comprehensive fire safety analysis. In effect, autogas stations of all sizes are now being looked at in the same way as those for gasoline, diesel, and aviation fuels have been scrutinized and standardized on design for more than 50 years. This is a positive direction in that these requirements further add to the acceptance by both regulators and fleet operators and management, who take comfort in the safety, reliability, appearance, and user friendliness of the fuels they are familiar with. Cabinet dispensers, free-standing meters, and minimal safety measures are now, more often than not, seen as unacceptable. Acceptance of the overall experience of fueling from the driver, to the fleet manager, to the local fire marshal or AHJ are now equally critical and part of the investment decision, as the fuel savings and environmental benefits—and propane autogas is actually in a good position to capitalize on this. No longer do these stations need to be approached from the minimalist perspective common to a small reseller station. A large-scale autogas station, incorporating more safety and automation, while a very substantial investment, is frequently far less expensive than the cost of a similar scale gasoline or diesel station with an expense that large fleet operators understand and can justify.
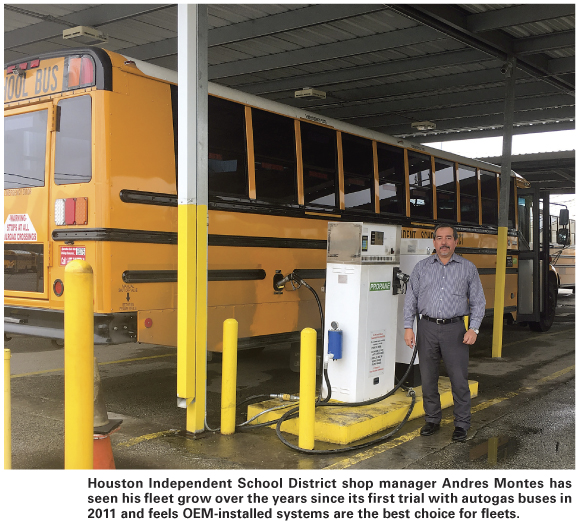
These issues also generally require a higher level of safety designed into the station system. Where in the past internal valves might only be used on the liquid supply line to the pump, they are now installed in all openings—pump supply, bypass return, and vapor return from dispenser meters. Dedicated tank design to accommodate these openings and additional separate openings for transport offloading are now common. Internal valves that were once left open all the time and only closed in the event of an emergency with a mechanical or pneumatic emergency shutoff, sometimes using propane vapor, are now normally closed and only opened on command from the dispenser as needed. Complex sequencing and control panels are designed to ensure the pumps are properly primed and vapor displaced before energizing the pump motors. Where the dispenser might have had a separate and sometimes inconspicuous electrical shutoff, it now has a single-point and fueling industry standard EPO (emergency power off) button that closes the internal valves and interrupts the electrical continuity for ALL conductors entering the hazardous areas. Tanks are sometimes painted with intumescent paint or other coatings to give them a longer safe exposure time when exposed to fire. Leak and gas detection systems that sound an audible and/or visual alarm once reaching a percentage of the lower flammability limit, and automatically trigger the EPO system, are also options.
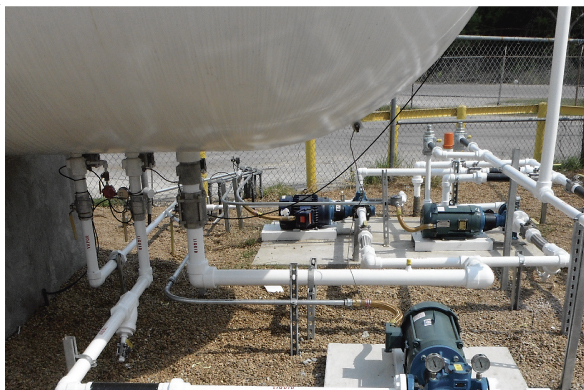
Large fleets with a substantial percentage of propane-powered vehicles also require a much higher reliability factor. Where one small pump might be adequate to deliver a minimal flow rate to one or two delivery hoses, now several pumps are required, and often, several more for redundancy. Where pumps were once controlled by simple on-off switches, they are now powered through sequencing control panels with variable frequency drives (VFDs) to eliminate the potential for vapor lock, and provide consistent and peak flow rates, while effectively reducing power consumption. VFDs are no longer just used for phase conversion, but as sophisticated motor drive controls, programmed to maintain line pressure at all times, from rapid start to flow. Some of these stations with multiple dispensers can be located as far as 300 to 500 feet from the storage tank. When 50% or more of a fleet is operating on propane, even a small possibility of a system failure and inability to flow, is unacceptable. Reliability must be a major consideration in design.
The use of more and more sophisticated fuel management systems, well known to the gasoline and diesel industry, are now being integrated with autogas. However, these can pose new issues not experienced in the past. The installers and distributors of these systems most often have no experience with LPG, and are frequently afraid to touch it. The use of true RMFDs (retail motor fuel dispensers) certified by NTEP for the service in which they are being used, and UL 495 and other listings are often now a requirement. Dispenser manufacturers can expect that they will have to integrate with these systems, and most likely, will have to either directly make the installation and connections, or be prepared to provide substantial assistance. Fuel management options such as RFID proximity systems, using radio frequency to identify, authorize and transfer data for vehicle fueling, are common. With the new, unique, and frequently inconsistent location or type of autogas fill valve, the LPG system can very often be blamed for faults in the fuel management system. Support, both at the time of installation and ongoing, is critical.
A typical example of this is Houston Independent School District (HISD). HISD shop manager, Andres Montes, has seen his fleet grow over the years since its first trial with autogas buses in 2011. The use of aftermarket systems was a major problem in the early adoption of LPG then, but with the introduction of OEM vehicles from Blue Bird, Thomas Built and others, large fleets have found more comfort and reliability. “Having OEM-installed systems is the only way to go; having factory support makes it the best choice,” says Montes.
The school district is planning to grow its autogas fleet to 50% in the next year, and add a second refueling station. With 161 buses and 20 light-duty Ford vans, it used more than 600,000 gallons of autogas in 2016, and could as much as double that in the next year or two.
HISD currently has one fueling station. This station, designed and installed by Propane Specialty Service (PSS; Leesville, Texas), has one 18,000-gal. tank with four dual-hose dispensers for autogas, a larger presence than it has for diesel and gasoline. The station, as designed and installed by PSS, has three Blackmer LGL158 pumps, two as primary and the third for redundancy. The pump motors are powered by TECO variable frequency AC drives, programmed for the specific needs of the site. Because of the extreme Texas climate, the drives are mounted outside in purpose-built enclosures with temperature controls. The drives are controlled through a sequencing control panel, and started on command from the pump controls of the Parafour P4-200 series dispensers. Each hose has a BlueMoon filter installed to protect the liquid injection systems on the vehicles. Pump starting voltage is delivered by the drives, after the dispenser command to the control panel opens the storage tank internal valves, with a time delay function to allow the valves to fully open and prime the pumps. There are several EPO button stations, exactly the same as those used for HISD’s diesel dispensers, located both under the refueling canopy and near the pumping station by the tank. Internal valves are controlled with a Parafour P4-ECO-air, a self-contained and maintenance-free air compressor. The FuelForce fuel management system works with the dispensers seamlessly. “The use of advanced technology, safety, and components is very beneficial to HISD. It lets us monitor fuel usage, mileage, and users, while helping us maintain a safe environment for fueling,” says Montes. “Obviously there is a comfort and acceptance level in having a fueling system with dispensers similar to our diesel and gasoline dispensers, since the refueling procedures are basically the same. Overall there has been very positive support from the school system and the students’ parents, due to noise reduction and emissions levels.”

While these stations are not a small investment, they are still less than 50% of the cost of a new diesel or gasoline station of similar capacity, and have much lower on-going costs for monitoring and maintenance. This was a very significant investment on behalf of HISD with support from grants provided by the state of Texas. Montes is proud of the accomplishment and is pleased with the experience both in fuel savings for the school district, and with the reliability, service, and support for the system from the manufacturers and installers. “Grant funding played a big role in initially purchasing propane buses and infrastructure, but also the fact that HISD is contributing to cleaner air is what matters most.”
More such stations are on the way in Texas. The city of San Antonio, which currently has one location with two 18,000-gal. tanks and five single-hose dispensers, will soon start construction of a second fueling facility planned to have a single 230,000-gal. underground tank with five single-hose dispensers. This site will incorporate even more advancements and may be the first site in the U.S. to use deep well submersible pumps, common in most of the world, but not as yet used in the North American markets. This is not exclusive to Texas—other fleets in many states are now adopting the use of much larger capacity stations with expanded use of controls and safety integration.
Propane autogas has come of age in the U.S., and the industry must continue to invest and support greater levels of safety and automation.
(by Robin Parsons, president of Parafour Innovations LLC (Georgetown, Texas)