Monday, February 17, 2020
(February 17, 2020) — Propane has long been the fuel of choice for a variety of agricultural applications including irrigation and power generation. For good reason. It is cleaner burning, does not harm water or soil because it’s nontoxic, and produces a carbon footprint that’s more of a tiptoe than a stomp.
Recently, propane-fueled engine technology took a major step forward with the introduction of Industrial-Irrigation Services’ Reliable Horsepower line of engines. Available with displacements of 5.7-, 6.2-, 8.0-, 9.1-, and 10.3-liters, these engines cover the displacement ranges previously available, but are designed to not only provide more efficient operation, but to deliver never-before-available reliability, monitoring, and control options.
The Reliable Horsepower line is a result of a partnership between Industrial-Irrigation Services, the Propane Education & Research Council (PERC), and Woodward Inc., a manufacturer of (among other things) electronic engine control systems. In addition to improved reliability and engine control, the new engines are EPA certified, which eliminates concerns about exhaust emissions compliance.
Agricultural engines have been required to meet EPA certification requirements since 2008, so the issue isn’t initial compliance, it’s ongoing compliance. The new control systems address that consideration head-on with their enhanced monitoring and control capabilities.
PERC was deeply involved in the development of the new engine line. According to Michael Newland, PERC’s director of agriculture business development, “Our overall mission is to promote safety, to look for additional business opportunities, and to help develop new uses and applications for propane. To that end, we often partner with manufacturers to assist with new product development and exposure.”
While PERC obviously has a vested interest in expanding propane use, it also has serious concerns about safety and reliability. It’s well documented that existing modes of power for agricultural applications (diesel and electric) often suffer from reliability problems, can be expensive, and may not be readily available.
According to Newland, “We’re excited about these new engines not only because they help advance the propane industry, but their control systems can help improve productivity because they require less maintenance and deliver more reliable operation. That translates to less downtime, so for irrigation, they spend more time pumping and less time shut down for repairs or adjustment. They’re also better for the environment. Propane is cleaner burning than diesel fuel or gasoline, and since these new engines meet the latest EPA certification requirements, they are especially clean running.”
Multi-Fuel Capability
Another advantage is that these engines can be switched from propane to natural gas with the flip of a switch. That means operators don’t have to shut down operation or engage in a lengthy switch-over if they need to change fuel sources.
That is obviously not a consideration at installations where propane is the only fuel source used. However, according to Jay Canada, Industrial-Irrigation’s vice president of sales and engineering, “There are quite a few farming operations that are located near natural gas pipelines, and that provides operators with a fueling option. Propane is the preferred fuel because it has a higher Btu content and that enables an engine to produce higher horsepower. However, multi-fuel capability is an advantage because it provides an option if propane is temporarily unavailable.”
Another reason for multi-fuel capability is that these engines are intended for additional uses beyond irrigation. Oil and gas production and power generation are two other applications for which these engines are ideally suited. When used for oil and gas production, the ability to switch fuels is especially attractive. Typically, when engines are used for pumping, they are started and run for a few days or weeks on propane. They aren’t switched over to wellhead gas until flow out of the ground is steady and reliable.
The Reliable Horsepower engines are based on existing GM architecture and, like their predecessors, incorporate components specifically designed for heavy-duty industrial use.
Impressive Torque
Horsepower ratings, which are a function of engine speed, are unimpressive as the advertised rating is at either 2800 or 3000 rpm. Torque is an entirely different situation as all engines generate impressive numbers at or below 2000 rpm. As an example, the 5.7-liter (350 cid) engine generates 437 lb/ft at 2000 rpm while the 10.3-liter (632 cid) version generates 798 lb/ft at 1200 rpm.
For pumping operations (such as with water, oil, or gas) torque is the relevant consideration—just as it is with a tractor or any other piece of farm equipment. Torque is an engine’s ability to overcome rotational resistance, such as that required by a pump. Horsepower is an engine’s torque output multiplied by engine speed. Internal combustion engines produce maximum torque at much lower rpm levels than maximum horsepower. Above the peak rpm point, torque decreases, although horsepower continues to increase—to a point—because of the engine speed multiplication factor.
Consequently, industrial engines, which operate under relatively constant and heavy loads, are designed to produce maximum torque at lower engine speeds.
The torque figures quoted are for engines fueled by propane. Output when fueled by natural gas is somewhat lower. As an example, the 10.3-liter engine produces 798 lb/ft of torque at 1200 rpm on propane, but only 723 lb/ft at 1800 rpm on natural gas. Obviously, propane is the better fuel as natural gas requires that an engine operate at higher speed to produce less power.
In addition to the five displacements currently available, Industrial-Irrigation Services plans to add both larger and smaller versions. According to Industrial-Irrigation’s Jay Canada, providing engines for irrigation system use is definitely not a one-size-fits-all proposition. “There are needs for a variety of engine sizes (power output levels), but, currently, there isn’t a wide variety of choices, so we will be expanding the Reliable Horsepower line. We’re looking at the needs of farms from sea level to 6000 to 8000 feet. The higher you go, the less power an engine will produce, so an engine that’s perfect for operation at sea level won’t produce sufficient power at high altitude. The distance you have to push water is another factor that affects power requirements, as is lift distance. Obviously, more power is required to pull water out of a 1000-foot well than to pump ground water. Once the variables involved are defined, we can specify an engine to meet a customer’s requirements.”
All Reliable Horsepower engines utilize the time-proven cast iron blocks and cylinder heads which are cast and machined in North America. Other components include aluminum intake manifolds, forged steel connecting rods, forged steel or nodular iron crankshafts, steel billet camshafts, and hydraulic roller valve lifters.
“Techies” might be surprised that all engines in the line incorporate cast iron blocks and heads and overhead valves, as opposed to aluminum castings and overhead cams. Reliability, cost, and application considerations are the major factors driving component selection. As noted, these engines are designed to operate at low speed, hence there is no advantage to an overhead cam configuration, which offers its advantages at high engine speeds. Additionally, overhead cam engines are much more expensive to repair or rebuild and failure of the cam drive system can result in significant engine damage.
Updated Fuel System
The actual hard parts that comprise a Reliable Horsepower engine have proven their reliability. What was needed was an updated fuel system that was equally reliable—and offered options made possible by recent technological developments. The new fuel system is therefore designed to conquer the most commonly encountered types of engine problems—failure to start, rough operation, and unexpected engine shut-down—that are typically a result of issues with the fuel delivery system.
It’s difficult to achieve reliable horsepower with an unreliable fuel system, and as the name implies, the new Reliable Horsepower engines are optimized to be reliable. For irrigation use, that means the engines run from the time they’re started until they’re turned off—with no stumbles.
To that end, Industrial-Irrigation Services partnered with Woodward Inc. to develop systems that offered both the required operational reliability and never-before-available control. These systems are also configurable to meet individual customer preferences, which include fuel type. All engines are bi-fuel capable, hence controls can be specified for propane-only, or multiple fuel types (propane, pipeline natural gas, wellhead gas).
The new fuel systems can be configured to allow the operator to flip a switch to change fuel type, or controls can be incorporated to enable the system to automatically switch fuel type if one runs out. Electronics also enable a number of other advantages.
All engines incorporate a throttle body-style of electronic fuel injection and include exhaust system oxygen sensors that monitor air/fuel ratio and pass it to the engine control module (ECM). In turn, the ECM makes whatever changes are necessary to maintain the desired air/fuel ratio. The ECM is programmable, thereby enabling operators to create custom calibrations to suit their particular operating environments.
That’s difficult to do with one-size-fits mechanical or non-programmable control systems. Conversely, the Reliable Horsepower systems not only continually optimize fuel and ignition settings to achieve maximum fuel economy and minimal exhaust emissions, the system can also be remotely monitored and controlled and even incorporates an emergency “kill switch.”
Remote Control, Monitoring
If you use your smartphone to lock or unlock your vehicle, monitor security cameras, or turn lights or appliances on or off, you’re already familiar with remote control and monitoring technology. Most commonly, that technology is implemented through use of the Internet of Things (IoT), which provides a means for “things” to communicate with each other. Remote monitoring and control provide a new level of safety and efficiency. All an operator has to do is pick up his or her cell phone to check engine speed, coolant temperature, oxygen sensor voltage, or a host of other sensors. The system can also store multiple calibrations so operation can be optimized for changes in operating environment (i.e high temperature/dry or cool temperature/wet). In spite of the sophistication of the control systems, they are designed to be user friendly.
Rather than having to stand right next to an engine, operators can use their cell phone from literally any part of the world with cell connectivity to monitor and control an engine. Remote control capability also opens new options for engine placement. The ability to remotely raise or lower engine speed, or to kill engine operation means that engine location can be optimized for operation rather than access.
In terms of in-the-field use, one of the greatest advantages of the Reliable Horsepower engine packages is summed up by a statement from Industrial-Irrigation Services: “All those trips to the north 40 to turn on or shut off the pumps can be a thing of the past with our fully electronic engine packages. We help you conserve both time and water with engine packages featuring remote start/stop and remote monitoring.”
The bottom line is that reliability leads to more productivity and increased profits, and that’s exactly what the Reliable Horsepower engine line is designed to deliver.
Dave Emanuel has written seven books and 2500 magazine articles covering a variety of topics ranging from automotive racing and performance modifications to political commentary. His automotive books and articles are informed by his hands-on background with engines and drivelines.
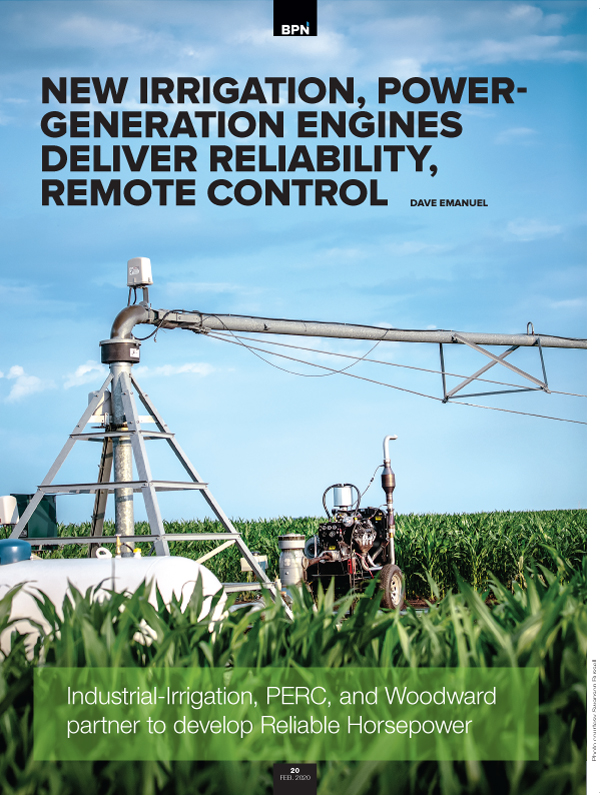
The Reliable Horsepower line is a result of a partnership between Industrial-Irrigation Services, the Propane Education & Research Council (PERC), and Woodward Inc., a manufacturer of (among other things) electronic engine control systems. In addition to improved reliability and engine control, the new engines are EPA certified, which eliminates concerns about exhaust emissions compliance.
Agricultural engines have been required to meet EPA certification requirements since 2008, so the issue isn’t initial compliance, it’s ongoing compliance. The new control systems address that consideration head-on with their enhanced monitoring and control capabilities.
PERC was deeply involved in the development of the new engine line. According to Michael Newland, PERC’s director of agriculture business development, “Our overall mission is to promote safety, to look for additional business opportunities, and to help develop new uses and applications for propane. To that end, we often partner with manufacturers to assist with new product development and exposure.”
While PERC obviously has a vested interest in expanding propane use, it also has serious concerns about safety and reliability. It’s well documented that existing modes of power for agricultural applications (diesel and electric) often suffer from reliability problems, can be expensive, and may not be readily available.
According to Newland, “We’re excited about these new engines not only because they help advance the propane industry, but their control systems can help improve productivity because they require less maintenance and deliver more reliable operation. That translates to less downtime, so for irrigation, they spend more time pumping and less time shut down for repairs or adjustment. They’re also better for the environment. Propane is cleaner burning than diesel fuel or gasoline, and since these new engines meet the latest EPA certification requirements, they are especially clean running.”
Multi-Fuel Capability
Another advantage is that these engines can be switched from propane to natural gas with the flip of a switch. That means operators don’t have to shut down operation or engage in a lengthy switch-over if they need to change fuel sources.
That is obviously not a consideration at installations where propane is the only fuel source used. However, according to Jay Canada, Industrial-Irrigation’s vice president of sales and engineering, “There are quite a few farming operations that are located near natural gas pipelines, and that provides operators with a fueling option. Propane is the preferred fuel because it has a higher Btu content and that enables an engine to produce higher horsepower. However, multi-fuel capability is an advantage because it provides an option if propane is temporarily unavailable.”
Another reason for multi-fuel capability is that these engines are intended for additional uses beyond irrigation. Oil and gas production and power generation are two other applications for which these engines are ideally suited. When used for oil and gas production, the ability to switch fuels is especially attractive. Typically, when engines are used for pumping, they are started and run for a few days or weeks on propane. They aren’t switched over to wellhead gas until flow out of the ground is steady and reliable.
The Reliable Horsepower engines are based on existing GM architecture and, like their predecessors, incorporate components specifically designed for heavy-duty industrial use.
Impressive Torque
Horsepower ratings, which are a function of engine speed, are unimpressive as the advertised rating is at either 2800 or 3000 rpm. Torque is an entirely different situation as all engines generate impressive numbers at or below 2000 rpm. As an example, the 5.7-liter (350 cid) engine generates 437 lb/ft at 2000 rpm while the 10.3-liter (632 cid) version generates 798 lb/ft at 1200 rpm.
For pumping operations (such as with water, oil, or gas) torque is the relevant consideration—just as it is with a tractor or any other piece of farm equipment. Torque is an engine’s ability to overcome rotational resistance, such as that required by a pump. Horsepower is an engine’s torque output multiplied by engine speed. Internal combustion engines produce maximum torque at much lower rpm levels than maximum horsepower. Above the peak rpm point, torque decreases, although horsepower continues to increase—to a point—because of the engine speed multiplication factor.
Consequently, industrial engines, which operate under relatively constant and heavy loads, are designed to produce maximum torque at lower engine speeds.
The torque figures quoted are for engines fueled by propane. Output when fueled by natural gas is somewhat lower. As an example, the 10.3-liter engine produces 798 lb/ft of torque at 1200 rpm on propane, but only 723 lb/ft at 1800 rpm on natural gas. Obviously, propane is the better fuel as natural gas requires that an engine operate at higher speed to produce less power.
In addition to the five displacements currently available, Industrial-Irrigation Services plans to add both larger and smaller versions. According to Industrial-Irrigation’s Jay Canada, providing engines for irrigation system use is definitely not a one-size-fits-all proposition. “There are needs for a variety of engine sizes (power output levels), but, currently, there isn’t a wide variety of choices, so we will be expanding the Reliable Horsepower line. We’re looking at the needs of farms from sea level to 6000 to 8000 feet. The higher you go, the less power an engine will produce, so an engine that’s perfect for operation at sea level won’t produce sufficient power at high altitude. The distance you have to push water is another factor that affects power requirements, as is lift distance. Obviously, more power is required to pull water out of a 1000-foot well than to pump ground water. Once the variables involved are defined, we can specify an engine to meet a customer’s requirements.”
All Reliable Horsepower engines utilize the time-proven cast iron blocks and cylinder heads which are cast and machined in North America. Other components include aluminum intake manifolds, forged steel connecting rods, forged steel or nodular iron crankshafts, steel billet camshafts, and hydraulic roller valve lifters.
“Techies” might be surprised that all engines in the line incorporate cast iron blocks and heads and overhead valves, as opposed to aluminum castings and overhead cams. Reliability, cost, and application considerations are the major factors driving component selection. As noted, these engines are designed to operate at low speed, hence there is no advantage to an overhead cam configuration, which offers its advantages at high engine speeds. Additionally, overhead cam engines are much more expensive to repair or rebuild and failure of the cam drive system can result in significant engine damage.
Updated Fuel System
The actual hard parts that comprise a Reliable Horsepower engine have proven their reliability. What was needed was an updated fuel system that was equally reliable—and offered options made possible by recent technological developments. The new fuel system is therefore designed to conquer the most commonly encountered types of engine problems—failure to start, rough operation, and unexpected engine shut-down—that are typically a result of issues with the fuel delivery system.
It’s difficult to achieve reliable horsepower with an unreliable fuel system, and as the name implies, the new Reliable Horsepower engines are optimized to be reliable. For irrigation use, that means the engines run from the time they’re started until they’re turned off—with no stumbles.
To that end, Industrial-Irrigation Services partnered with Woodward Inc. to develop systems that offered both the required operational reliability and never-before-available control. These systems are also configurable to meet individual customer preferences, which include fuel type. All engines are bi-fuel capable, hence controls can be specified for propane-only, or multiple fuel types (propane, pipeline natural gas, wellhead gas).
The new fuel systems can be configured to allow the operator to flip a switch to change fuel type, or controls can be incorporated to enable the system to automatically switch fuel type if one runs out. Electronics also enable a number of other advantages.
All engines incorporate a throttle body-style of electronic fuel injection and include exhaust system oxygen sensors that monitor air/fuel ratio and pass it to the engine control module (ECM). In turn, the ECM makes whatever changes are necessary to maintain the desired air/fuel ratio. The ECM is programmable, thereby enabling operators to create custom calibrations to suit their particular operating environments.
That’s difficult to do with one-size-fits mechanical or non-programmable control systems. Conversely, the Reliable Horsepower systems not only continually optimize fuel and ignition settings to achieve maximum fuel economy and minimal exhaust emissions, the system can also be remotely monitored and controlled and even incorporates an emergency “kill switch.”
Remote Control, Monitoring
If you use your smartphone to lock or unlock your vehicle, monitor security cameras, or turn lights or appliances on or off, you’re already familiar with remote control and monitoring technology. Most commonly, that technology is implemented through use of the Internet of Things (IoT), which provides a means for “things” to communicate with each other. Remote monitoring and control provide a new level of safety and efficiency. All an operator has to do is pick up his or her cell phone to check engine speed, coolant temperature, oxygen sensor voltage, or a host of other sensors. The system can also store multiple calibrations so operation can be optimized for changes in operating environment (i.e high temperature/dry or cool temperature/wet). In spite of the sophistication of the control systems, they are designed to be user friendly.
Rather than having to stand right next to an engine, operators can use their cell phone from literally any part of the world with cell connectivity to monitor and control an engine. Remote control capability also opens new options for engine placement. The ability to remotely raise or lower engine speed, or to kill engine operation means that engine location can be optimized for operation rather than access.
In terms of in-the-field use, one of the greatest advantages of the Reliable Horsepower engine packages is summed up by a statement from Industrial-Irrigation Services: “All those trips to the north 40 to turn on or shut off the pumps can be a thing of the past with our fully electronic engine packages. We help you conserve both time and water with engine packages featuring remote start/stop and remote monitoring.”
The bottom line is that reliability leads to more productivity and increased profits, and that’s exactly what the Reliable Horsepower engine line is designed to deliver.
Dave Emanuel has written seven books and 2500 magazine articles covering a variety of topics ranging from automotive racing and performance modifications to political commentary. His automotive books and articles are informed by his hands-on background with engines and drivelines.