Monday, December 9, 2019
By Robert Battye…
The benefits of using tank monitors with forecasting, ticketing, routing, and truck computers to drive distribution efficiency and improve customer engagement are well understood. However, achieving reduced costs and customer terminations requires management awareness of inefficiencies, staff engagement in a change program, courage to operationalize savings by retiring bobtails, and, the focus of this article, intimate integration across systems and applications.
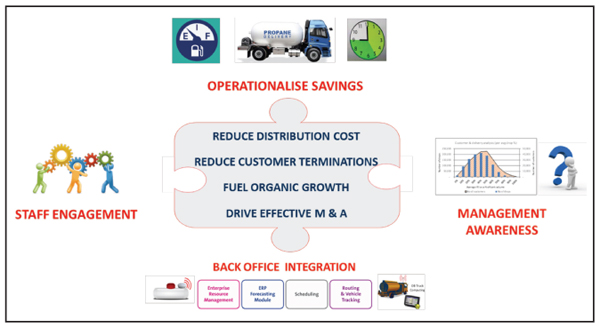
Typically, only the last reported level is imported into the back-office tank record to prompt manual ticket generation by operations staff. In many cases, monitor maintenance issues are not displayed on dispatch screens to at least make dispatchers aware that the monitor is no longer operational. The means of integration, the data structure and mechanisms for matching accounts and tanks between systems, differs from vendor to vendor, and often requires significant manual intervention to ensure the data is used effectively.
Advocating Change
The newest addition to the Anova family, Gaslog, like others in the industry, recognizes the opportunity to reduce the workload of operations staff, improve fill rates, increase truck productivity, and create a platform for new consumer engagement models through better integration across the systems propane distributors rely on. We have been quietly advocating for the development of advanced integration standards for several years and would welcome the opportunity of working with other vendors, including competitors, to agree upon and start the realization of a set of standards that would benefit our mutual customers.
While a tank monitor solution provider such as Gaslog, an Anova solution, can encourage and discuss change, it is more important that propane marketers advocate for this too. Everyone listens to their customer! In business transformation workshops, Gaslog details back office integration requirements and recommends progressing these with the relevant back office application and tank monitor vendors.
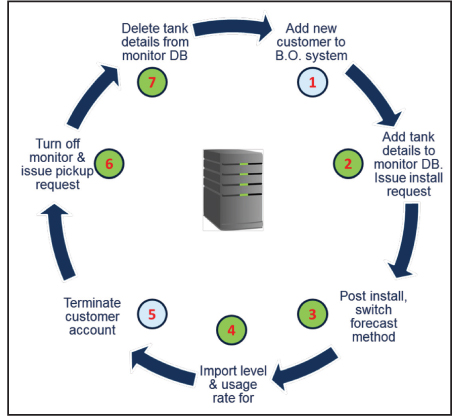
Other Industries
Standards have proven invaluable in other industries. Cellular technology vendors from chip manufacturers to base stations to cell tower receivers to routers and switches, the key to monitoring and truck computing, mobile phones, and much, much more, must adhere to the agreed global 3GPP standards in order to enable the worldwide calls, SMS’s, and data transfer we now take for granted.
There are a lot of standards that have come into existence, either agreed upon by vendor groups (e.g., XML in data exchange) or determined by a user industry wanting to focus more on their core business and less on integrating disparate systems (e.g., OPC-UA in industrial automation).
As the technology suppliers, we have an exciting opportunity to collectively increase the “off the shelf” benefit of the systems, services, and products provided to the industry we serve. Today, each of us decides what, how, when, and why to integrate. However, with the rapid increase in the use of data-driven logistics, it would help the propane industry and the vendors if there were an agreed set of standards that vendors could respond to.
The use of tank monitors may have reached an inflection point, with rapid growth in the last three years very much in evidence. The expansion of tank monitoring is expected to follow the “S-curve” seen in the adoption of other technologies; it begins with a small number of “early adopters,” moves into a period of accelerated growth as technology is adopted by “followers,” and culminates in slower growth as a saturation point is reached and “laggards” follow suit.
Gaslog estimates 8% of bulk tanks are monitored in the U.S., but that number is rising rapidly as evidenced by double-digit growth in monitor sales and the number of new monitor suppliers in the market. This growth is being driven by greater value and industry challenges.
Tank monitoring’s total cost of ownership continues to fall while reliability and battery life continue to rise. Total cost of ownership includes capital depreciation, monthly fees, and installation cost. While a cellular-based system is cost effective for up to 30% of tanks, we are entering the industry 4.0 era, facilitating a trend towards automation and data exchange with Internet of Things (IoT) costs falling further, driving effective ROI for more than 60% of propane tanks.
At the same time, the need for the delivery efficiency is increasing. The number of gallons supplied has been contracting each year; the cost of delivery has increased; demand and weather patterns have become less predictable; and the cost of propane has grown more volatile with changes in global demand. For propane marketers, reducing the cost of delivery and customer churn for increased profitability is critical to meeting these challenges.
Gaslog has accumulated more than 6 million propane delivery records working with propane distributors on logistics transformation. This data shows an average fill without monitoring of 42% of water volume and an average fill with monitoring of 53%. With better integration between monitors, back-office software, and onboard truck computing systems, an average fill of 60% with improved truck productivity (e.g., 3000-plus drops per year) should be achievable. At that point, propane marketers can dramatically reduce their costs by operating fewer bobtails and needing fewer drivers, a scarce resource.
Reducing Time to Benefit
The time it takes to achieve these benefits could be reduced if there were a standardized level of integration. Tank monitors would be an even more powerful tool in a propane distributor’s arsenal if dispatchers, drivers, and back-office staff could take the information for granted and rely on systems to make sensible decisions and recommendations (e.g., deliver gas to a customer with more propane but a higher usage rate than someone with less gas and two weeks remaining). They could automatically switch back to k-factor forecasting if the monitor is unable to report for several days, or generate a work order for monitor deployment after marking an account as a telemetry target. These automated interactions between systems are taken for granted in many other industries.
Advanced integration could automate the management of a new customer from onboarding to termination. Manual back-office functions such as re-entering customer details in multiple systems could be eliminated; sophisticated level history, usage rates, and forecasting algorithms could combine to improve delivery efficiency and truck optimization; and monitor productivity would improve through integration with service management systems, generating a monitor and tank installation ticket. A diagram on this page shows manual steps in blue and potentially automated steps in green.
If you have to rekey customer data, manually associate a monitor with the target tank, log into different systems, and issue verbal or email instructions to technicians, it creates a lot of work, causes mistakes, and ultimately results in monitor productivity falling and distrust of the data. If the data exchange and workflow are automated, operations can focus on their core tasks of forecasting, scheduling, and routing, and drivers can concentrate on delivery, both trusting the systems and leveraging “data” as a part of their day-to-day work.
Given the limited data involved, it shouldn’t be hard to develop some basic standards to deliver an improved level of integration and data exchange that could evolve and improve over time.
Technology can play a key role in driving productivity in distribution, improving profitability and cash flow, and creating space for competitive strategies that increase the attractiveness of propane to a changing customer demographic. To get there, you need off-the-shelf integration across distribution, customer engagement, and supply chain systems, knowing that changing out one tank monitor or back-office system for another does not require substantial reinvestment in integration to maintain and improve your business’s efficiency.
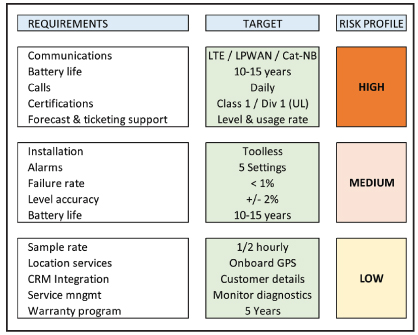
Evaluation Criteria
In the absence of standards, propane distributors can ask us, the vendors, how our systems integrate with others and detail decision criteria when selecting tank monitors and systems.
Distributors need to prioritize features and benefits that are important to them, perhaps breaking them down into high, medium, and low priority requirements; setting targets; and using these to compare competitive systems and products.
Overarching requirements should include the required systems interfaces that will facilitate intimate integration in the future when 30% to 60% of tanks are monitored; data security standards to meet growing consumer concerns over privacy and statutory regulations; and application and network reliability, knowing in the dead of winter, your ability to deliver propane depends on your systems being up.
Some requirements are easily evaluated and well understood by the buyer. These might include the life span of the battery; the frequency of calls; the level of safety certification; and the forecasting and ticketing APIs for level and usage-rate. External advice may be needed for other requirements, particularly when it comes to security, integration standards, and communications. The 2G GSM sunsetting was a lesson well learned by vendors and customers alike.
Conclusion
By choosing systems with a long life span and a commitment to back office integration beyond today’s typical exchange of level data, propane marketers can maximize the benefits of tank monitoring, as well as their investment in back-office systems and truck computers, to leverage what is possible today while simultaneously planning for a future in which the IT systems carry more of the workload. This will further reduce the number of runouts and improve engagement with the end-gas consumers, generating stronger customer loyalty, and potentially halving the direct cost of delivering propane.
Robert Battye has more than 30 years’ of project and executive management experience in IT, the last 12 working with propane companies as vice president North America and COO of Gaslog, a leading tank monitoring solution provider, which recently announced its merger with Anova. He can be contacted at This email address is being protected from spambots. You need JavaScript enabled to view it..
The benefits of using tank monitors with forecasting, ticketing, routing, and truck computers to drive distribution efficiency and improve customer engagement are well understood. However, achieving reduced costs and customer terminations requires management awareness of inefficiencies, staff engagement in a change program, courage to operationalize savings by retiring bobtails, and, the focus of this article, intimate integration across systems and applications.
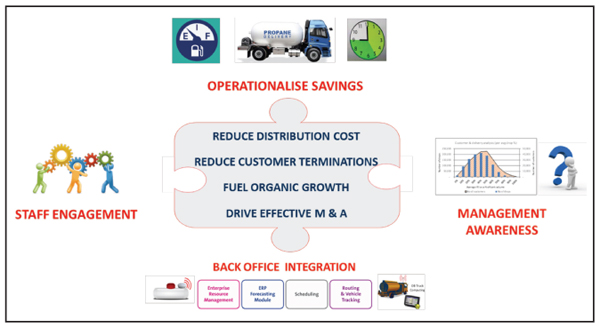
Typically, only the last reported level is imported into the back-office tank record to prompt manual ticket generation by operations staff. In many cases, monitor maintenance issues are not displayed on dispatch screens to at least make dispatchers aware that the monitor is no longer operational. The means of integration, the data structure and mechanisms for matching accounts and tanks between systems, differs from vendor to vendor, and often requires significant manual intervention to ensure the data is used effectively.
Advocating Change
The newest addition to the Anova family, Gaslog, like others in the industry, recognizes the opportunity to reduce the workload of operations staff, improve fill rates, increase truck productivity, and create a platform for new consumer engagement models through better integration across the systems propane distributors rely on. We have been quietly advocating for the development of advanced integration standards for several years and would welcome the opportunity of working with other vendors, including competitors, to agree upon and start the realization of a set of standards that would benefit our mutual customers.
While a tank monitor solution provider such as Gaslog, an Anova solution, can encourage and discuss change, it is more important that propane marketers advocate for this too. Everyone listens to their customer! In business transformation workshops, Gaslog details back office integration requirements and recommends progressing these with the relevant back office application and tank monitor vendors.
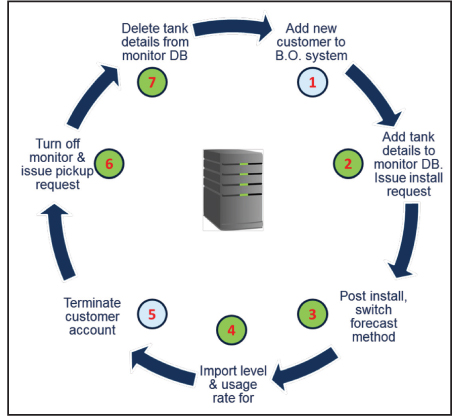
Other Industries
Standards have proven invaluable in other industries. Cellular technology vendors from chip manufacturers to base stations to cell tower receivers to routers and switches, the key to monitoring and truck computing, mobile phones, and much, much more, must adhere to the agreed global 3GPP standards in order to enable the worldwide calls, SMS’s, and data transfer we now take for granted.
There are a lot of standards that have come into existence, either agreed upon by vendor groups (e.g., XML in data exchange) or determined by a user industry wanting to focus more on their core business and less on integrating disparate systems (e.g., OPC-UA in industrial automation).
As the technology suppliers, we have an exciting opportunity to collectively increase the “off the shelf” benefit of the systems, services, and products provided to the industry we serve. Today, each of us decides what, how, when, and why to integrate. However, with the rapid increase in the use of data-driven logistics, it would help the propane industry and the vendors if there were an agreed set of standards that vendors could respond to.
The use of tank monitors may have reached an inflection point, with rapid growth in the last three years very much in evidence. The expansion of tank monitoring is expected to follow the “S-curve” seen in the adoption of other technologies; it begins with a small number of “early adopters,” moves into a period of accelerated growth as technology is adopted by “followers,” and culminates in slower growth as a saturation point is reached and “laggards” follow suit.
Gaslog estimates 8% of bulk tanks are monitored in the U.S., but that number is rising rapidly as evidenced by double-digit growth in monitor sales and the number of new monitor suppliers in the market. This growth is being driven by greater value and industry challenges.
Tank monitoring’s total cost of ownership continues to fall while reliability and battery life continue to rise. Total cost of ownership includes capital depreciation, monthly fees, and installation cost. While a cellular-based system is cost effective for up to 30% of tanks, we are entering the industry 4.0 era, facilitating a trend towards automation and data exchange with Internet of Things (IoT) costs falling further, driving effective ROI for more than 60% of propane tanks.
At the same time, the need for the delivery efficiency is increasing. The number of gallons supplied has been contracting each year; the cost of delivery has increased; demand and weather patterns have become less predictable; and the cost of propane has grown more volatile with changes in global demand. For propane marketers, reducing the cost of delivery and customer churn for increased profitability is critical to meeting these challenges.
Gaslog has accumulated more than 6 million propane delivery records working with propane distributors on logistics transformation. This data shows an average fill without monitoring of 42% of water volume and an average fill with monitoring of 53%. With better integration between monitors, back-office software, and onboard truck computing systems, an average fill of 60% with improved truck productivity (e.g., 3000-plus drops per year) should be achievable. At that point, propane marketers can dramatically reduce their costs by operating fewer bobtails and needing fewer drivers, a scarce resource.
Reducing Time to Benefit
The time it takes to achieve these benefits could be reduced if there were a standardized level of integration. Tank monitors would be an even more powerful tool in a propane distributor’s arsenal if dispatchers, drivers, and back-office staff could take the information for granted and rely on systems to make sensible decisions and recommendations (e.g., deliver gas to a customer with more propane but a higher usage rate than someone with less gas and two weeks remaining). They could automatically switch back to k-factor forecasting if the monitor is unable to report for several days, or generate a work order for monitor deployment after marking an account as a telemetry target. These automated interactions between systems are taken for granted in many other industries.
Advanced integration could automate the management of a new customer from onboarding to termination. Manual back-office functions such as re-entering customer details in multiple systems could be eliminated; sophisticated level history, usage rates, and forecasting algorithms could combine to improve delivery efficiency and truck optimization; and monitor productivity would improve through integration with service management systems, generating a monitor and tank installation ticket. A diagram on this page shows manual steps in blue and potentially automated steps in green.
If you have to rekey customer data, manually associate a monitor with the target tank, log into different systems, and issue verbal or email instructions to technicians, it creates a lot of work, causes mistakes, and ultimately results in monitor productivity falling and distrust of the data. If the data exchange and workflow are automated, operations can focus on their core tasks of forecasting, scheduling, and routing, and drivers can concentrate on delivery, both trusting the systems and leveraging “data” as a part of their day-to-day work.
Given the limited data involved, it shouldn’t be hard to develop some basic standards to deliver an improved level of integration and data exchange that could evolve and improve over time.
Technology can play a key role in driving productivity in distribution, improving profitability and cash flow, and creating space for competitive strategies that increase the attractiveness of propane to a changing customer demographic. To get there, you need off-the-shelf integration across distribution, customer engagement, and supply chain systems, knowing that changing out one tank monitor or back-office system for another does not require substantial reinvestment in integration to maintain and improve your business’s efficiency.
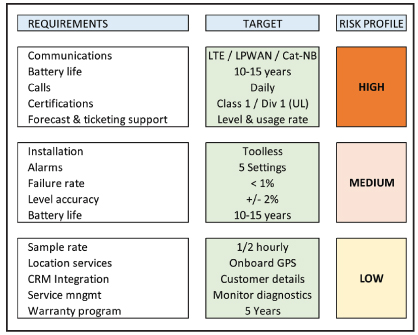
Evaluation Criteria
In the absence of standards, propane distributors can ask us, the vendors, how our systems integrate with others and detail decision criteria when selecting tank monitors and systems.
Distributors need to prioritize features and benefits that are important to them, perhaps breaking them down into high, medium, and low priority requirements; setting targets; and using these to compare competitive systems and products.
Overarching requirements should include the required systems interfaces that will facilitate intimate integration in the future when 30% to 60% of tanks are monitored; data security standards to meet growing consumer concerns over privacy and statutory regulations; and application and network reliability, knowing in the dead of winter, your ability to deliver propane depends on your systems being up.
Some requirements are easily evaluated and well understood by the buyer. These might include the life span of the battery; the frequency of calls; the level of safety certification; and the forecasting and ticketing APIs for level and usage-rate. External advice may be needed for other requirements, particularly when it comes to security, integration standards, and communications. The 2G GSM sunsetting was a lesson well learned by vendors and customers alike.
Conclusion
By choosing systems with a long life span and a commitment to back office integration beyond today’s typical exchange of level data, propane marketers can maximize the benefits of tank monitoring, as well as their investment in back-office systems and truck computers, to leverage what is possible today while simultaneously planning for a future in which the IT systems carry more of the workload. This will further reduce the number of runouts and improve engagement with the end-gas consumers, generating stronger customer loyalty, and potentially halving the direct cost of delivering propane.
Robert Battye has more than 30 years’ of project and executive management experience in IT, the last 12 working with propane companies as vice president North America and COO of Gaslog, a leading tank monitoring solution provider, which recently announced its merger with Anova. He can be contacted at This email address is being protected from spambots. You need JavaScript enabled to view it..