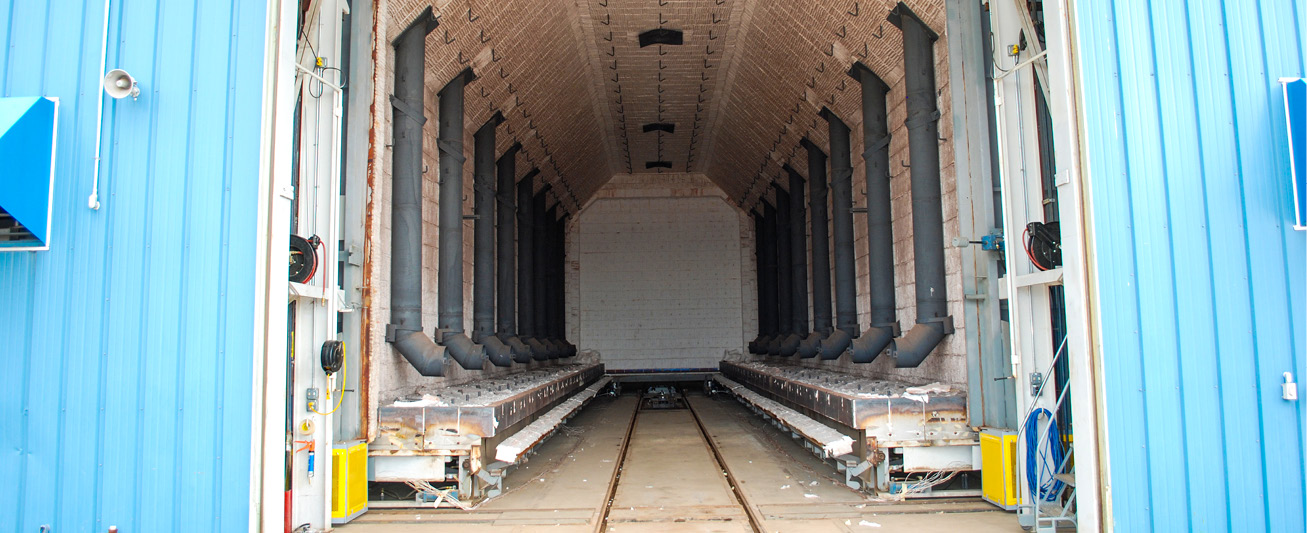
As it says in the title, bobtail cargo tank stretching has become a thing of the past. Why? Ahead, we’ll give reasons to explain this shift.
Background
For background on our experience, Arrow Tank and Engineering, a cargo tank manufacturer approaching 68 years of serving the propane industry, holds both a U-stamp for newly manufactured vessels and an R-stamp for repairs and major modifications that include tank stretches. With our experience in building new vessels, our history of performing modifications and alterations on older tanks might not be as well-known. Tank stretches were much more common 20 years ago, but they have now largely become a thing of the past for numerous reasons.
Overall Length
Most tank candidates considered for a stretch tend to be older vessels that are 73 inches in diameter. Stretching these to a desirable capacity such as 3,200 gallons results in an overall length that is 26 inches longer than a 3,200-gallon tank that is built 80 inches in diameter. Consequently, the chassis wheelbase must be substantially longer (perhaps 18 inches or more) for proper weight distribution. The longer wheelbase directly impacts maneuverability, making a big difference in tight spaces, such as high destiny residential and/or congested commercial areas.
Documentation, Material & Design Specifications
As mentioned, the smaller tanks to be repurposed are also more likely to be older, where the ability to produce proper documentation and design specifications will likely impact the decision to stretch. First and foremost, to be a legitimate MC-331 cargo tank, the owner must have the MC-331 Certificate of Compliance from the vessel manufacturer and form U-1A manufacturer’s data report for pressure vessels. If a form U-1A is missing and is no longer available from the manufacturer, it can sometimes be obtained through the National Board of Pressure Vessels. However, the certificate of compliance can sometimes be more difficult to produce, especially if the manufacturer no longer has a copy or is no longer in business.
Material specifications are also a factor. SA202 material specs will always be a five-year hydrostatic test cycle. Forget about anything else you read, such as obtaining “Charpy impact tests reports,” because they were never required to be documented by the manufacturer, and the material for these tanks never met the requirements of a “full-sized specimen.” Additionally, nozzle arrangement on rear head, outlet flange location, bottom drain, baffle(s), minimum thickness weld buildup, etc., may need to be modified/altered to accommodate the new build.
Another requirement in the code states that the design of the stretched cargo tank must meet the specifications in effect at the time such work is performed. Therefore, if your tank does not have a manway, it needs to be added as part of the process.
Cost Prohibitive
The process involves stripping everything from the cargo tank, which means you are starting from scratch and then some. By comparison, the preparation, transportation, repair/modification labor and material costs begin to approach the threshold of buying a new bobtail vessel. Keep in mind the true condition of the tank is not known until you cut the tank into two pieces, especially in the event no manway exists. The real kicker is that discovering findings that render the tank as scrap may not be known until $7,500 worth of transportation and work in process has been completed.
Transport Vessel Construction & Post Weld Heat Treatment
Arrow Tank and Engineering also hosts a post weld heat treatment (PWHT) furnace on-site at the plant in Cambridge, Minnesota. PWHT is a process used to ensure the material properties of the components are retained after welding and forming. PWHT reduces residual stress as a method of hardness control while enhancing material ductility and corrosion resistance, thus improving the lifespan of the vessel. The process is a crucial step in manufacturing various vessels, including LPG and NH3 transport vessels.
Our furnace has a maximum capacity of 18 feet in diameter by 110 feet long and up to 280 tons in weight. The furnace is fully configurable into three different furnace spaces with a maximum temperature of 1,700° F coming from the 48 million Btu capacity.
As for transport vessels, the manufacturing process is quite interesting and much different than bobtail cargo tanks. Here is the condensed version on how it differs between bobtail and transport vessels:
Bobtail cargo tanks are most often comprised of SA-612 material that is non-quenched and tempered (NQT). This material is formed/welded and then undergoes non-destructive evaluation (NDE), such as phased array or X-ray, to thoroughly inspect welds for flaws like cracks, lack of fusion or pitting. Once that process is complete, the integrity is verified via hydro test at 375 psi.
On the other hand, transport material is most often comprised of SA-517 that is quenched and tempered (QT). This is a high tensile-strength material that allows thinner material to save weight but also has a variety of processes required to ensure the material is safe when the manufacturing process is complete. The construction process is more specific as it relates to weld procedures, weld finish, attachments and NDE requirements.
Like bobtails, the vessel undergoes phased array or X-ray, but it then requires a few additional steps before and after hydro test.
Next, all welds internally and externally must be examined for conformance to crown height and by magnetic particle testing (MPT). MPT uses a magnetic particle along with a contrast color to locate surface defects that may not have been discovered by the naked eye. Once the surfaces are evaluated and confirmed free of cracks/defects, it’s time for a cook in the oven.
Preparation for PWHT involves loading the vessel on a specially designed cart and then attaching various probes on the tank to monitor the wall temperature. The process conforms to ASME code and is performed with the concurrence of an authorized inspector. The rate of heat input above 800° F is not more than 100° F every 15 minutes. Holding time must be at least one hour per inch of shell thickness, but generally not less than 30 minutes. The holding temperature is normally 1,075° F and usually allowed to air cool when completed.
Following PWHT is verifying the integrity of vessel and welded attachments to the pressure boundary via hydro test. New vessel construction for QT tanks built according to ASME Section VIII, Division 1 must be tested at 2-times working pressure, or 500 PSI.
With the hydro completed, the vessel is subjected to another round of magnetic particle testing. Pressurizing vessels during hydro test procedure purposely causes the material to stretch. One last round of MPT after hydro is a final check to assure all welds meet the specifications and performance requirements per ASME and MC-331 Code. Following these detailed procedures mitigates risk and ensures safe use of pressure vessels as they travel our roadways.