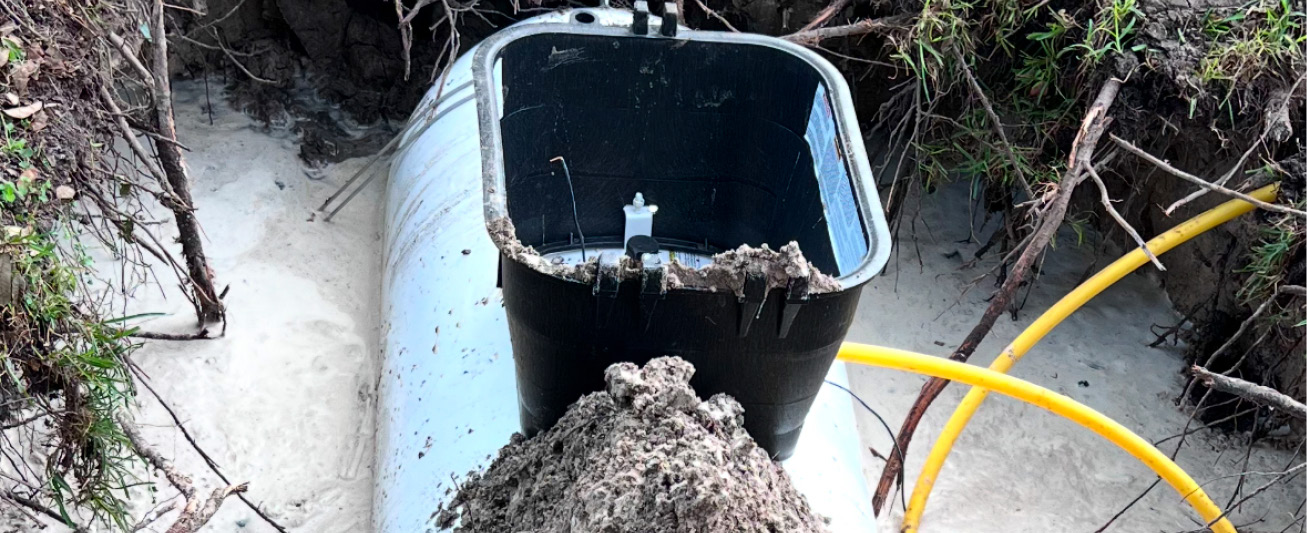
Propane tank installation in coastal areas can be a challenge at times. In Florida, for example, there are over 7,700 named lakes that are larger than 20 acres. One of the most well-known lakes in Florida includes Lake Okeechobee, the second-largest freshwater lake in the United States. Along with lakes, Florida has over 50,000 streams, rivers, canals and coastal plains, along with 76,000 stormwater retention ponds. Therefore, “waterlogged” tanks are a real issue here. Most municipalities require propane tank anchoring on underground tanks; however, in high water table areas, this is just not enough. Most areas of our state are even requiring aboveground tanks to be anchored and secured due to potential flooding. With the recent hurricanes in the Southeast, this is starting to become not only a state issue but an entire regional issue that needs to be taken into consideration when choosing a proper location for coastal propane tank installation.
Challenges of Propane Tank Installation in Coastal Areas
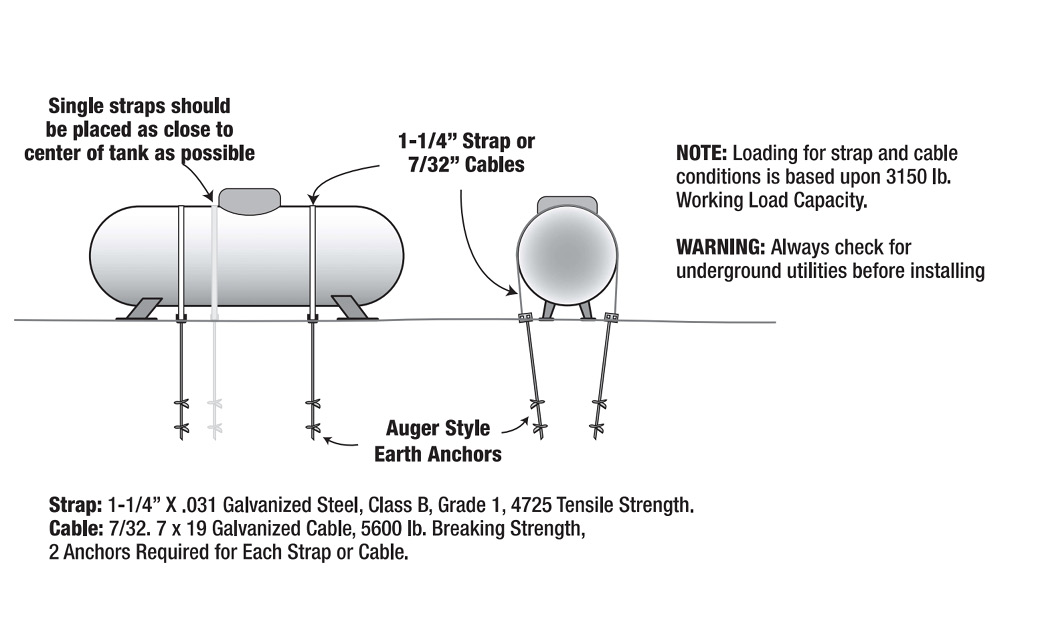
Buoyancy is the overall issue with the potential of a tank coming out of the ground. If the water table rises above the liquid level in the tank and there are no measures in place to protect it, the tank will “pop” out of the ground. Nothing will get a customer screaming quicker than seeing their newly installed tank coming out of the ground like a submarine breaching the surface of their lawn.
Best Practices for Propane Tank Installation & Anchoring
When looking for an ideal location for coastal propane tank installation, we review site surveys, property boundaries and historical flood levels and flood zones when deciding on tank placement. Even after reviewing these items, sometimes it may still not be enough. As we start excavating for the tank burial and find water in the base of the hole, we need to make decisions on whether we want to proceed with the underground option or move the tanks aboveground. If we proceed with the underground option, the tank will need to be anchored into the base of the hole and filled with propane quickly to help weigh down the tank. Sometimes, even after doing all those measures, the tank could still float out of the ground if the water table is at an extremely elevated level. We have had some rare conditions where we will prefabricate a concrete “buoyancy” pad at our shop, then bring it out to the customer location and be forced to anchor the tank to the pad in the hole for extra weight. Subpumps are used to keep water out of the hole while we are preparing for these types of intricate propane tank installations.
Even older systems that were not anchored to begin with can create issues throughout the year. If an existing system runs low or out of gas during our rainy season, tanks are prone to “pop” out of the ground. This forces us to either reinstall with a propane tank anchoring system or consider other options for the system. As we continue to build housing developments and neighborhoods, spacing on properties and tank placement options are few and far between with tighter lot lines.
Dealing With Corrosion in Coastal Environments
Along with the risk of tanks coming out of the ground in wet conditions, we also have cathodic protection as a strong concern. One in the industry would just think, “Slap an anode on your underground tank and you’re good, right?” With marshy or waterlogged conditions, we will need to upsize or add extra anodes to protect our assets. Proper anode sizing for the type of conditions that you are in is a key role, as well. Sizing tells you that a 250-gallon tank should be good with a 9-pound anode. However, if we are installing propane tanks in a marshy or waterlogged area, we would want to increase to a 17-pound anode to keep this asset protected as long as possible. Regular and periodic testing of the anode and the tank are also key to fulfilling the life of the unit to its fullest extent.
When we start getting closer to our coastal regions, studies show that salt water has effects 30-50 miles inland. At times, intercoastal waterways will extend inward, as well. In locations other than this, we typically would say keep it propane tank installations aboveground. However, in these harsh, salty conditions, tanks tend to corrode more quickly aboveground; therefore, we are forced to go the underground route to try and attempt to protect the steel from environmental factors. The average lifespan that we see on tanks here in a coastal area (without preventative maintenance) is less than five years.
Improving Long-Term Maintenance & Protection for Propane Tanks
Protecting your assets — whether above- or underground — in potential “waterlogged” locations play a key role for business in the Southeast. We have seen tanks float out to sea in Florida within the direct coastal areas. Others in the Southeast have seen landslides and rivers take their tanks away. While the National Fire Protection Association’s boundary lines are a good starting point, we need to consider Mother Nature to find the safest spot to install propane tanks.