Friday, November 11, 2016
By David Kidd…
As the propane industry continues to expand and evolve, the technology designed to enable better information gathering and customer service follows suit. In this rapidly transforming environment, propane delivery companies are starting to adapt in an effort to better serve their customers and provide products in a more effective and trackable way.
Technical advances are made each year to accommodate the evolution of the propane industry. New top-notch technologies continue to surface, with many providing user-friendly interfaces.
Staying on top of demand in today’s distribution chain is challenging. Stock-outs can be costly and lead to lost business. In addition, transportation expenses and delivery logistics can be hard to manage, particularly around emergency deliveries. Monitors on tanks can be inconsistent and unreliable, with a lot of time being spent to get them into working order.
So what should propane delivery companies look for in a product and what features? When choosing equipment, companies should determine their current challenges, evaluate the options, and select the one that best meets their needs.
Having the right information at the right time can help companies better schedule and dispatch truck fleets and drivers, as well as reduce fuel costs through more efficient pickups and deliveries. Products such as remote monitoring solutions can provide users with up-to-date inventory information, help to eliminate costly stock-outs and emergency deliveries, and better understand production changes. This can boost the bottom line and provide more accurate forecasting of inventory and usage changes.
Products are also available that offer better radio strength and communicate via cellular technology to ensure the best solution for any application and can help streamline processes that will result in better profit margins.
Monitors offer a variety of options including a GPS feature that enables companies to put the units onto moveable assets to not only track inventory levels, but also location. Additionally, they can remotely set reporting schedules and level alarms to suit their application and provide a consistent overview of assets. This simple compilation of data allows professionals to have all the information they need to make the best business decisions.
Equipment innovations have evolved with new Web capabilities. Users can access up-to date information that supports the best delivery and supply decisions. Monitoring solutions with this component can enhance delivery planning and performance tools for efficient practices. This innovative Web feature allows users to track progress, give a more detailed inventory forecast, and deliver most efficiently.
Web access can provide other benefits for industry professionals, including the elimination of run-outs and the ability to access detailed graphical and tabular reports. Dealers can use active text or email alerts to keep teams proactively on top of changing tank levels. As technology has evolved, these innovative tracking solutions manage data via cellular connection, allowing companies to actively track levels as well as the timing and location of asset deliveries.
By eliminating inefficient manual order creation and scheduling, monitoring technologies can also reduce the amount of time a dispatcher must spend in order to establish delivery schedules. When special circumstances or last-minute orders arise, manual adjustments can be made as needed.
Technological innovations can significantly streamline the complicated delivery optimization process. On average, companies will experience a 50% increase in the amount delivered and 33% fewer stops. Helping dispatchers determine which tanks to fill now and which to fill later can minimize total costs while maximizing asset utilization. What once took hours of educated guessing and research to achieve can now be done in less than 10 minutes. Industry modernizations allow businesses and monitoring teams to focus their efforts on other important tasks.
(David Kidd is Centeron product manager, global solutions, for Schneider Electric)
As the propane industry continues to expand and evolve, the technology designed to enable better information gathering and customer service follows suit. In this rapidly transforming environment, propane delivery companies are starting to adapt in an effort to better serve their customers and provide products in a more effective and trackable way.
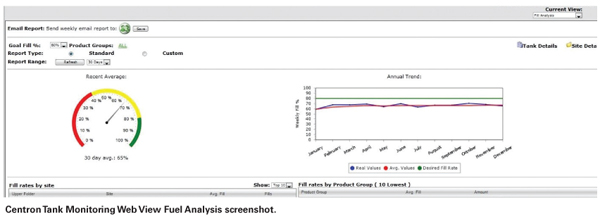
Technical advances are made each year to accommodate the evolution of the propane industry. New top-notch technologies continue to surface, with many providing user-friendly interfaces.
Staying on top of demand in today’s distribution chain is challenging. Stock-outs can be costly and lead to lost business. In addition, transportation expenses and delivery logistics can be hard to manage, particularly around emergency deliveries. Monitors on tanks can be inconsistent and unreliable, with a lot of time being spent to get them into working order.
So what should propane delivery companies look for in a product and what features? When choosing equipment, companies should determine their current challenges, evaluate the options, and select the one that best meets their needs.
Having the right information at the right time can help companies better schedule and dispatch truck fleets and drivers, as well as reduce fuel costs through more efficient pickups and deliveries. Products such as remote monitoring solutions can provide users with up-to-date inventory information, help to eliminate costly stock-outs and emergency deliveries, and better understand production changes. This can boost the bottom line and provide more accurate forecasting of inventory and usage changes.
Products are also available that offer better radio strength and communicate via cellular technology to ensure the best solution for any application and can help streamline processes that will result in better profit margins.
Monitors offer a variety of options including a GPS feature that enables companies to put the units onto moveable assets to not only track inventory levels, but also location. Additionally, they can remotely set reporting schedules and level alarms to suit their application and provide a consistent overview of assets. This simple compilation of data allows professionals to have all the information they need to make the best business decisions.
Equipment innovations have evolved with new Web capabilities. Users can access up-to date information that supports the best delivery and supply decisions. Monitoring solutions with this component can enhance delivery planning and performance tools for efficient practices. This innovative Web feature allows users to track progress, give a more detailed inventory forecast, and deliver most efficiently.
Web access can provide other benefits for industry professionals, including the elimination of run-outs and the ability to access detailed graphical and tabular reports. Dealers can use active text or email alerts to keep teams proactively on top of changing tank levels. As technology has evolved, these innovative tracking solutions manage data via cellular connection, allowing companies to actively track levels as well as the timing and location of asset deliveries.
By eliminating inefficient manual order creation and scheduling, monitoring technologies can also reduce the amount of time a dispatcher must spend in order to establish delivery schedules. When special circumstances or last-minute orders arise, manual adjustments can be made as needed.
Technological innovations can significantly streamline the complicated delivery optimization process. On average, companies will experience a 50% increase in the amount delivered and 33% fewer stops. Helping dispatchers determine which tanks to fill now and which to fill later can minimize total costs while maximizing asset utilization. What once took hours of educated guessing and research to achieve can now be done in less than 10 minutes. Industry modernizations allow businesses and monitoring teams to focus their efforts on other important tasks.
(David Kidd is Centeron product manager, global solutions, for Schneider Electric)