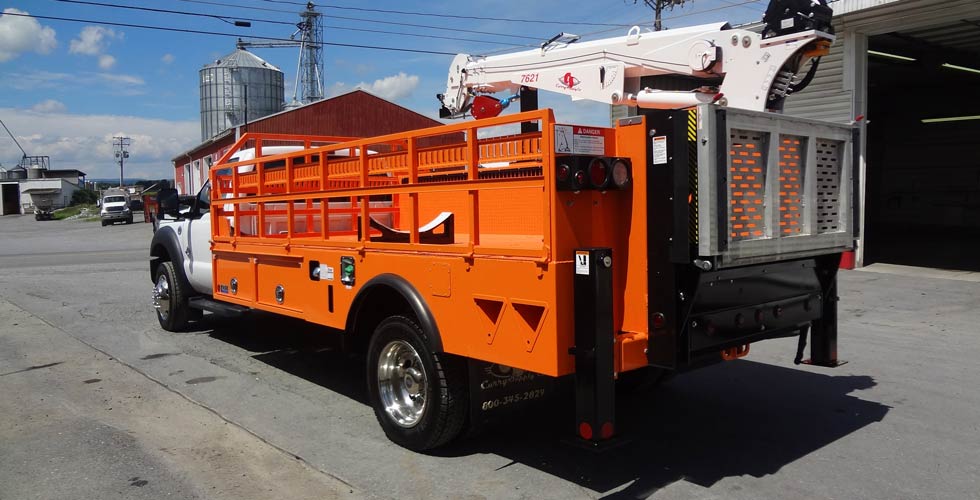
When the BPN team attended the Western Propane Gas Association’s 2021 convention in Reno, Nevada, earlier this year, one thing we heard over and over again was concern over an increasing need for qualified drivers and equipment operators. And, unfortunately, a potential side effect of this specific strain on the labor market relates to safety: As propane marketers are forced to make do with what — and, more importantly, who — they have, safety precautions can fall to the wayside, resulting in potentially hazardous situations.
This month, BPN caught up with Jeff Shaw, vice president of sales and marketing for Curry Supply, to discuss how leadership teams can help drive safe operations on and around propane service trucks. Shaw has 14 years of experience working in the truck and equipment industry. Read his insights and advice below.
What emerging trends or new features on service trucks have made the most significant impact to operators’ processes over the past five years?
A big influence has been the advancement in crane controls and aluminum bodies. Our partner in service trucks, Stellar Industries, has developed the CDTplus radio remote for service cranes that allows operators to know the actual weight they are picking. As the crane gets closer to maximum capacity, the crane remote will vibrate at a great cycle rate.
This is a huge productivity tool that keeps operators in the normal operating range of the crane. Stellar has also created the first aluminum mechanics and LP crane bodies with aluminum compartments while maintaining a steel crane support. This combination saves a few hundred pounds in weight to allow operators greater carrying capacity.
Do any of those features help the operator do their job more safely?
The radio remote increases operator safety by actually communicating with the operator what capacity is left on the crane. In addition to the current load on the crane, it will also tell the operator what the maximum distance is that they can move the load. This helps the operator stay away from a max load situation and a possible overload shutdown. The system also incorporates a feature that temporarily increases the crane’s capacity to alleviate an overload situation. All of this is done within the design limits of the crane in order to help the operators be as safe as possible.
What are the advantages for propane marketers of customizing service trucks?
Some people will find that customizing their service truck meets a special requirement for an operator. Some operators may do special work and need to increase tool storage or make larger storage areas for tubing or hardware. However, customizing too much can be a drawback for propane fleet management.
The cost of customization may or may not be justified unless the customization helps with a majority of the tasks to be performed by the truck and operator. Additionally, we found the resale value of custom modifications to a service truck doesn’t hold up as well as trucks with standard components.
Can you describe some of the customization options available from most manufacturers?
Custom modifications can range from a total custom body with different body lengths or compartment depths — although, most custom items center around internal compartment storage, such as drawer sets and bolt bins for tools and parts storage.
It’s also common to add generators or power inventors to run power tools and charge cordless tool batteries. We are also finding utilization of all-in-one power units more common. This allows the operator to utilize hydraulic components without running the truck engine, which saves fuel and reduces emissions.
What are the most common safety issues you see when it comes to preventive maintenance for propane service trucks?
Preventive maintenance safety issues are usually centered around crane inspections. Each service crane used in propane or any other market is required to have daily, monthly, quarterly and annual inspections. These tools lift a considerable amount of weight, and there are wear components that need to be inspected, serviced and replaced as needed. We find that few customers do all the required inspections.
What about operations?
Operational safety concerns we see are the lack of crane operator and rigger or rigging training for crane operators. The Occupational Safety and Health Administration now requires a crane operator certification for cranes with greater than 2,000-pound capacity. Operators need to do a better job of understanding crane operation and rigging to ensure they don’t damage property or people.
How can leadership teams or fleet managers put processes in place to prevent some of these issues?
It’s up to leadership to place more importance on safety, inspection and training. It must become part of the culture. Regularly review inspection logs. Make operator training part of regularly scheduled toolbox talks or standing meetings. We have tools available to help facilitate training, from visits by regional sales personnel to conduct a product demonstration to a video library showing proper crane operation.