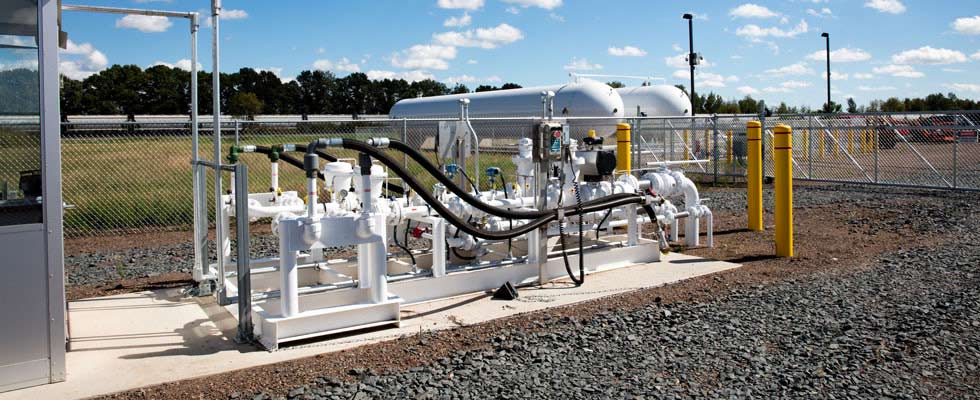
In today’s economy, regardless of what you are supplying, it’s a challenge. A little over two years ago, we were all living in a world in which we could get almost anything we wanted in a day or less. COVID-19 very quickly uncovered the weaknesses of our supply chain.
With the sudden behavioral and purchasing habit changes, the problems that always existed were exacerbated and became out of control at a pace no one could have predicted.
It was the start to the major disruption — one that has continued to unfold — causing us all to adjust to a new normal of shortages all over the world, with new challenges each day. Regardless of whether you are a manufacturer, supplier, retailer or end user, we are all affected.
From a manufacturer’s standpoint, one of the most challenging aspects of the supply chain crisis is the frequency and variation of material delays. One day the problem is raw materials and allocation. The next, the challenge may be a steep price increase.
We are working through doing business with the inability to get chassis, which can be absolutely crippling for some manufacturers/upfitters. We’ve experienced major lead time changes with everyday products, such as meters, or suddenly we can’t get a hose reel, and so on. We are doing the best we can and constantly adjusting production schedules to work with the shortages.
Many of us have adjusted our inventory levels, carrying more than we ever have, which can create its own set of challenges — tying up dollars that could be used on other items and potentially holding inventory that will change in price (up or down), not to mention storing many items we have never had to store before.
We are also experiencing the same labor shortages that everyone else is. In manufacturing, some of the biggest shortages are in finding production workers and welders. So many of us have doubled down on our recruiting efforts. At Westmor Industries, for example, we offer training to those who don’t have any experience. Our goal is to train new welders for our industry and help them get their required certifications. We are going to these great lengths to keep up with the products our customers need us to deliver. But even with the extra effort, demand is still outpacing supply in
many cases.
Further downstream, we are concerned with propane supply and the ability to get that supply wherever it’s needed. Propane transports help to mitigate supply challenges. Having them readily available allows the product to be moved wherever it needs to go. Without them, that would not be possible. However, on the receiving end of propane transport, there needs to be an adequate amount of storage … that is, if you can get access to additional storage tanks right now.
Going back to our supply chain challenges, it’s more difficult than it has been in some time to get industrial-sized propane storage. Manufacturers are suffering the aforementioned supply chain challenges and labor shortages, which adds up to the inability to produce what is needed.
Outside of those challenges, if you can get additional storage capacity, it is absolutely one way to be able to respond to unpredictable crop drying, cold-weather periods or other potentially catastrophic events. In 2022, it does seem like a particularly good idea to make sure that supplies are full or full-plus from what we are accustomed to.
Extra preparedness in an environment that has been fairly volatile seems like a good decision. It appears to be a simple answer, but if you have the trailer and truck fleet, as well as storage to help with supply, generally that equals success. However, that still leaves the challenge of labor shortages at play.
We are short of qualified drivers as an industry and in the larger economy. There have been some changes to the commercial driver licensing (CDL) process, which were intended as improvements, but as with most “improvements” by the government, there can be unintended consequences. In our case, the process to obtain a CDL with a hazmat endorsement is even more time-consuming and costly. And because there is such a demand for qualified drivers across all industries, we may not be able to keep them no matter what
we do.
Almost everyone is working double time to recruit more. With inflation, there’s more risk than ever to lose them to the highest bidder. On top of all of that, there is still a lack of people seeking blue collar jobs.
To add to the concern, President Joseph Biden’s administration has told the National Propane Gas Association that moving forward, hours-of-service waivers will be much harder to come by. This is likely to worsen your average, run-of-the-mill shortages caused by high moisture content of a given year’s harvest — distinguished from an emergency shortage during an acute extreme weather event.
That said, the more transports and storage facilities there are, the more prepared we can be to respond to supply challenges and move product into areas where it is needed most. Bulk transport companies should make an effort to right-size their fleets. Many fleets that haul liquefied petroleum gas (LPG), usually through acquisition or similar, have trailers that are designed to haul ammonia or what we think of as a “dual-purpose” trailer (used for LPG and NH3).
These trailers are heavier and/or smaller than a trailer designed for LPG only. In an 80,000-pound jurisdiction, an LPG-only trailer can be as much as 2,000 gallons larger than a trailer designed for NH3-only and 1,000 gallons larger than a dual-purpose trailer.
Trucks with sleepers also reduce the amount of product that can be hauled because they are heavier than a day-cab tractor. This is not a problem that fleets can solve between July and October. It’s a long-term, strategic fleet planning effort to maximize the efficiency of bulk transport operations.