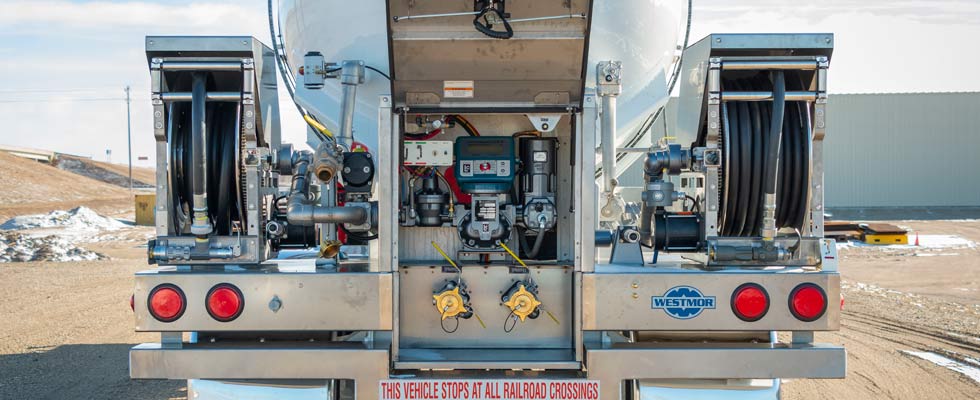
The industry doesn’t get anything done without this delivery workhorse. And in the current labor market, any features and technology that improve the bobtail operator’s experience are paramount to success. This month, Jason Soulon — sales manager, Southwest region, for Westmor Industries — answered some of BPN’s most pressing questions regarding bobtails, ongoing manufacturing challenges and new features coming online. Read more below.
What initiatives have potential to alleviate the industry’s driver shortage?
Westmor’s customers and industry contacts have talked a lot about driver shortages. There have been some changes to the commercial driver’s licensing (CDL) process, which were intended as improvements. But there can be unintended consequences. In this case, the process to obtain a CDL with a hazmat endorsement is more time consuming and costly. Even if those obstacles can be overcome, there is still a lack of people seeking blue collar jobs.
Some of our recent innovations have aimed to address this issue by reducing physical strain on the operator, and other solutions are designed to increase productivity to help reduce the demand for drivers. At the National Propane Gas Association’s Southeastern Expo, we launched our Blueline Distribution Trailer. The standard model features a 6,000-gallon cargo tank — nearly twice the capacity of a typical single axle bobtail.
That means fewer trips to the bulk plant, opportunities to consolidate routes and the versatility to supplement transport loads when needed. The trailer has the same features and functionality as a conventional bobtail.
How can our industry better recruit bobtail drivers?
Being a bobtail driver is hard work. Drivers wake up early, work long days and sometimes make emergency deliveries in the middle of the night. When the weather is at its coldest, drivers are out in the elements making sure their customers are taken care of. Anything we can do to make that job easier, safer, more ergonomic and more comfortable will make it easier to put more drivers behind the wheels of industry vehicles.
Is Westmor experiencing material delays or logistical issues in getting supplies for bobtail production? how are you navigating this?
Yes — we all are. One of the most challenging aspects of the supply chain crisis is the frequency and variations of material delays. One day the problem is a chassis; the next day it’s a meter; the next day it’s a hose reel; and so on. We are constantly adjusting production schedules to deal with the shortages.
One way to combat the supply chain situation is to carry more inventory, but that creates other issues with warehouse space, and it requires more capital. We’ve increased our commitments for chassis, raw materials and equipment to provide larger buffers in our production schedule, but demand is still outpacing supply in many cases. Another issue is the lead time for major components, which has increased significantly. Lead times that used to be four to six weeks are now as long as 20 weeks. This makes it nearly impossible to react to changes in the market.
On top of that, many suppliers have increased prices substantially and regularly receive notices about additional surcharges, especially on aluminum and stainless steel. The long lead times and volatile costs make it difficult to predict pricing more than several months ahead.
We’ve gotten more creative with items that are in extremely short supply. For example, we would normally purchase chassis from a few truck dealerships, but now we’re purchasing chassis from numerous dealerships. The aforementioned Blueline Distribution Trailer is another example; in some cases, a single trailer and driver can replace two bobtails and drivers. And if your fleet has underutilized tractors, then you could avoid the long wait for a new chassis and get more value from existing assets.
Are there any other industry trends that your team is paying attention to?
- More payload — There’s a lack of drivers, and we don’t expect that situation to turn around anytime soon. We’re looking for more ways to help our customers accomplish more work with fewer people.
- Customization — Our customers are able to get exactly what they want from us to meet their needs. Often, this requires customization because what works for one marketer doesn’t always work for another marketer. Every operation is different from the next, requiring different tools to be as efficient as possible.
- Safety — No one wants to be injured, have their employees return home in worse shape than when they came to work or have something happen that could injure a customer or damage their property. It’s more important than ever to ensure the safest operation possible, and there are so many options to make that a reality. We’ve been staying in front of emerging technologies so we can make those systems available.
- In-cab technologies and back-office software — Understanding the many different technologies and how they work with trucks and trailers is hugely important to our customers. Marketers rely on hardware and software to run their businesses. As with any technology, they are constantly evolving and commonly require some level of customization. We frequently educate ourselves on the most common technologies and train our employees to install and support the ever-changing technologies so we can take that pain from our customers.
Do you see any gaps in safe bobtail operations that could be improved with new equipment features or increased training?
There is usually more that can be done to prevent accidents. In many cases, simpler is better and simpler is safer. With training, more is usually better, but simplicity trumps complexity. We have been hearing from some customers that education is just as important as training. Yes, you need to check the training boxes, but critical knowledge can be missed if that’s all you’re doing. It’s important to talk about why you’re training. Those discussions might help you to avoid accidents, especially in situations that might be a little out of the norm.
What new features on your trucks have you announced recently that our readers need to know about?
We are focused on featuring our Blueline Distribution Trailer. These types of trailers have been around in some form for decades, but Westmor has evolved the design to alleviate challenges with driver and chassis shortages. The payload can reduce the demand on your bobtails or free those bobtails up so they can be used to grow gallons in other markets. Plus, the trailer will reduce trips to the bulk plant, allowing more efficiency. It has the same features and options as our Blueline Bobtail, but it’s a trailer, so you don’t need to wait for chassis availability to deliver propane. If an operation also delivers refined fuels, then our Transtech Distribution Trailer addresses the same concerns. Additionally, the Pathway Delivery System — a swiveling hose reel — addresses several concerns, like driver ergonomics and safety. A turntable underneath the hose reel allows the driver to position the hose reel at the best angle for each propane delivery. When the customer’s tank is anywhere but behind the bobtail, the driver can either pull the hose straight out and then walk to the side or pull the hose to the side while exerting extra effort to overcome the friction of the hose against the rollers and the resistance of the hose reel itself. This becomes more difficult with longer hose pulls, especially in winter, and it causes unnecessary stress and strain on the operator, which can lead to injury.
Are there any changes to current bobtail models necessary to allow for the use of renewable propane?
The type and blend of renewable propane are the primary factors for material compatibility. In some scenarios, the elastomers in valves and fittings need to be upgraded. In other cases, no changes will be necessary. We will continue to stay in front of emerging markets and technologies so we can provide what our customers need or will need.