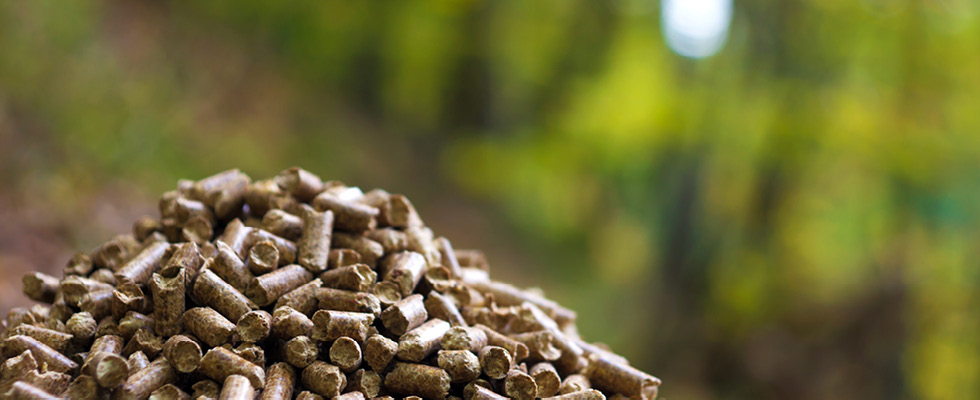
Perry, Florida, a small town located in Taylor County, is nestled in the Big Bend region of the state where the panhandle curves into the peninsula. Approximately 50 miles southeast of Tallahassee, Perry is part of a rural area known for its natural beauty and proximity to the Gulf of Mexico. The city has historically been a hub for forestry and logging activities, earning the nickname “Tree Capital of the South.”
In recent years, Perry has faced significant challenges due to hurricanes. Hurricane Helene, a powerful Category 4 storm, made landfall near Perry in September 2024, causing widespread damage with winds reaching 140 miles per hour and storm surges of up to 15 feet. This followed Hurricane Idalia in 2023 and Hurricane Debby earlier in 2024, marking a period of repeated devastation for the region. The economic impact of these hurricanes has been substantial.
Adding to the economic strain, the Foley Pulp Mill, a major employer in Perry, permanently closed in late 2023. The mill had been a cornerstone of the local economy, providing 525 direct jobs and supporting many others in related industries. Its closure has led to significant economic repercussions, including the loss of over 1,000 jobs in Taylor County and a decline in local GDP by 15%. The shutdown of the mill has also impacted state-level economic activity, with estimated losses of $571.8 million in industry output.
Taylor County faces a challenging economic and employment outlook. The unemployment rate has risen to 6.5% as of February, as the region struggles to recover from the dual impacts of natural disasters and industrial decline. Efforts are underway to attract new businesses and diversify the local economy, but the path to recovery will require resilience and innovation.
Biopropane Production: Politics & the Laws of Physics
Alkcon Corporation was formed in 2013 in Nevada. At that time, there was a growing concern over the methane gas (CH4) releases from oil and gas production, farms and landfills. In 2014, former President Obama’s administration released the “Climate Action Plan: Strategy to Reduce Methane Emissions.” Legislation at various levels of government was being drafted to financially penalize those responsible for uncontrolled methane releases.
Methane is ubiquitous and is familiar to most of us as natural gas. Many cook with it and heat their homes with it. Compressed natural gas has been accepted as a viable motor fuel. In the right place, methane is a beneficial gas. But what about the unwanted methane gas released to the environment? In 2013, the oil and gas industry flared off $3.6 million worth of natural gas every day during the Bakken oil rush in North Dakota.
The C-H bond holding methane together is strong. To utilize methane as a chemical process intermediary, the chemical bond energy of about 415 kJ/mol (kilojoules per mole) must be overcome. For example, at temperatures of 700 C to 1,000 C, methane can react with carbon dioxide in the presence of a catalyst to produce synthesis gas, a mixture of hydrogen and carbon monoxide. In simple terms, methane is a tough nut to crack.
Nevertheless, it is possible to use methane to generate other fuel, such as propane. Gas plasma discharges, especially nonthermal plasmas, create highly energetic electrons, which act as an efficient “catalyst” that can activate methane under room-temperature conditions. Methane activation generates highly active radical molecular species, which can recombine into higher alkanes. Moreover, adjusting the electron energy can alter the product distribution of methane activation via gas plasma.
For example, when methane is activated in a gas plasma discharge, a methyl group is formed. When two methyl groups combine, ethane is formed and hydrogen is released:
2CH4 + e- (plasma) -> 2CH3• + 2H• CH3• + CH3• -> C2H6
When ethane is activated in a gas plasma discharge, an ethyl group is often formed. When methyl and ethyl groups combine in a second reaction, propane is formed:
C2H6 + e- (plasma) -> C2H5• + H• CH4 + e- (plasma) -> CH3• + H• CH3• + C2H5• -> C3H8 (propane)
Propane can be produced from methane via this two-stage reaction, without the use of a complex metal or organic catalyst. Both reactions occur to various degrees in the first reactor. Ethane is produced in the first reactor as a majority product, along with a minor amount of propane and butane(s). The ethane is then oligomerized to propane in a second reactor. Propane and butane can be liquefied and separated from the gas product streams from both reactors via simple compression.
In 2016, Alkcon Corporation submitted a proposal to the Department of Energy in response to grant opportunity DE-FOA-0001417. The proposal described a small-scale gas conversion system that could be deployed globally and installed at a methane source. The system would have converted methane to propane via a gas plasma conversion process. Such a system would allow flaring gas from petroleum wells to be converted to propane, thus creating a pathway to monetize methane, which would have otherwise been flared off. The proposal was rejected.
Later that same year, the proposed bench-scale reactor was designed, fabricated and tested in a self-funded effort. The Alkcon plasma reactor converts methane to a product stream consisting of ethane and lesser amounts of propane and butane(s). The major innovation, when compared to other plasma reactors, is the “reaction jet” design. This design allows the C2 and C3 alkane products to exit the reactor, thus avoiding any additional interaction with the plasma. The reactor also does not employ a metal or organic catalyst, making it suitable for use with gas streams that might contain trace amounts of sulfur compounds, which deactivate complex catalysts.
In the end, the use of an electrically-driven plasma reactor can reduce the energy requirements to activate methane when compared to a thermal-catalytic system, especially when the gas plasma reactor incorporates a selective catalyst. However, the amount of energy required to activate methane at a commercial scale as a feed gas for the production of propane is simply impractical, regardless of the energy source. That being said, there may be small-scale, niche applications where plasma processing of methane may still be viable.
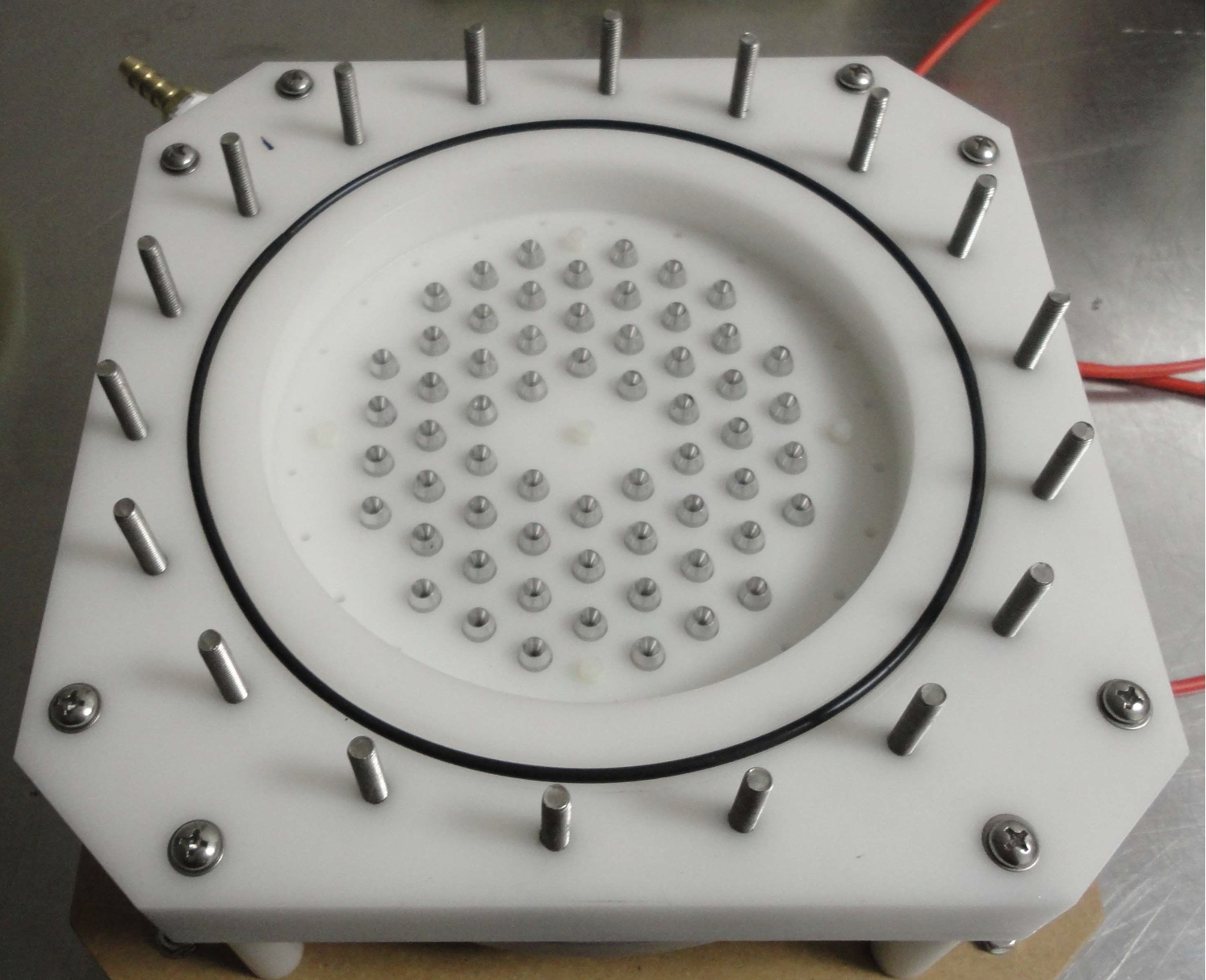
With the change of the administration in 2016, federal government support for biofuels waned, there was less interest in sequestering methane releases and there was no clear path to public or private funding, given the market for biofuels in the United States. Alkcon Corporation relocated to Florida in an effort to reduce costs. The relocation also allowed the company to be closer to potential business partners in Europe, where there was still a promising market for biopropane.
Biopropane Production: Can It Scale Economically?
Over the adjoining years, Alkcon Corporation continued to explore novel and alternative pathways to produce biopropane. New feedstocks, chemical processes and catalysts were considered. The capital cost, adequacy and efficiency of each process configuration were analyzed. The price of the biomass, transportation costs and energy inputs requirements at commercial scale were all considered and modeled. The gasification of biomass, coupled with a thermo-catalytic system, was determined as the most viable and efficient pathway.
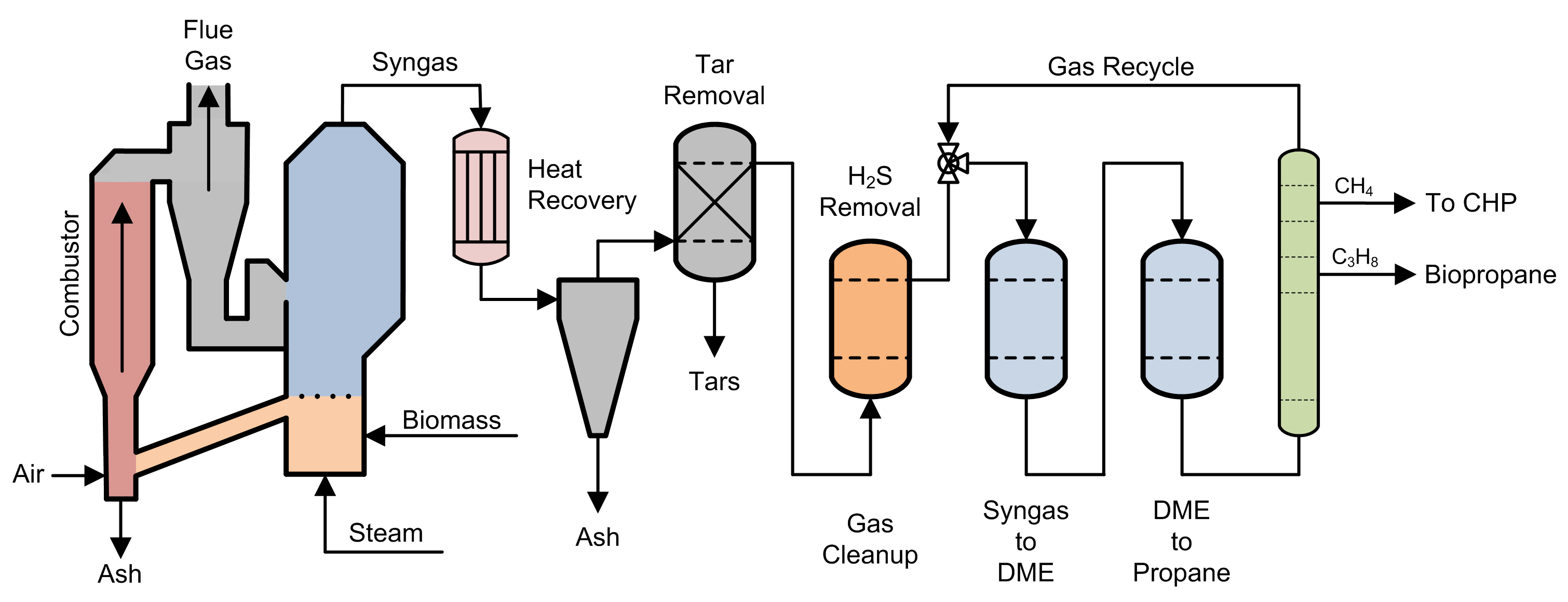
Woody biomass and forestry residues from managed forests were selected as the feedstock. This type of material is readily available in North America in large volumes at a low cost per ton, and the transportation and handling (cutting, logging, hauling and chipping) of woody biomass at commercial scale are well understood. The skilled labor and equipment to harvest, transport and process woody biomass at an industrial scale are readily available as well.
The process of converting woody biomass into biopropane is comprised of two main steps. The first is the conversion of woody biomass to synthesis gas (syngas) through gasification. The second is the conversion of syngas into biopropane via a thermal-catalytic process.
Syngas is composed of carbon monoxide, carbon dioxide, hydrogen and methane. This gas mixture is a common starting point for alternative fuel synthesis. We selected a dual fluidized bed (DFB) steam gasifier for generating syngas, as the yield of hydrogen is high and the production of unwanted tars is low in this type of gasifier. A DFB gasifier employs superheated steam to break down the hemicellulose in woody biomass. The increased hydrogen production rate is due to the water gas shift (WGS) reaction that occurs more prevalently in this type of gasifier. During the WGS reaction, carbon monoxide reacts with water to produce carbon dioxide and hydrogen gas.
The raw syngas from the gasifier contains wood ash, heavy tars, hydrogen sulfide, aromatic compounds and unsaturated hydrocarbons, which need to be removed from the gas stream prior to its introduction to the catalytic fuel synthesis reactors. A cyclone is used for separating heavier particulates from the gas stream by centrifugal force. Electrostatic filters and particulate filters are used to remove fine particles of dust and ash. Wet scrubber systems are used to effectively remove tars and oils from the synthesis gas. Catalytic cracking can be employed to convert aromatic compounds and unsaturated hydrocarbons into syngas.
Syngas is then converted to biopropane via a two-step, thermal-catalytic process. The first stage consists of a CuZnAlOx and ZSM-5 catalyst operating at 410 C and 725 psi in a stainless-steel reactor vessel, where synthesis gas is converted to dimethyl ether (DME). The second stage consists of a SSZ-13 zeolite catalyst operating at 260 C and 725 psi, also in a stainless-steel reactor vessel, where DME is converted to propylene and then hydrogenated to propane. This process was developed by Dr. Wenliang Zhu and Dr. Zhongmin Liu at the Dalian Institute of Chemical Physics in Dalian, Liaoning, China. This two-stage catalytic system exhibited excellent stability during a 200-hour test on stream.
The output of the second reactor is passed through a distillation tower where the biopropane product and methane are removed from the process gas stream. Unreacted syngas components are returned to the first reactor for catalytic reprocessing. An odorant is added to the biopropane product to meet federal requirements. The methane separated from the gas stream is fed to a gas turbine combined heat and power system to provide up to 1 megawatt of electrical power for the system.
With the DFB steam gasifier digesting 220 tons per day (about 75,000 tons annually) of woody biomass, a system of that scale could produce from 10 to 15 million gallons of low-carbon biopropane annually. The process is rate limited by the available hydrogen in the system. Shredded polyethylene, procured from sorted municipal waste streams, could be co-fed with the biomass to also increase the available hydrogen in the system, but this may also lower the Carbon Index (CI) of the biopropane product.
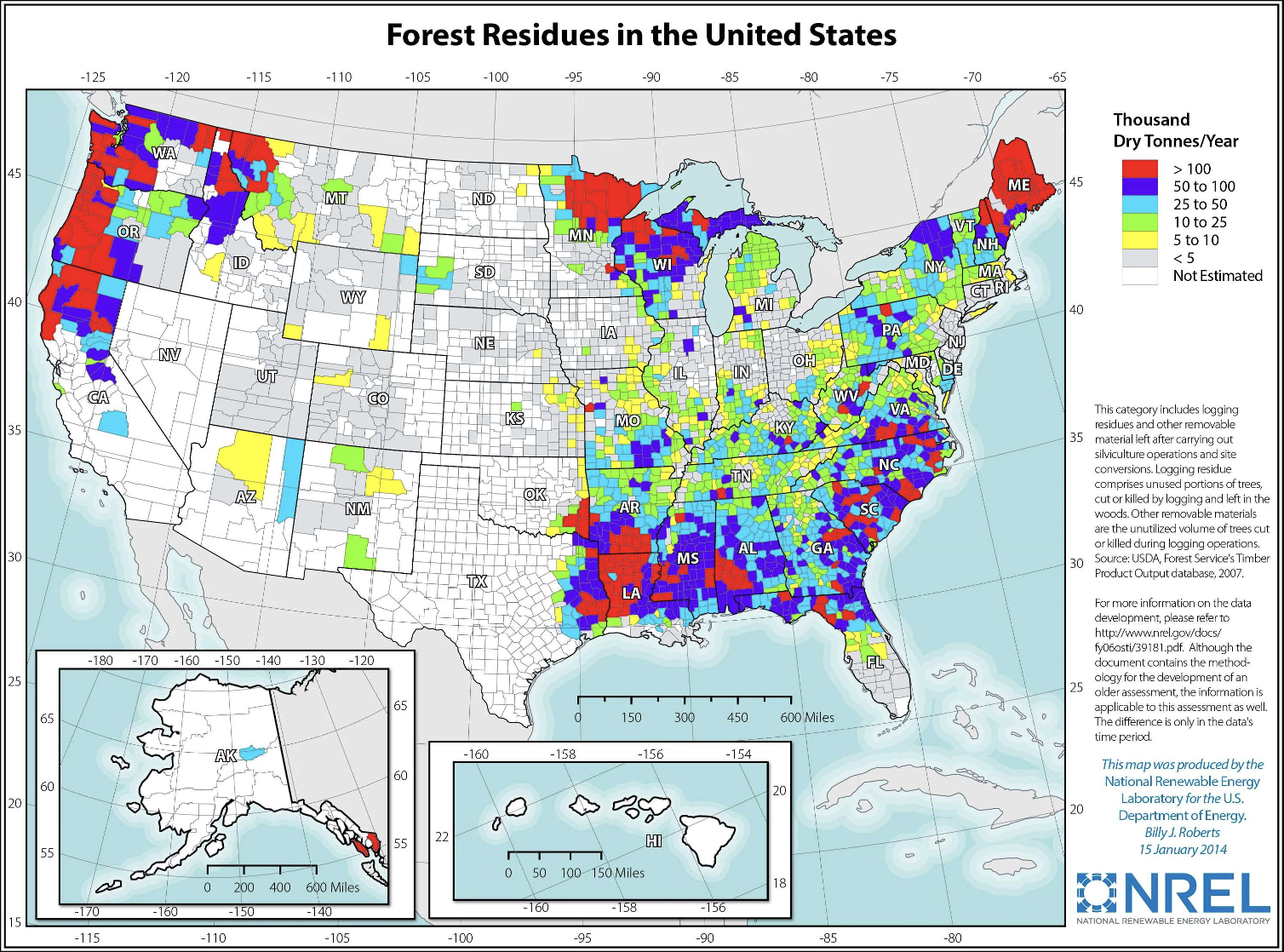
In areas where commercial power is available, a steam methane reforming module could be added to the system to increase the available hydrogen by converting the methane stream to additional hydrogen.
Biopropane Production: Coming to a Town Near You
According to data available from the National Renewable Energy Laboratory (NREL), there are millions of tons of forestry wastes readily available around the United States that could support a distributed system of biopropane production facilities. In the state of Maine, there are an estimated 3.3 million tons of forestry wastes available on an annual basis. That is enough biomass to supply the PADD 1A region with 440 million gallons of biopropane annually. In the Midwest, NREL estimated there are 3.25 million tons of forestry wastes available on an annual basis in northern Minnesota. That is sufficient biomass to supply the PADD 2 region with 430 million gallons of biopropane annually.
On the West Coast, there are over 4 million tons of forestry wastes available on an annual basis across northern Minnesota, Washington and Northern California. That is enough biomass to supply the PADD 5 region with over 500 million gallons of biopropane annually. In central Louisiana, there is an estimated 8.4 million tons of forestry wastes available on an annual basis. Over 1 billion gallons of biopropane could be produced in the PADD 3 region with that amount of biomass.
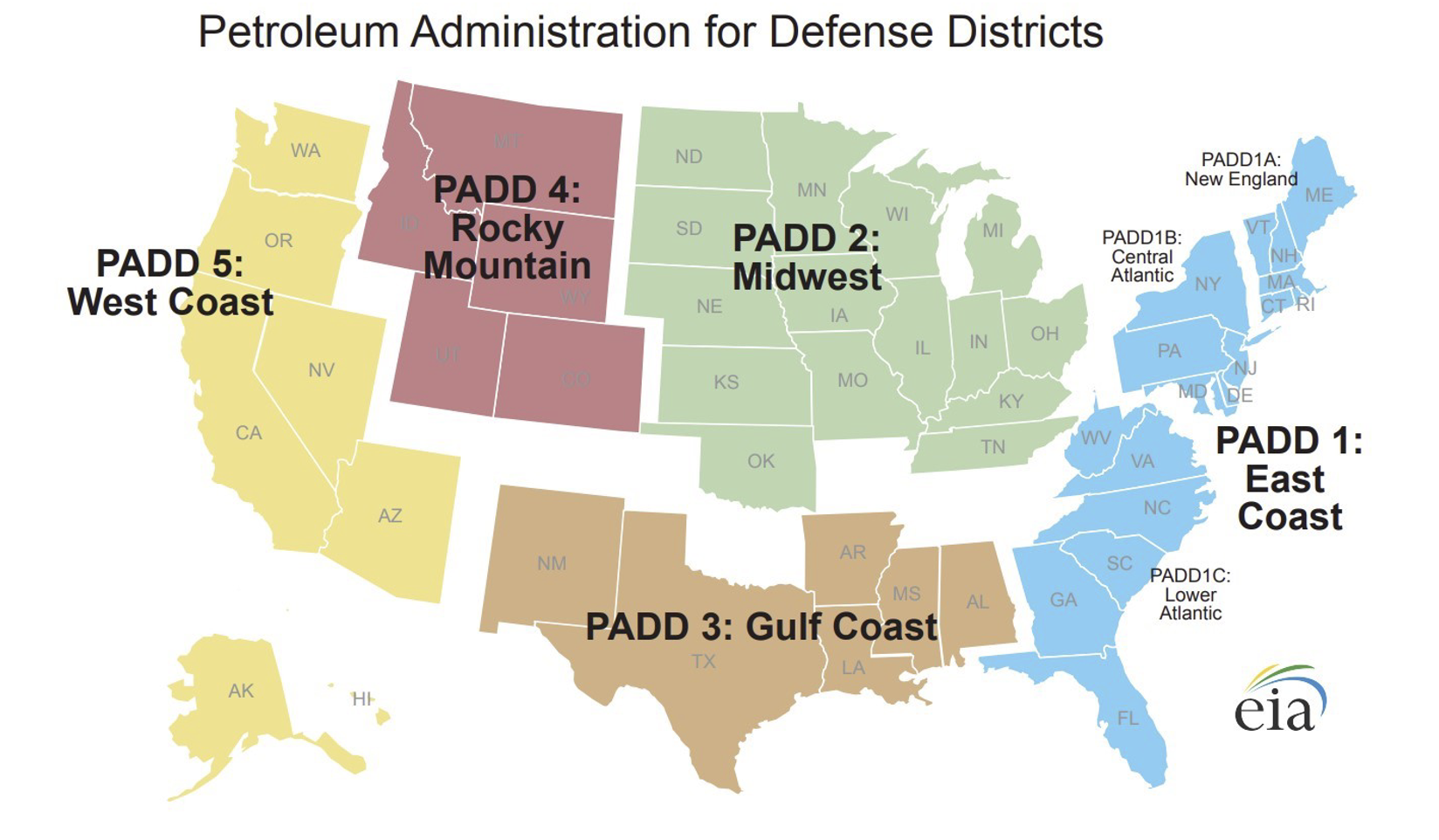
And that brings us back to Perry, Florida. According to information available from the Taylor County Development Authority, the panhandle region of northern Florida “has supplied over three million tons per year of pine pulpwood, chip-n-saw and saw timber annually for over 70 years.” That would be sufficient biomass to supply the PADD 1C region with 400 million gallons of biopropane annually. The now closed Foley Pulp Mill likely consumed somewhere in the range of 1.7 million U.S. tons annually.
A 50-acre lot, which is owned by the City of Perry, is located immediately adjacent to the Foley Pulp Mill property. Seeing the opportunity, Alkcon Corporation created a site development plan for the 50-acre lot and a simple economic analysis, based upon the information available at the time. The plan called for the construction of a total of four gasifier and gas processing chains on the lot. Each gasifier and its associated gas processing chain were to be completed each year.
The completed facility, with four gasifiers operating at full capacity, would consume approximately 880 tons of biomass daily. Regardless of harvesting costs and variations in wood density by region, biopropane production facilities with an annual production rate of 40 to 60 MMGPY are feasible in each region.
The recent average Mont Belvieu, Texas, spot price for propane is around $0.90 per gallon. The Renewable Identitification Numbers credits (when available for this process) and the Low Carbon Fuel Standard subsidies for biopropane with a low CI score amount to approximately $2.10. When combined, these create a value of about $3.00 per gallon. Thus, the total revenue for the proposed biopropane plant in Perry, Florida, would be about $150 million annually.
The cost of delivered woody biomass to Foley Pulp Mill was about $40 per ton. The total cost for the biomass for the proposed biopropane plant would be about $12 million annually. The complete facility would likely employ about 150 people, working three shifts — keeping the plant operating 24/7, with an expected uptime greater than 90%. The median salary range for the skilled labor workforce at the proposed plant might be $45,000 to $65,000. This puts the basic annual payroll expense at approximately $8.25 million, plus benefits.
When Alkcon Corporation proposed the biomass-to-biopropane project to the city manager of Perry, Florida, in 2023, he replied, “I feel like we need to get more people involved, but I’m not sure who.”
To read more about the process of using plasma technology to reform methane, check out this article. Additionally, researchers based in China also published an article exploring the conversion of syngas into propane.