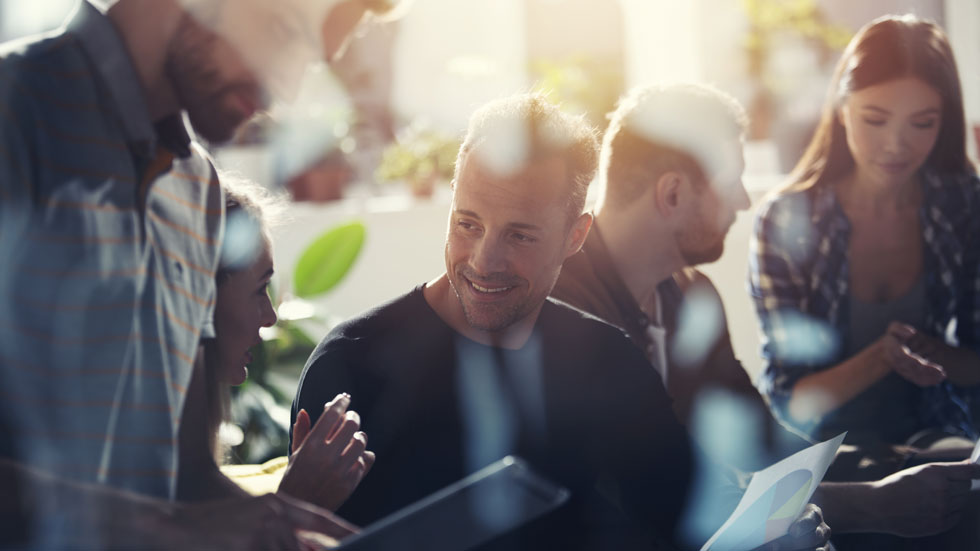
The propane industry is full of potential hazards. By promoting workplace safety, you can help reduce on-the-job injuries. Leading, advocating and encouraging safe behavior is an important step toward keeping your employees healthy and injury-free. What’s more, promoting workplace safety will help boost employee productivity, forestall expensive insurance claims and keep insurance premiums in check.
As a bonus, loss control at the workplace can help prevent or reduce the possibility of a loss or help reduce the severity of a loss if one does occur. Who wouldn’t sign up for this? The following article lists steps your management team can take to foster greater workplace safety and loss control.
1. A Workplace Safety Plan
Engage the services of loss control professionals to help create a workplace safety plan to aid in reducing accidents and workers’ compensation claims. A proper workplace safety plan should begin with a hazard assessment conducted by a loss control consultant, along with a safety committee and employees with experience and a desire to improve safety for all. A great starting point is engaging your trusted agent or broker for assistance.
The identification of potential risks and hazards to your employees will help you to lay the foundation for your plan. It is not surprising that risks and hazards will vary depending on the workplace environment. For example, a propane tank farm will pose different risks than a retail or office environment.
Threats and hazards can be obvious. They include slippery floor surfaces, poorly secured shelving, inadequately ventilated workspaces, difficult-to-access tools and materials and tripping hazards, among other issues.
Your company’s workplace safety plan should have a custom-fit feel for your employees, so it addresses not only the unique aspects of your workplace but also your organizational culture. It should also ensure all compliance components of both federal and local jurisdictions are addressed. Failure to do so will not only result in a failed safety effort but also in substantial fines and penalties.
Like most plans, this one is easy to describe but can be difficult to execute. Once problems or risks have been identified, efforts should be directed towards generating solutions. Responsibility for managing the plan should be assigned to the safety committee, which should also be tasked with making sure the action plan is being effectively carried out.
While others may carry it out, experience tells us without consistent senior executive attention and prioritization, safety processes fail almost 100% of the time.
Conversely, the chance of improving an organization’s safety process and outcomes increases exponentially with senior management support. There is truly no substitute for demonstrating the commitment to a safe work environment at the executive level.
2. Training & Implementation
Training employees to became aware of and to adhere to loss control guidelines is a critical element of your workplace safety plan. It is only through rigorous training, follow-up and encouragement you can ensure your employees will keep safety top-of-mind throughout the workday no matter the situation and no matter the stress of operations.
The workplace safety plan will fail without consistent and updated employee training. Training should clearly identify the full set of workplace hazards for employees through words and visuals and should be refreshed at regular intervals.
Those who are most vulnerable to accidents typically ride on the outside of your demographics: the new employee and the long tenured. Without adequate training, the first group will not have the necessary awareness. The second group thinks it knows it all, which often results in hazardous efforts to shortcut the process.
3. Communications
Effective communications are an essential element in establishing a comprehensive safety system. By posting reminders and warnings about safety throughout the jobsite, you will emphasize to employees the importance of following the company safety plan.
Communications outreach should be consistent, frank and transparent, and it should create meaningful dialogue on issues identified for resolution. Employees can recognize a “puff piece” from a mile away.
4. Recordkeeping
Accurate and detailed recordkeeping is a vital element of every workplace safety program. It is also necessary in satisfying Occupational Safety and Health Administration standards and additional regulatory requirements.
Recordkeeping creates accountability and effective business management, while memorializing results for safety inspections and insurance audits. In addition, recordkeeping constitutes its own form of loss control. Employees will gain the ability to learn from valuable past experience, and management will be able to identify and prevent potential future issues.
Moving Forward
A formal workplace safety plan provides a baseline when evaluating incident reports and workplace injuries. You should review your plan frequently so you can shift resources to address issues as they develop. Make safety communication a daily experience for your operations.
Formalize and discuss safety at management meetings before any other business issues are discussed. Conduct weekly safety meetings and shift specific or function-specific safety meetings so ideas and best practices are shared and spread through the organization. Your workplace will become safer over time if you work your safety plan consistently.
Enlist the aid and guidance of your trusted agent or broker from planning your workplace safety plan through recordkeeping. Their expertise will help to ensure the safety of your employees.