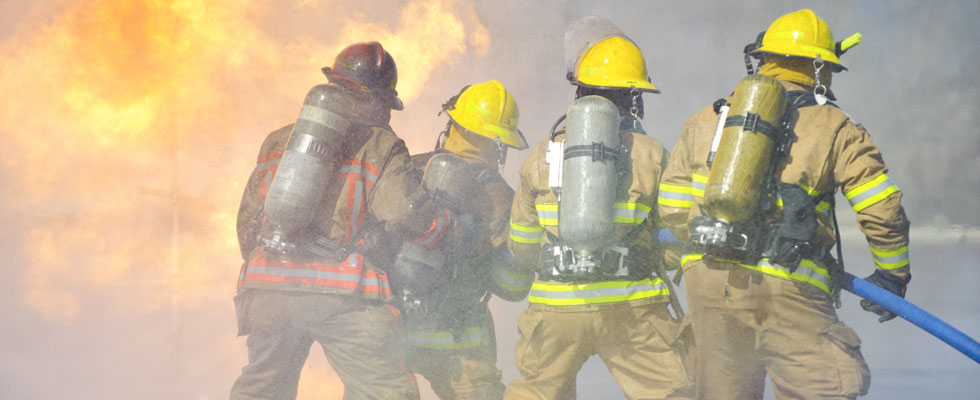
In 1937, Walter Cronkite, then a cub reporter for United Press International, surveyed the scene of an explosion in New London, Texas.
Cronkite went on to win fame as a war correspondent covering World War II in Europe and later as a national network news anchor back in the United States.
But he remembered the event many years later, saying, “I did nothing in my studies nor in my life to prepare me for a story of the magnitude of that New London tragedy, nor has any story since that awful day equaled it.”
The main building at the New London School had been destroyed in a natural gas explosion. At least 294 people, mostly students, were killed.
Hundreds more were injured. The tragedy is universally credited with prompting laws for the mandatory odorization of natural gas and propane in the U.S.
State-of-the-Art School System
In 1930, large oil deposits had been found in the New London area. There were soon oil wells everywhere — including 15 on school district property). Oil money quickly boosted the local economy (and the school district’s budget) to such an extent that in 1932 (during the depths of the Great Depression), a brand new, state-of-the-art school was constructed to house students in the first grade through the tweflth grade.
Reportedly, by that time, the school district was the wealthiest in the nation. The grounds of the new school were complete with a football stadium that was the first in the state of Texas to have electric lights.
The school was built on sloping ground, and there was a large open space beneath the structure. The open area ran the entire 253-foot length of the building.
Fatal Decision
The original plan was to heat the school by means of a steam boiler system. However, the school board overrode this plan and decided to install 72 gas heaters throughout the building. The gas was supplied by United Gas Company for a fee of $300 per month.
All was well with the new school system until January 1937, when the school board made a fatal decision. In order to save the $300 per month fee, the board cancelled its gas service with United Gas and had plumbers tap into a residue gas line owned by one of the drillers on its property, Parade Gasoline Company.
The tap was not authorized by Parade Gasoline Company, but such taps were common practice at the time, and most drillers winked at them.
Back then, the natural gas extracted with the oil was generally considered to be a valueless waste product and was flared off. The raw gas that now fed the school’s heaters varied from day to day in quality. More significantly, the gas was not odorized.
Leaking Tap
Tragically, the tap was not only unauthorized, but it was also not installed properly, and it was leaking. The leaking gas migrated into — and ultimately filled — the large open space beneath the main high-school building. For some time prior to the explosion, students complained of headaches. However, little notice was given to these early alarms.
On the afternoon of March 18, 1937, there were at least 500 students and about 40 teachers in the main building. By good fortune, the students in the first grade through the fourth grade had been given the afternoon off.
A PTA meeting was being held in a separate gymnasium, which was not seriously damaged in the explosion.
At 3:17 p.m., a shop teacher turned on an electric sander. This is generally accepted as the source of ignition for the devastating explosion that followed.
The Explosion
The walls of the school bulged, and the roof first lifted and then crashed back down. The building collapsed. The explosion was heard four miles away, and it was so powerful that a two-ton block of concrete was hurled 200 feet away from the building, where it crushed a 1936 Chevrolet.
Those in the PTA meeting rushed to the scene, and within minutes, local residents started to arrive to assist in the desperate rescue and recovery efforts, mostly digging through rubble with bare hands. Oil field workers, discharged from their jobs, soon joined the effort with heavier equipment to move concrete and steel.
The governor sent in the Texas Rangers, the highway patrol and the U.S. National Guard. Thirty doctors, 100 nurses and 25 embalmers arrived from Dallas, Texas. It took over 17 hours to clear the entire scene.
Aftermath
Seventy lawsuits were filed against both the school district and Parade Gasoline Company, but it was a different era then, and the lawsuits were quickly dismissed.
However, the school superintendent was forced to resign — he had lost a son, a niece and a nephew in the explosion. The U.S. Bureau of Mines investigated and quickly discovered the faulty tap on the residue gas line.
Within weeks, the Texas legislature acted. It enacted a registration act to regulate the practice of engineering, due to the improper installation of the tap. More importantly for our industry, it mandated the odorization of all gas used for residential or commercial use.
Other states, as well as the federal government, quickly followed this odorization requirement. Today, these requirements are uniform and well-established in all parts of the country as part of our industry’s safety infrastructure.
The event that prompted these requirements is remembered as the most catastrophic school disaster to occur in the history of the U.S. Today, a museum and a memorial in New London commemorate the disaster.