The COVID-19 pandemic triggered a shift to remote working, which has boosted the adoption of virtual reality (VR) by oil and gas companies for training, collaboration and data visualization, says GlobalData. The data and analytics company notes that this shift will persist even though most employees have now returned to offices.
Ravindra Puranik, oil and gas analyst at GlobalData, comments, “VR technology is becoming commonplace in the oil and gas industry as it helps to visualize 3D simulations of real-world objects. As the industry deals with volatile substances that are often found in dangerous environments, there is a substantial concern for worker safety.”
According to GlobalData’s report, "Virtual Reality in Oil and Gas — Thematic Research," the global VR market for the enterprise segment, including oil and gas, will surpass the consumer segment by 2023 to reach $32 billion by 2030.
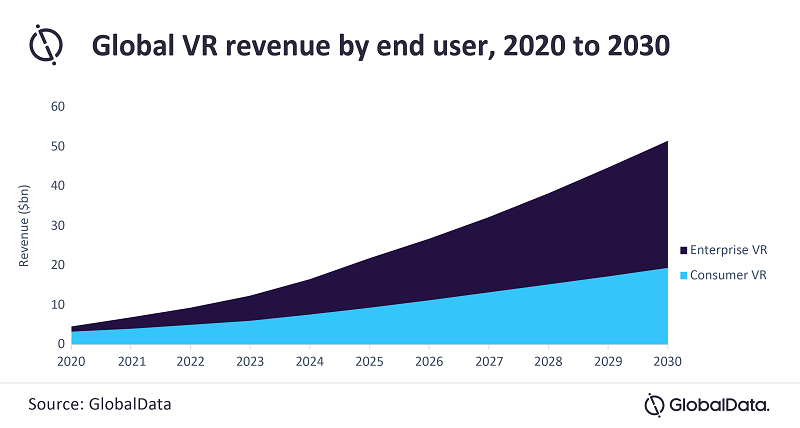
Taking a cue from the gaming industry, VR is gaining traction in the training of oil and gas personnel. Large oil and gas companies — such as Saudi Aramco, Equinor and Shell — are using VR to simulate the physical environment in training rooms.
Puranik explains, “Trainee personnel are given VR headsets that deliver an immersive experience of a facility, be it an offshore production platform, a gas processing plant or a refinery. Although this lacks the real feel of a challenging workplace environment, it is a highly safe and cost-efficient approach to introduce personnel to a new facility.”
VR enables oil and gas companies to train workers on field equipment in a simulated environment to build their situational awareness. It can help develop safety procedures at production facilities to address smaller accidents, as well as for emergency responses. VR simulation can be used to design workflows and identify bottlenecks to optimize a plant’s performance.
Puranik adds, “Digital twins is another critical use case for VR. By allowing engineers to virtually explore production facilities, VR will help in extracting the maximum value from digital twins. This could improve plant designs, fast-track the adoption of new solutions, and develop best practices for ensuring the health and safety of field personnel and surrounding communities. For instance, Shell is creating a digital twin of its integrated refinery in Singapore to facilitate remote monitoring and improve operational efficiency and safety.”